In commercial buildings, the uncontrolled intrusion of moisture into concrete and masonry walls may have costly consequences. Moisture supports the growth of mold, and causes wall coatings to blister and peel. It also saturates insulation, reducing energy efficiency. In extreme cases, moisture intrusion leads to spalling and could even necessitate wall replacement.
Coatings and water repellents are applied to the exterior of building walls to protect the substrate from deterioration, minimize the entry of moisture into the wall assembly and enhance aesthetics. Sealants supplement the protection afforded by the coatings by filling the gaps between adjoining surfaces and around flashings and penetrations—gaps that would otherwise allow unimpeded pathways for moisture to enter the building.
This article addresses the selection of coatings, water repellents and sealants based on protection, rather than aesthetics, and includes resources for identifying the brand names of candidate materials and systems.
COATING SYSTEM AND WATER REPELLENT SELECTION
Many coating systems and water repellents are available to protect the exterior of concrete and masonry walls. When selecting the materials, it must be recognized that walls move and cracks will form (Fig. 1) .

If the cracks are not sealed or bridged by the coating, they provide a direct path for moisture to enter the wall. According to a 2013 Durability + Design Magazine article, “Elastomeric Acrylic Coatings for Use on Commercial Structures,” a 20-mil-wide crack that is 3 feet long presents about the same area for water infiltration as would a one-inch diameter hole. Think of the many cracks often seen in block and along mortar joints: If left unsealed, the potential for water infiltration is enormous. The same article indicates that conventional masonry coatings are capable of bridging small cracks approximately 8 mils in width if applied heavily enough, and that acrylic elastomeric coatings can bridge cracks up to approximately 16 mils in width. Wider cracks should be sealed with specialized crack-repair materials prior to painting.
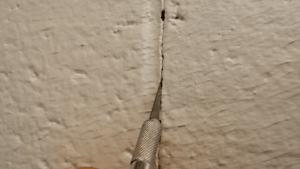
To put crack width into perspective, a dollar bill is 5 mils thick; the tip of an X-ACTO knife blade is 20 mils thick. Cracks in building walls can be much wider than this (Fig. 2), and even though most coatings are incapable of bridging these deficiencies, fine cracks are not routinely repaired in advance of painting.
Coating Materials
A few of the coating material options for building exteriors are summarized below. Some of the products are from the Master Painters Institute (MPI) qualified materials list. By typing “MPI #” and the product number into an online search engine, you will find a list of brands that have successfully completed a specific MPI laboratory testing regimen. If a specific brand is not on the list, it does not necessarily mean that the product did not pass the testing—it may have never been submitted to MPI for evaluation. When an MPI number is not available for the materials below, search keywords are provided to locate specific brands. Following the discussion of the individual materials, they are combined into systems.
- Water Repellent (MPI #34): These are thin, clear water repellents that are paintable. Typically, they are used initially on their own, but are also capable of being coated, generally in later years.
- Acrylic Block Filler (MPI #4): Block fillers are used to fill the porosity of the substrate, usually CMU. Note that for exterior use, the block filler should not contain any polyvinyl acetate (PVA). PVA is water sensitive, and could lead to blistering and disbonding if water becomes trapped beneath the film.
- Acrylic Elastomeric (MPI #113): Acrylic elastomeric coatings provide excellent weather barriers, and because of their good tensile strength and elongation, elastomerics tolerate some movement and fine cracking of the mortar while remaining intact and protective (when applied to the proper thickness). They provide a good barrier to bulk water, frequently passing wind-driven rain testing (ASTM D6904, “Standard Practice for Resistance to Wind-Driven Rain for Exterior Coatings Applied on Masonry”). Depending on the permeance of the selected product, acrylic elastomerics allow water vapor to escape through the film, especially when only a few coats are applied.
- Alkali-Resistant Water-Based Primer (MPI #3): These primers are suitable for alkaline surfaces such as concrete and masonry, and are used beneath latex or acrylic finish coats.
- High-Performance Latex (MPI #311 and #315): These high-performance latex products have good weathering characteristics, but lack the high level of wind-driven rain resistance offered by acrylic elastomerics. These materials are also suitable for application to external insulating and finish systems (EIFS). The difference in the product numbers is related to gloss (#311 is 35 to 70 units at 60 degrees; #315 is a maximum of 35 units).
- Acrylic Texture Coat (MPI #42): These products contain an aggregate, to create a textured finish on concrete surfaces such as pre-cast and tilt-up. The gloss is a maximum of 5 units at 60 degrees.
