KTA’s Certified Coating Inspector Forum is designed to provide professional development/continuing education on standards, inspection practices, new instruments, and other topics to help keep certified AMPP and FROSIO coating inspectors current. It represents the views of the author and KTA-Tator, Inc. It may or may not represent the views of AMPP: The Association for Materials Protection & Performance, even though SSPC, NACE, and AMPP standards are frequently referenced in the content.
Introduction
Product data sheets, or PDS are essentially an “instruction manual” for the coating, so the only people that need to read them are the ones applying the coating, right? Not really. Coating manufacturer’s PDS are important documents that provide technical information regarding the coating and are often supplemental to a coating specification. Many contract documents and project specifications reference products by generic type (e.g., organic zinc-rich primer, polyamide epoxy mid-coat, polyurethane finish), but may not be accompanied by an Approved Products List (APL)/Qualified Products List (QPL). When the specific brands that will be applied are unknown, it is not possible to include product-specific requirements in the specification. Even when the brands are identified, contractors are typically required to have the PDS on the project site for each material they intend to use. And a coating inspector needs to have them, as well. The contractor and inspector must also be familiar with the material Safety Data Sheets (SDS), but SDS are outside the scope of this article.
Product data sheets are manufacturer- and product-specific, and there is key information that trained and certified inspectors need to know to verify the product is being used as intended. Coating manufacturers also include marketing information and laboratory test data on their PDS, which may be useful for the specifier but serves little purpose for the inspector. This article describes how an inspector can benefit from locating and comprehending specific content on a PDS, and how specifications sometimes invoke requirements listed on the PDS.
Navigating Product Data Sheets
Unlike SDS, there are no requirements for what a manufacturer lists on their data sheets and there is no standard format or sections. And rarely do different manufacturer’s PDS look the same or include the exact same information; however, there are similarities in content. The lack of uniformity makes it challenging for inspectors since they can encounter different manufacturers when moving from project to project. So, the key is to acquire the PDS (typically available on the internet by accessing the coating manufacturer websites) and carefully navigate through the content, highlighting key information before the project begins. (Note: If the date of the latest PDS is more recent than the date of the specification, it may be of value to compare the current and previous PDS.) To illustrate the information available, I’ve selected one manufacturer’s PDS. I’m not intending to show favoritism nor endorse the product. It was selected for illustration purposes only. Each of five pages is shown with key information highlighted. It is interesting to note that a good majority of the sections are not highlighted. It doesn’t mean they aren’t valuable, but they are not necessarily useful to the inspector.
Figure 1 is page 1 of a five-page PDS. Much of the information on Page 1 is of value to the specifier, but there are sections that an inspector needs to reference.

The Product Name and No. must match the product listed on the APL/QPL, if the specification has one. If the specification includes brands, it must match exactly (e.g., Carboguard 890LT is a different product that Carboguard 890).
The Generic Type of coating must match the product type listed in the specification.
Dry Film Thickness (DFT): The specification may invoke the manufacturer’s recommended DFT per coat, but do not assume that to be the case. Look for differences between the specification and the thicknesses in the PDS. If there are differences, point them out.
The Solids Content (Volume) is used to calculate the target wet film thickness and has a direct impact on the coverage rate.
The Theoretical Coverage Rate is based on volume solids content and DFT, not considering losses. Practical coverage rates will be lower. Based on the ft2 to be coated, this helps determine if there is enough coating on-site.
The Volatile Organic Compound (VOC) content (as supplied and thinned – by type and amount of thinner). These values can be compared to local regulations to determine whether the coating can be thinned, and the type of thinner to use.
The Date the PDS was last published.
Figure 2 is page 2 of the five-page PDS. It only has one section highlighted, which pertains to various Substrates and Surface Preparation recommendations for each.
