Concrete is the most commonly and widely used construction material for commercial building floors. While the decision to specify concrete is an easy one, the selection of the floor finish or coverings to be installed on the floor can be quite complicated. There are endless floor finishing options for new construction projects. Owners and designers work together to come up with a floor finish that is suitable for the service environment, within budget, meets maintenance expectations and accurately illustrates the company’s brand image. The concrete is then designed to accommodate the desired finish.
But when it comes to existing concrete floors, the finishing decisions become even more complicated. When it is time to restore, reuse or remodel an existing floor, the condition of the concrete becomes a major factor in the selection of the finish flooring type. Depending on the concrete condition, the owner may decide to coat it, cover it or polish it, or, in a worst case, completely remove and replace it. This article discusses floor finish options for concrete, typical problems that may be encountered in existing concrete and methods that are used to assess the condition of the concrete.
The primary floor finish options for concrete in commercial buildings include coatings, coverings and concrete polishing. A variety of aesthetic options are included within these three categories, from a basic, utilitarian look to a highly decorative one. It is important to consider the advantages, disadvantages and costs when considering a concrete floor finish. Below are average costs and a comparison of the advantages and disadvantages of each flooring type.
CONCRETE FLOOR COATINGS
Concrete coating choices range from do-it-yourself materials to specialized industrial materials. Coatings are sometimes referred to as seamless floors, fluid-applied flooring and resinous flooring. Numerous types and formulations of coatings allow for highly customizable options that can be adapted to most any type of commercial application. General advantages and disadvantages of concrete floor coatings are listed below in Table 1.
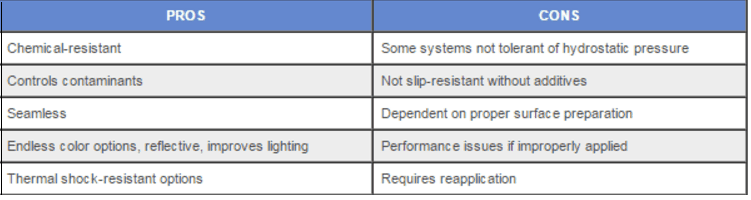
Hundreds of different types of concrete coatings and coating formulations exist in the industry. Concrete coating type varies by thickness, application methods, resin type, appearance and texture. Common types of concrete coating systems include:
- Thin-film coatings (sealers, stains, dyes, single-component acrylics, epoxies)
- Thick-film coatings (hi-build epoxies, polyurethane, polyurea, hybrids)
- Slurry systems (cementitious and resinous)
- Broadcast systems (quartz aggregate, color chip, metallic)
- Mortar systems (toppings, overlays)
Many factors go into selecting the most effective coating type. Performance characteristics may include bond strength; abrasion resistance; impact resistance; compressive strength; tensile strength; flexural strength; chemical resistance; non-skid properties; reflectivity; weathering; cleanability; secondary containment requirements; USDA/FDA compliance; microbial control; appearance; and maintenance properties.
The appropriate resin type must also be determined and may include acrylic, epoxy, polyurethane, polyester and vinyl ester. Installed prices range widely. For example, installed costs for thin-film systems range from $1.00 – $3.50 per square foot. Thick-film systems range from $3.50 – $7.00 per square foot. Mortar systems can cost up to $20.00 per square foot. Average service life is five to 10 years. Coating consultants are sometimes used to determine which coating type best fits the owner’s project requirements at the lowest life-cycle cost.
FLOOR COVERINGS
Floor coverings consist of a wide range of options, including carpet, hardwood/laminate, vinyl (VCT, LVT, Sheet), natural stone, terrazzo, ceramic tile and porcelain tile. In some cases the floor coverings are attached with adhesives, grout or they snap together to form a “floating” floor. Installed prices, average service life and the pros and cons of each type of floor covering are shown below in Table 2.