- Hydrophobic Paints (no MPI number): These products do an excellent job of protecting concrete and masonry substrates, providing water repellency and resistance to soiling, mold and mildew, while also being highly permeable, allowing vapor to escape. Search online for “lotus effect paints” or “hydrophobic paints” to find specific products.
- Silicone Resin Emulsion Paints (no MPI number): These products exhibit excellent water repellent characteristics while being highly permeable, allowing vapor to escape. Products can be found by searching for “silicone resin emulsion paints.” An acrylic silane/siloxane sealer is often applied first on porous substrates. When using silicone coatings, the same type of material is frequently used for future overcoating.
(Pigmented stains are addressed later in this article, under “Water Repellents.”)
Coating Systems
The systems shown in Table 1 are suitable for application to new vertical concrete and masonry surfaces. It should be noted that this is not an exhaustive list; systems other than those listed below may be viable. Where MPI designations exist, they are provided.
When overcoating existing coatings, the integrity and adhesion of the system should be examined to make certain that it is a candidate for overcoating. When possible, overcoating with the same generic type of coating used originally helps ensure compatibility. It also helps prevent the new material from placing undue stress on the underlying coating, and reduces the likelihood of the expansion of an underlying elastomeric coat cracking a newer (but less flexible) overcoating material.
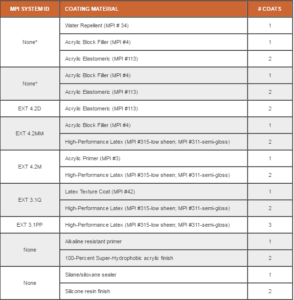
Water Repellents
When moisture intrusion becomes an issue with above-grade vertical surfaces, such as integrally colored block, stone, concrete, terra cotta, brick or other unpainted material (Fig. 3), the surfaces can be coated with a clear water repellent.
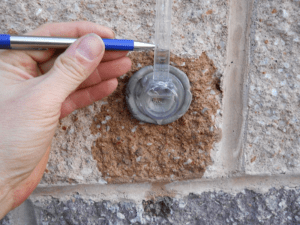
Many types of water repellents are available, such as silane, siloxane and silicone emulsions, with variations in formulation and solids content to accommodate the porosity of different substrates. Both water-borne and solvent-borne water repellents are available. Solvent-based water repellents may not be compatible with a pre-existing water-borne water repellent. If a solvent-based water repellent (such as a silicone elastomer) is desired, the existing material should be identified first to ensure compatibility.
Even when the existing water repellent type is known, it is advisable to apply a test area in advance of production work. This test helps to confirm compatibility, to agree on the appearance that results after cleaning and sealing and to determine how many applications are required to achieve the desired water-repellent characteristics. A RILEM tube may be used to determine whether adequate resistance to absorption is being achieved, or if additional applications are required.
With regard to appearance after cleaning—especially when removing efflorescence, calcite stains or lime run—the cleaning process can change the color of integrally colored block (Fig. 4). When this occurs, a pigmented stain may need to be applied prior to applying the water repellent. Accordingly, proposed cleaning methods should be evaluated prior to wholesale cleaning.
If the mortar joints or masonry surface contain fine hairline cracks, water repellents will penetrate the cracks to make the surfaces hydrophobic, but will not fill or bridge them. When cracks in mortar are wider than approximately 16 mils, the joints may need to be replaced to create an effective seal. When new mortar is being installed in unpainted masonry structures, adding a water-based water repellent admixture to the mortar is beneficial.
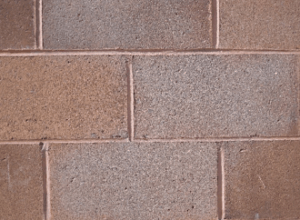
Water repellents can be paintable or non-paintable (as described below), so the potential for future painting should be considered during the materials selection. Clear materials are addressed below in items 1 and 2; pigmented stains are addressed in items 3 and 4. Although the first two materials are clear, they may darken the surface or otherwise change its appearance. As indicated earlier, a test area should be used to confirm that the appearance is acceptable prior to wholesale use.
- Paintable Water Repellent (MPI #34): These clear water repellents penetrate into the surface of the concrete, and can be painted.
- Non-Paintable Water Repellent (MPI #117): These are silane or siloxane clear water repellents that penetrate into the surface of the concrete, causing it to be hydrophobic. MPI classifies these as products that should not be painted, and used only when the surface will be resealed with the same product in the future.