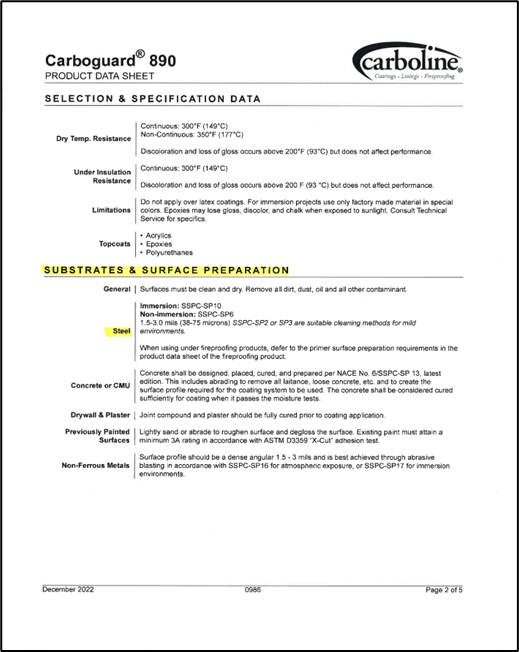
This section provides general and substrate-specific recommendations for surface preparation and addresses steel, concrete, drywall, previously painted surfaces, and nonferrous metals.
Steel substrate is highlighted for the example. Two levels of surface preparation are described based on the service environment. The recommended surface profile range is also indicated. Note that these are general recommendations from the manufacturer; the specification may require a different level of surface cleanliness and a different surface profile depth. For example, although SSPC-SP6 is listed as being suitable for non-immersion service, the specification may require SSPC-SP10, which will prevail.
Figure 3 is page 3 of the five-page PDS. Again, only one section is highlighted, which pertains to mixing and thinning.
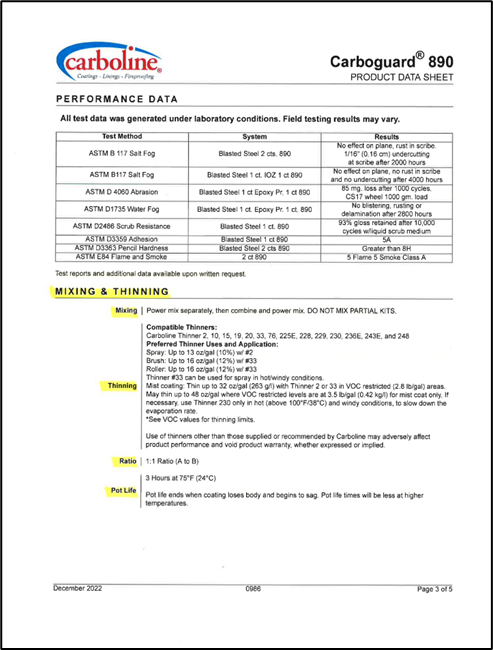
Mixing invokes power mixing (not hand mixing) and prohibits mixing of partial kits.
Thinning. Compatible thinners are listed, as are specific types and amounts based on the application method. Alternative thinners for mist coating over zinc-rich primers and hot/windy conditions are described. Note the caution regarding thinning and VOC. That is, thinning to the maximum listed here may cause the VOC level to be unacceptable as shown on Page 1.
The Ratio of Part A to Part B is listed to help ensure the correct number and container size of the components are mixed. For example, there may be one-gallon and five-gallon units on site. Since the ratio is 1:1, this should prevent five gallons of Part A getting mixed with one gallon of Part B. It is not for mixing partial kits, which is prohibited above.
The Pot Life of the mixed material is based on the temperature of the material, which is influenced by the surrounding air temperature.
Note: If the coating had an induction or sweat-in requirement, it would typically be listed in this section. This product does not have an induction time. If it did, the pot life begins at the time the components are mixed together.
Figure 4 is page 4 of the five-page PDS. It provides Application Equipment Guidelines, Application Conditions, and a Curing Schedule.