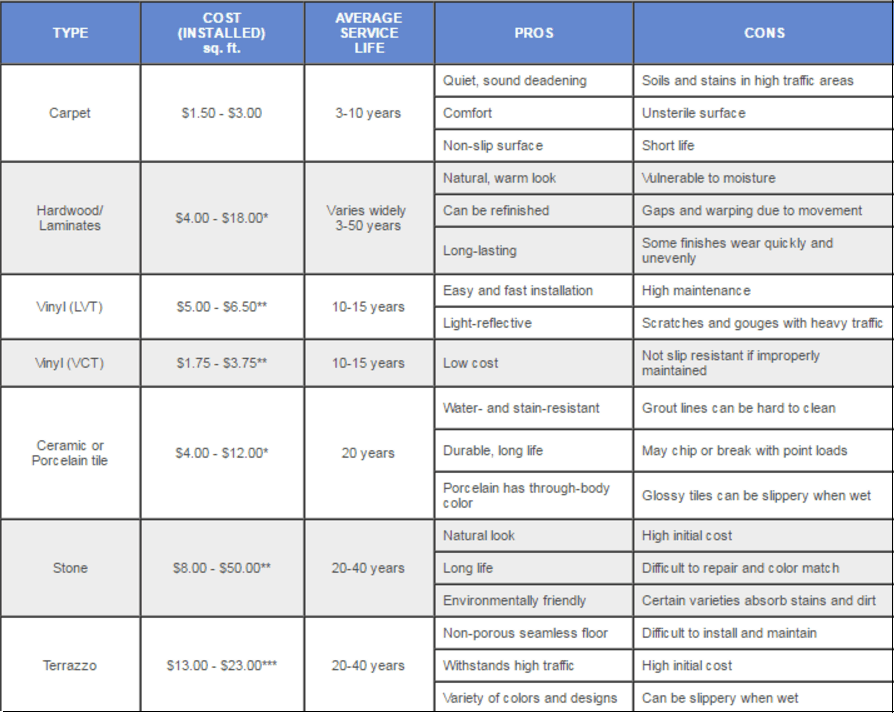
POLISHED CONCRETE
Concrete polishing is unlike coatings and coverings in that the finish is produced onsite. Polished concrete does not come in a can, roll or box like other products that are produced in plants with strict quality control standards. Concrete polishing is both a mechanical and chemical process. An initial assessment of both new and existing floors and technical specifications are necessary for polished concrete to be a successful floor finish. It requires highly trained craft workers who also have artistic abilities.
Concrete polishing is defined by the amount of aggregate exposure and level of sheen. The Concrete Polishing Association of America (CPAA) defines the aggregate exposure by Class A, B, C and D as shown in Figure 1.

Finished gloss is also defined in four levels by CPAA. The higher levels of gloss or reflective sheen are achieved by successive floor grinding steps using incrementally smaller grit diamonds in polishing pads attached to floor polishing equipment. Polish is continued at a 90 degree angle from the previous step until the desired sheen is achieved.
- Level 1 – Flat (Ground) Diffused reflection – < 100 Grit
- Level 2 – Satin (Honed) Matte appearance – 100-400 Grit
- Level 3 – Semi-Polished – High Shine – 800+ Grit
- Level 4 – Highly-Polished – Glossy, Mirror-like Finish – 1500-3000 Grit
Finished color can also be added as a dye during the polishing process, creating a highly decorative and artistic floor. Average costs for polished concrete with no aggregate exposure ranges from $1.50 – $2.50 per square foot for five steps and $3.50 – $6.00 per square foot for eight steps. Exposed aggregate adds an additional $1.00 – $3.00 per square foot. Dyed floor (without patterns) adds an additional $1.00 per square foot.
Since polished concrete is a relatively new process with introduction in the U.S. around 2000, the life expectancy is not well defined. Polished concrete does require general maintenance on a daily basis along with periodic burnishing on a quarterly basis to sustain high shine. Table 3 lists the pros and cons of polished concrete floors.
