KTA’s Certified Coating Inspector Forum is designed to provide professional development/continuing education on standards, inspection practices, new instruments, and other topics to help keep certified AMPP and FROSIO coating inspectors current. It represents the views of the author and KTA-Tator, Inc. It may or may not represent the views of AMPP: The Association for Materials Protection & Performance, even though SSPC, NACE, and AMPP standards are frequently referenced in the content.
Introduction
I recently learned of a catastrophic coating failure (in litigation) that occurred at an educational institution. During discovery it was learned that no quality control documentation was available from the contractor’s inspector or superintendent. When asked, the contractor responded that the project specification did not require documentation, so while compliance with the project specification was claimed, nothing was recorded. The lack of documentation on that project could easily cost the contractor hundreds of thousands of dollars in rework (depending on the outcome of the litigation), since widespread disbonding (between coats) occurred and compliance with the manufacturer’s maximum recoat time was in question. Let’s talk about the importance of documentation, independent of contractual requirements.
The Insurance Analogy
Most of us carry insurance on our automobiles, homes, boats, motorcycles, jewelry, artwork, and other property. We do so because there is a chance we will need coverage in the event of a loss. But we also recognize that we may never really need that insurance, yet we continue to pay annual premiums. That’s how I think about documentation on a coating inspection project – insurance that we may never use, but when we need it, we’re glad we have it! Consider the sheer volume of documentation that fills file cabinets or uses Cloud storage that we don’t need after the fact. It isn’t needed because the coating project was a success. But when the project is in-progress, we don’t know whether it will be a success or if there will be issues once the project is completed. This is the value of documentation. It is our “time machine.” It provides us with a written “picture” of what was done, so that we can compare it to what was supposed to be done (the specification) as part of problem resolution.
I get it. No one likes paperwork and few inspectors enjoy the documentation side of their job. But it is a key responsibility since as commonly argued, “if it wasn’t written down it didn’t happen,” even if it did. While the contractor in the case cited above alleges he was not contractually required to document the results of the quality inspections, the effort required to record the measurements and document actual recoat intervals seems minuscule compared to the cost of potential rework. Documentation in this case could have served as the contractor’s proof that he complied with the coating manufacturer’s recoat interval.
There is no standard documentation form, nor is there a standard set of information that must always be documented. For example, holiday detection will almost always be required on a tank lining project, but typically won’t be invoked on a bridge coating project. Creating inspection documentation forms can be challenging, as they need to strike a balance between logical organization and thoroughness. Here are a dozen tips for creating and completing documentation forms.
Creating/Designing Documentation Forms
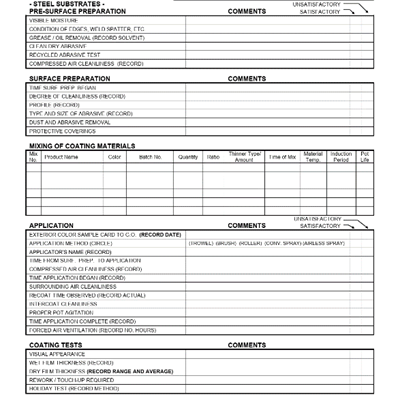
- You’re not the first one to create a coating inspection form. Look at others and take the best of the best from them to create your form. But abide by any copyright restrictions.
- Consider the inspection checkpoints that are common to many of the coating projects you are involved with and make sure they are addressed on your form.
- Consider what you will be documenting and how much space is required to document the information legibly. That is, are you entering values, a few words, or a narrative?
- Consider the order of the information. For example, in many cases ambient conditions are monitored first, so fields/cells for recording ambient conditions and surface temperature should be placed on the form before checkpoints like the quality of surface preparation, coating mixing, and dry film thickness.
- Include diagrams or drawings of the structure that show the progress of the work each day (i.e., the locations of surface preparation, priming, top coating, etc. completed that day). Representative digital images of the quality of the work also help.
- Without having to dig, the reader should be able to easily see whether each phase of the work done that day complies with the specification requirements and if rework was required to bring it into compliance.