- Pigmented Water Repellent Stains: These stains are available as both solvent- and water-based products. Chemistries vary, but some of the products can be found by searching online for “vertical concrete stains” and “silicone acrylic concrete sealers.”
- Mineral Water Repellent Stains: Available in many colors, these stains are high-permeance potassium silicate materials that penetrate the surface to create a hard, insoluble silicate. Products can be found by searching for “silicate mineral stains.”
JOINT SEALANTS
While coatings and various types of water repellents are applied to walls to protect them from the damaging effects of moisture, moisture may also intrude due to cracks in block and mortar joints, as well as the separation of sealants used in joints, at junctions and around penetrations.
Concrete and masonry structures are subject to stresses that may lead to unwanted cracking. Before repairs are made, cracks should be analyzed to determine the cause and whether corrective action should be taken to prevent or accommodate the movement. Otherwise, cracks may reappear in the same locations. If the cracking is determined to not be a structural problem, cracks should be repaired to reduce water penetration.
Crack repair methods vary and depend upon many factors, such as substrate type and crack width. For example, on masonry structures, cracks less than 1/16 inch can typically be cleaned using a utility knife and filled with a flexible crack filler. Cracks greater than 1/16 inch should be routed out to a minimum width/depth of 1/4 inch by 1/4 inch. In moving cracks, a sealant capable of high movement should be installed; rigid repair materials like mortar will restrict movement, causing damage to form in other areas.
Sealants used in control joints, inside corners, around openings such as doors and windows, around penetrations and at flashing tie-ins often crack cohesively within themselves or adhesively from the mating surface (Fig. 5). Separation may occur as a result of:
- Selecting a sealant that is incapable of withstanding the movement;
- Inappropriate use of backer rod;
- Inadequate joint width-to-depth ratios;
- Installing sealant without first priming the surface; and
- Installing a thin skin of new sealant over old, existing sealant.
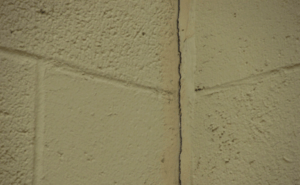
Elastomeric joint sealants are classified according to ASTM C920, “Standard Specification for Elastomeric Joint Sealants.” Classifications include Type of sealant (single and multicomponent), Grade (pourable, self-leveling sealants and gunnable, non-sag sealants), Class (+/-12 ½ percent to +/-50 percent; percentage represents the increase/decrease in joint width that the sealant can withstand), and Use (traffic and non-traffic areas, immersion service and use with mortar, glass, aluminum or other substrates).
Polyurethane sealants are typically used for vertical sealants on buildings. Sample classifications are as follows:
- Type S (single component), Grade NS (non-sag), Class 35 (withstand an increase and decrease of at least 35 percent of joint width), Use NT, M, A, O (non-traffic and tested for mortar, aluminum and other substrates). Some products are also classified for traffic (T).
- Type M (multicomponent), Grade NS (non-sag), Class 50 (withstand an increase and decrease of at least 50 percent of joint width), Use NT, M, A, O (non-traffic and tested for mortar, aluminum and other substrates). Some products are also classified for traffic (T).
For horizontal sealants at the base of walls, polyurethane or polyurethane hybrid sealants are typically used. A sample classification is as follows:
- Type M (multicomponent), Grade P (pourable or self-leveling), Class 25 (withstand an increase and decrease of at least 25 percent of joint width), Use T, M, O (traffic and tested for mortar and other substrates).
Sealant brands can be found by searching online for “ASTM C920 joint sealants.”
For optimal movement capabilities, the proper width-to-depth ratio needs to be maintained, per the building specifications or sealant manufacturer technical data sheets. Sealants are typically applied half as deep as they are wide to allow for optimal movement. Compressible closed-cell foam backer rod is used in control joints to reduce the thickness of the sealant required, to prevent three-sided adhesion and to accommodate a change in the size of the joint due to compression and expansion. Some sealant manufacturers may also require the substrate to be primed before installation of their material.
VERIFYING THE INTEGRITY OF COATINGS, WATER REPELLENTS AND SEALANTS
Selecting the correct coating, water repellent and/or sealant is one step in achieving proper protection of the substrate from moisture intrusion. Equally important are the quality of the cleaning and the application or installation. Typical inspections performed during the installation of the products are as follows:
- Quality of Surface Preparation: The surface should be evaluated to confirm that it is suitable for painting and to determine if there are any unique conditions or repairs that need to be undertaken (e.g., tuck pointing, replacement of block faces, etc.). After preparation for the application of paint or water repellent, the surface should be examined to confirm that it is clean; free of loose material, grease, oil, form release, curing compounds, laitance, efflorescence, chalk, dust and dirt; and the proper texture, if surface roughening is required.