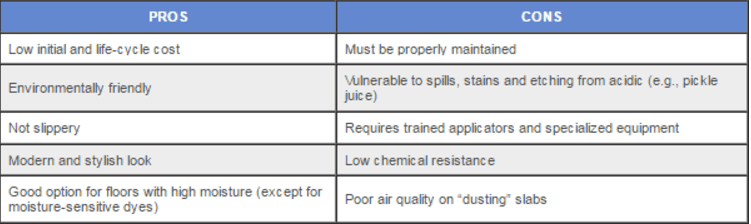
CONCRETE FLOOR DEFECTS AND DETERIORATION
When dealing with existing concrete, a floor condition survey is necessary to identify and document concrete defects and deterioration that could impact the floor finish. As owner’s requirements change, buildings are reused for different purposes and existing floor finishes wear out. The finished flooring type may be different from the original finish. Depending on the floor condition, the owner may decide to coat it, cover it or polish the existing concrete. Some typical concrete problems that may be encountered in an existing floor when selecting the floor finish type include:
- Excessive deterioration;
- Improper concrete design;
- Placement- and curing-related defects;
- Excessive moisture; and
- Aesthetic concerns.
A brief discussion of each follows.
Excessive deterioration: Service loads, weathering and exposure to aggressive chemicals such as deicing salts will eventually cause deterioration and corrosion of the concrete surface. Figure 2 shows stamped concrete that has significant erosion of the surface due to heavy traffic loads and exposure to deicing salts. In the case of reuse, factories may now be used as retail spaces exposing concrete that has had generations of alternate uses as shown in Figure 3. In either case, removal and replacement of the concrete may not be feasible due to disruption or scheduling limitations. In these cases a concrete coating or epoxy mortar overlay is a viable option.
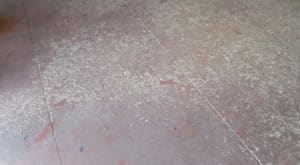
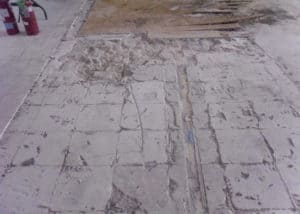
Improper concrete design: Improper concrete mix designs can result in concrete deterioration and may impact the floor finish type. An assessment of the engineering data (if available) is needed during the assessment phase. Further, in the case of a concrete floor reuse, the original mix design may limit the choices of floor finishes that can be used. For example, certain floor finishes may require specific requirements for shrinkage, durability, permeability, workability, finishability and strength. A proper concrete mix along with floor flatness and levelness tolerances are particularly important for polished concrete floors. Knowing the original design will aid in making knowledgeable decisions on the floor finish type.
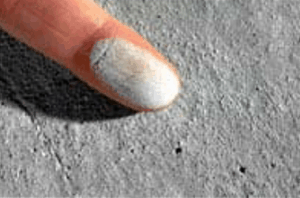
Placement- and curing-related defects: Defects such as excessive carbonation, dusting and concrete curling can result from improper concrete placement and curing techniques. These types of defects can create unwanted problems on the concrete surface. Carbonation occurs naturally in concrete but becomes a problem when it is excessive. It is caused by the absorption of carbon dioxide into the slab, which lowers the pH leading to a soft concrete surface. Figure 4 shows a concrete floor with excessive carbonation, which leads to dusting of the concrete surface. The authors have experienced projects where carbon dioxide from the concrete finishing equipment and concrete delivery trucks have created an environment rich in CO2 leading to excessive carbonation. Curing-related defects create unwanted problems such as slab curling (Figure 5). Excessive curling leads to faulting at control joints, which creates challenges with many types of floor coverings.