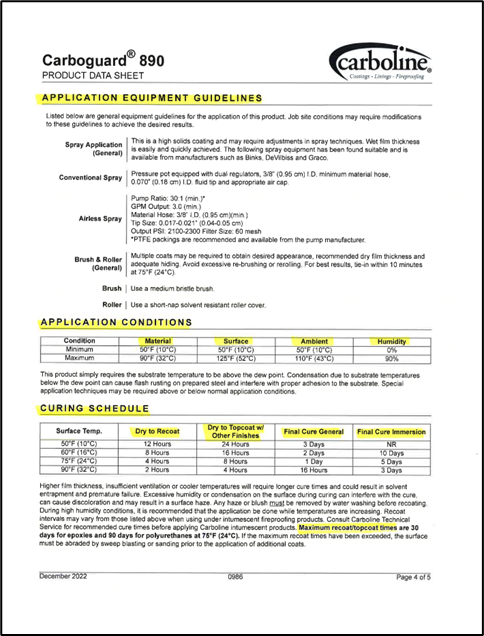
Application Equipment Guidelines are just that… guidelines for conventional (air) and airless spray, brush, and roller. The contractor will select tip sizes and pressures based on actual conditions, viscosity of the materials, etc., unless the specification requires that the contractor conform to the manufacturer’s guidelines for equipment.
Application Conditions is a critical section, since many specifications will invoke the manufacturer’s temperature ranges for the paint, the air, the surface, and the amount of moisture in the air. Note that the manufacturer may allow up to 90% relative humidity (RH), but the specification may invoke a maximum of 85% RH. The specification is the governing document. The requirement that the surface temperature be higher than the dew point temperature by at least 5°F is also typically included in this section.
The Drying and Curing Schedule on the PDS may also be invoked by the specification. In this case the dry/cure times are based on the surface temperature. Dry to recoat with itself and with another product are listed, along with full cure for both atmospheric and immersion service. The maximum recoat times are also indicated together with the necessary steps to follow if the times are exceeded.
Figure 5 is the final page of the five-page PDS. It provides Packaging, Handling, and Storage information. This section typically contains:
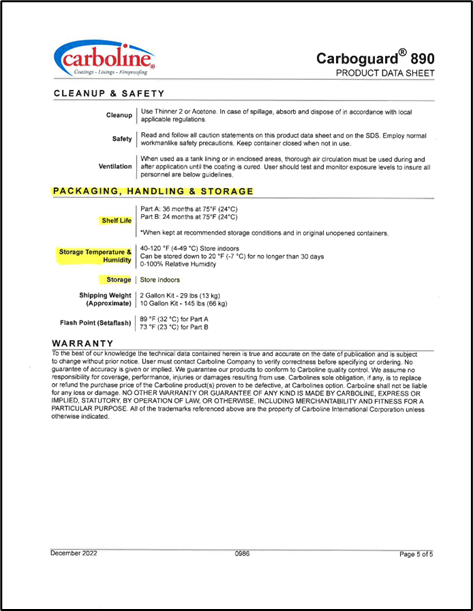
Shelf Life is based on a specific storage temperature for each component. Shelf life begins at the manufacturing date and is based on unopened cans stored according to the requirements in the PDS.
Storage Conditions (temperature and humidity ranges) for storing the material. Note that storage outside of these conditions can affect the shelf life or usability of the material.
Storage Location. Note that “indoors” generally means protected from the direct impact of the weather.

Comparing Specification Requirements to PDS Recommendations
After navigating through the product data sheets for each coating material to be used on the project, the next step is to carefully read the project specification to determine whether there are project-specific requirements that would supersede the manufacturer’s recommendations, or if there are discrepancies or differences between the manufacturer and the owner requirements. If these exist, an inspector should flag them so they can be resolved before the project begins. Developing an Inspection Test Plan (ITS) is another good way to capture all the inspection checkpoints and corresponding acceptance criteria, and determine whether the criteria conflict with the PDS, and vice-versa. The process of creating an ITS will be the subject of a future column.
Summary
Product data sheets are a valuable tool for coating applicators as well as trained and certified coating inspectors. They are essentially an instruction manual for using the product. Unfortunately, many of us don’t read the instructions until it is too late, or assume it is the same material we’ve used for years, or that the “epoxy” of one manufacturer is the same as the epoxy from another. Reading and comprehending PDS as well as the governing coating specification on every project can help avoid application issues and catastrophic coating failure.
Thank You Mr. Corbett. Once again, your insights were quite informative. As much as I have used PDS’s over the years, your article bears several pearls of wisdom that I had not though about previously.
God Bless
Thank you this is a handy reminder of what to look for.
Thanks for reading, John!