- Be careful using abbreviations unless they are obvious. Consider that the reports will often be read by people who may not be conversant in the language of our industry. While most people will recognize RH, they may not recognize fc (foot candles for illumination) or even WFT or DFT for wet and dry film thickness. If space isn’t available for the names, consider including an abbreviations key.
Completing Documentation Forms
- Put an entry in every field. Leaving a field blank infers you forgot to enter information. If it is not applicable, document NA or some other designation. If it wasn’t witnessed, document NW (Not Witnessed) and footnote what “NW” means or add it to the abbreviations key.
- Do not use White-out liquid or tape. Strike a single line and initial it if you need to change an entry. And always use ink.
- If you are completing forms created by others, if you don’t understand what you are supposed to document in each field, get clarification. There is no shame in telling someone you don’t understand something on their form.
- Make sure to sign and date the documentation forms. Co-signing a form completed by others makes you equally responsible for the content, so if you do, make sure the information they recorded is accurate.
- Include units of measurement. For example, temperatures should be accompanied by an F or C, surface profile and coating thickness values should be followed by mils or microns (µm), abrasive water-soluble contaminant levels followed by mS/cm or µS/cm, and surface salt concentrations followed by mg/m2 or µg/cm2 along with the salt anion type, such as chloride, sulfate, nitrate, etc.
Writing a Narrative
Written communication is an art and the ability to communicate using the written word should be a requirement of any competent inspector. Some will argue that written communication has become a lost art and that even the most educated individuals cannot convey their thoughts in a clear, concise, cohesive manner. In fact, some now rely on artificial intelligence to write for them. Despite that potential reality, written documentation is of critical importance on a coatings project and is a key element in resolving disputes or diagnosing premature failures. Inspection reports contain data acquired using instruments, but a properly constructed narrative gives context to the data and provides the owner and the contractor’s management with a picture of how the project is progressing. In fact, as the use of digital documentation increases, the importance of narrative is only heightened.
How Often Should Daily Inspection Reports be Prepared?
I like this question because despite the obvious answer, procrastinators will wait until the end of the week before preparing them. Any details that are not contained in field logs will certainly be forgotten by putting off this task. Daily reports prepared by trained/certified inspectors should be completed…daily. Unless a different schedule is agreed upon, they should also be submitted the following day to the appropriate individuals. Learning a week later that there are issues on a project isn’t good for anyone.
Digital Documentation
Many inspectors have adopted the use of electronic or digital documentation, where data stored in a gauge memory is uploaded automatically to a digital platform such as TruQC or the gauge manufacturer’s proprietary software. Some public agencies are even requiring the use of electronic documentation so that records are received the same day, are more easily stored, can be accessed by multiple parties, and are searchable in the event of issues in the future, not to mention the reduction in paper use and storage. Whether documentation is handwritten or digital, as a trained/certified inspector you are still responsible for the content, so make sure the data transfers correctly and has populated the correct fields. Also, these platforms don’t know good data from bad data, so be sure to review the data once it is uploaded and you’ll still need to determine whether the inspection results conform to the specification requirements or manufacturer’s product data sheets. And don’t forget that writing a narrative to accompany the data is still important.

Summary
Regardless of which party you are working for, documentation of inspection data is a critical role for a trained/certified inspector, albeit oftentimes one of the more dreaded tasks. It is just as important as your hands-on inspections and acquiring the data. Poor documentation (or lack of it altogether) can make problem resolution very difficult and can leave any of the parties (contractor, owner, or material supplier) sharing in the cost of rework they may not be responsible for. Don’t get hung up on apparent contractual loopholes that don’t explicitly require it. Document the results of your inspections daily, and make sure your reports are accurate, legible, and complete. Your reports are a direct reflection of you and your level of professionalism.
very informative and useful examples to pass along out in the field
Thanks, Charles. We’re glad you found it helpful!
Daily reporting should also be done on a construction site, and it is much more productive to do it with software so as not to get bogged down in a pile of paperwork
Daily reporting should also be done on a construction site, and it is much more productive to do it with software so as not to get bogged down in a pile of paperwork
Daily reporting should also be done on a construction site, and it is much more productive to do it with software so as not to get bogged down in a pile of paperwork