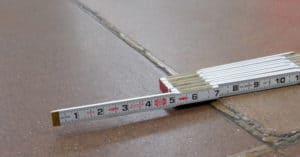
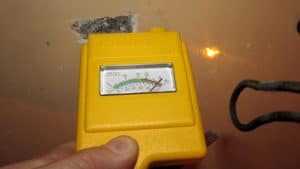
Excessive moisture: The absence of a functional vapor retarder and excess moisture vapor emissions lead to many types of floor finish failures. Some coatings and floor coverings are vulnerable to excessive moisture. Moisture can move through the slab by capillary action, osmotic movement and hydrostatic pressures, which can lead to coating or floor covering delamination (Figure 6). Some floor covering adhesives are highly susceptible to excessive moisture and dissolve in its presence (Figure 7). In the case of floor polishing, excessive moisture causes color loss or color shift with moisture-sensitive dyes. In many cases, excessive moisture problems can be overcome with proper assessment, planning and design. There are coating systems that will adequately bond to concrete having a relative humidity upwards of 99 percent. Floor coverings can adequately adhere to the concrete slab with the addition of a moisture-mitigation membrane. Membranes can be liquid- (Figure 8) or sheet-applied and will also perform well on slabs with 99 percent relative humidity. Many floor covering manufacturers offer adhesives that will perform adequately on slabs with elevated moisture. In any case, an assessment of moisture is necessary before selecting the specific system or floor finish.
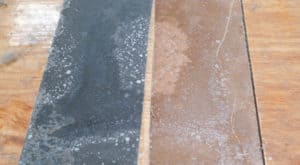
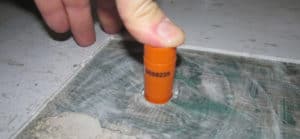
Aesthetic concerns: Certain aesthetic issues may cause owners to reconsider the floor finish type. This can be especially relevant when changing from one flooring type to another or reuse of an existing floor. One problem that often arises when owners are considering changing from a floor covering to polished concrete is “shadowing” or “ghosting” patterns from pre-existing floor coverings. Sometimes dark lines or patterns will appear on the surface that correspond to the previous floor covering layout (Figure 9). This defect typically does not affect the integrity of the concrete, but the appearance may become too much of an eyesore. Other problems that may be encountered include delamination of the concrete surface from removal of floor covering adhesives (Figure 10) or loose layers of pre-existing patch (Figure 11). These problems are typically not seen until floor coverings are removed, and they may indicate that the floor is not be suitable for polishing. (These conditions often require the use of an overlay or floor topping.)
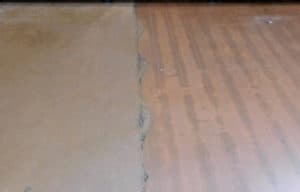
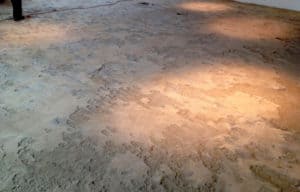
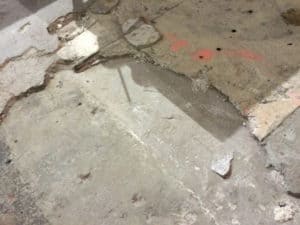
ASSESSING THE CONDITION OF CONCRETE FLOORS
Prior to restoring, changing or installing a new floor finish, an assessment of the concrete is necessary. Regardless of age, concrete can become damaged by the effects of weathering, chemicals, moisture and excessive loading. Floor finish installations may require the use of specialized professionals to assess the concrete condition, identify the appropriate repair methods and materials and oversee the installation. A condition assessment typically involves a thorough visual assessment along with physical testing. There are some useful industry guides to assist in concrete assessments available for download through ACI (American Concrete Institute) and ICRI (International Concrete Repair Institute). In addition, the authors have found the following physical tests useful in the assessment of concrete floors in preparation for floor finishes.