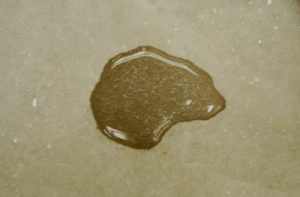
Determination of compliance is primarily visual, although freedom from organic contaminants can be established by testing with acid (examine the surface for fizzing –Fig. 6), water break (look for water absorption rather than beading) and black light (although not all oils will fluoresce).Freedom from chalk can be determined according to ASTM D4214, “Standard Test Methods for Evaluating the Degree of Chalking of Exterior Paint Films.” This test requires rubbing a clean black fabric, such as wool felt, across the surface and comparing the appearance of the residue on the fabric with an ASTM rating scale (Fig. 7).
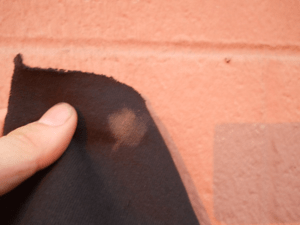
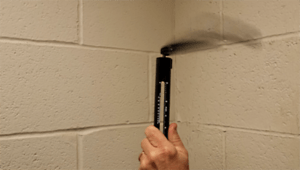
2. Ambient Conditions: Application must be done under proper conditions of temperature, relative humidity and dew point, and not during periods of dampness or when rain or frost are expected prior to drying. Ambient and surface temperature concerns include temperatures that are lower or higher than the manufacturer’s published tolerances. The surface temperature should also be at least 5 degrees Fahrenheit higher than the dew point. These assessments are made using instrumentation (Fig. 8).
3. Moisture Content and pH: Moisture content of the substrate should be compliant with the specification and manufacturer’s requirements. Visual inspections are not adequate. Determinations need to be made using instruments (Fig. 9) and/or plastic sheet tests (ASTM D4263, “Test Method for Indicating Moisture in Concrete by the Plastic Sheet Method”). In 2016, The Society for Protective Coatings (SSPC) expects to publish a new guidance document, “Field Methods for the Determination of Moisture in Concrete and Masonry Walls and Ceilings,” that will describe the types of instruments used for determining moisture content of walls prior to painting, including recommended test frequencies. The pH of new concrete can also be checked with pH paper to make certain it is not too alkaline for painting (10 or below is typically desirable).
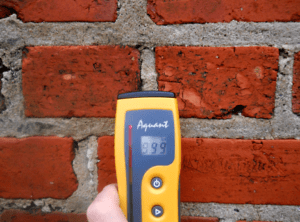
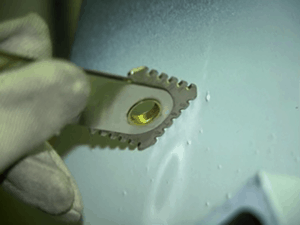
4. Proper Thickness and Number of Coats: Wet-film thickness should be monitored during application to confirm that ample film build is being achieved. Insufficient film thickness or number of coats is a common problem, and can lead to inadequate wind-driven rain resistance. Wet-film thickness is monitored using a simple wet-film thickness gage (Fig. 10). Coverage rates can also be calculated and used in conjunction with wet-film thickness measurements.
After the coating dries, its thickness can be measured non-destructively using ultrasonic gages (Fig. 11) according to ASTM D6132, “Standard Test Method for Nondestructive Measurement of Dry Film Thickness of Applied Organic Coatings Using an Ultrasonic Gage,” and SSPC-PA9, “Measurement of Dry Coating Thickness on Cementitious Substrates Using Ultrasonic Gages.”
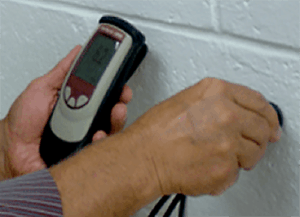
5. Dry Time and Cleanliness Between Coats: The dry time between coats should be monitored for compliance with the manufacturer’s requirements. The surface of the coating should also be clean prior to application of the next. Physical tests are not required, although a “white cloth test” could be used to help confirm surface cleanliness.
6. Coating Continuity: A common problem with systems applied to concrete and masonry surfaces is the presence of pinholes and poor coverage. Much of this can be prevented by back rolling and back-brushing to work the coating into the porosity of the substrate, coupled with thorough visual inspections to touch up flaws. SSPC is developing a new standard, “Visual Evaluation of Pinholes in a Coated Surface,” for classifying the quantity of pinholes in a finish coat together with establishing acceptance criteria.
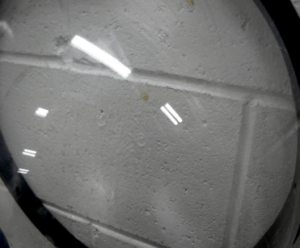
Continuity of the film can also be determined instrumentally at specific locations up to approximately 2 square feet in size by one of the methods described in ASTM E1186, “Air Leakage Site Detection in Building Envelopes and Air Barrier Systems.” The method, “Chamber Depressurization in Conjunction with Leak Detection Liquid,” involves applying a test solution to the surface and covering it with a special dome. A mild vacuum is drawn, and the formation of bubbles in the surfactant indicates that the surface is not adequately sealed (Fig. 12). The equipment can be used to reveal problem areas while application is underway, in order to improve the painting process.
CONCLUSION
The intrusion of moisture into concrete and masonry walls is a widespread problem. Apart from design issues with the building itself, causes include: improper selection and application of coatings and water repellents; inadequate repair of cracks prior to painting or sealing; and separated sealants in joints, gaps around openings and at flashing tie-ins. A number of sources, such as MPI and material manufacturers, are available to assist in selecting products by brand name, and proper installation can be confirmed through a combination of visual inspections and the use of inspection instruments.
In terms of costs, proper installation for new construction will likely cost more than is currently being experienced if compliance with the specifications is enforced—such as number of coats and thickness, proper ambient conditions during application and thorough back-rolling to seal pinholes. Maintenance costs will also likely increase, due to more thorough repairs (like tuck-pointing and complete removal and replacement of defective sealant and backer rod), rigorous and thorough cleaning of existing coatings prior to overcoating and using instruments to confirm walls are dry before painting.
The benefits of complete compliance with the specification and manufacturer’s installation procedures are a realization of the expected performance and service lives of the materials being installed. Proper selection and installation of coatings, water repellents and sealants help to mitigate the damage caused by moisture intrusion, and in the case of block walls filled with insulation, to improve energy efficiency by keeping the insulation dry. Aesthetics are also improved by reducing or eliminating blistering and peeling of the coating and the formation of efflorescence and lime runs.
As seen in Durabilty & Design
About the Authors:
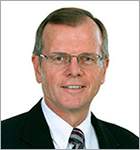
Kenneth A. Trimber is the president of KTA-Tator Inc., Pittsburgh. Trimber has over 40 years of experience in the industrial painting field. He holds a bachelor’s degree from Indiana University of Pennsylvania, is a NACE-Certified Coatings Inspector and an SSPC Protective Coatings Specialist. He is a past president of SSPC and a member of the Standards Review Committee, as well as the chairman of the SSPC’s Commercial Coatings Committee, Surface Preparation Committee and Containment Task Group. He is a past chairman of ASTM D1 on Paints and Related Coatings, Materials, and Applications, and authored “The Industrial Lead Paint Removal Handbook.”
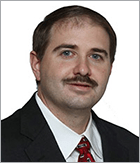
Kevin J. Brown is Technical Director for the Commercial Services Group for KTA-Tator Inc., where he develops and implements maintenance programs for commercial clients with architectural/commercial problems related to paint failures. He holds a CXLT (Certified XL Tribometrist), NACE Level 2 Coating Inspector certification and RRO (Registered Roof Observer) certification. He holds a BS degree and MBA from Gardner-Webb University in Boiling Springs, N.C. He also has attended several seminars at World of Concrete, SSPC and PACE on floor restoration and coating systems. Brown has more than 15 years of experience in the field of retail facility management, overseeing building maintenance and preventative maintenance programs for more than 1,700 stores including store repaints, floor coating replacement and long-range budget planning.
When inspecting my grandma’s house for damage from the strong earthquake the other day, we discovered cracks on the walls that seem to pose danger to the structural integrity of the house. It’s a good thing that you mentioned how we can opt for sealants that are capable of high movement if the cracks are moving since rigid repair materials will only restrict movement and cause more damage to form. I’ll take note of this before hiring a contractor to help with sealing the walls with cracks.