Moisture testing: Moisture testing helps to reduce the risk of floor coating failures and delamination related to excessive moisture in concrete. Moisture testing is also necessary when using certain concrete dyes associated with concrete polishing. Moisture testing may consist of relative humidity testing using moisture meters, moisture vapor emission rate (MVER, ASTM F1869), and percent of relative humidity of the concrete floor (ASTM F 2170). Relative humidity testing equipment is shown in Figures 8 and 12.
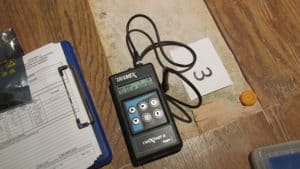
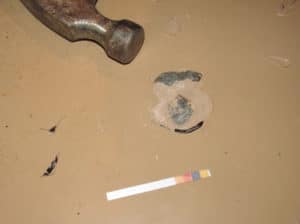
Acidity or alkalinity testing: Expressed as pH, the degree of acidity or alkalinity of concrete is measured on a scale from 0 (acidic) to 14 (alkaline). It is necessary to know the pH of concrete for most floor coating and floor covering adhesives. Figure 13 shows the use of a pH strip to determine the pH of blister liquid underneath an epoxy floor coating.
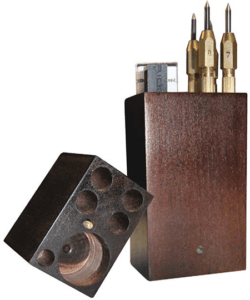
Floor polish assessment: An assessment of the concrete is necessary to determine areas of delamination, hardness of the surface and the depth of carbonation on floor polish projects. Some slabs may have areas of delamination. If delamination is suspected, a “chain test” is useful in determining areas of delamination by sound. Standard chains with a chain-link length of around 2 inches are typically used. Hardness can be measured in the field using a Mohs Hardness test kit (Figure 14). The Mohs hardness test is a scratch test to determine the approximate concrete hardness on a scale from 1 (soft) to 10 (hard). Hardness helps to identify floor dusting and carbonation concerns and allows the polishing contractor to plan for proper tooling selection to maximize production time on the job. If excessive carbonation is suspected, a phenolphthalein pH indicator solution can be used to determine the depth of carbonation.
Petrographic examination: In some cases petrography of a concrete core is necessary to analyze the condition of the concrete, causes of distress in concrete and whether the deterioration will continue. ASTM C856 Standard Practice for Petrographic Examination of Hardened Concrete is a common standard used in the petrographic analysis of concrete. For floor finishes, it is often useful to analyze the upper segment of the concrete core since this is the primary wearing surface or surface in contact with coatings and coverings. Figure 15 shows an example of a concrete core that had concerns with a soft wearing surface and excess carbonation. Results from petrographic analysis can be used to determine the appropriate repair methods, materials and application methods suitable for the condition.
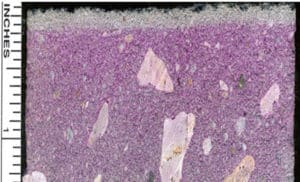
CONCLUSION
Concrete floor finishes provide a means for commercial building owners to convey their brand image to customers and associates. Unique images can be created using coatings, coverings and concrete polishing to reinforce their company’s message. The floor finish cost, advantages and disadvantages of each type and existing concrete condition must be considered before deciding which floor finish is most suitable. Pre-assessments of existing floors are necessary to avoid detrimental uncertainties. Proper planning, assessment, design and execution can ensure a successful floor finish project. D+D
ACKNOWLEDGEMENT
Average cost data for floor systems furnished by SASE Company unless noted otherwise.
ABOUT THE AUTHORS
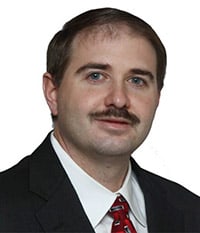
Kevin J. Brown is technical director for the Commercial Services Group for KTA-Tator Inc., where he develops and implements maintenance programs for commercial clients with architectural and commercial problems related to paint failures. He holds a CXLT (Certified XL Tribometrist), NACE Level 2 coating inspector certification and RRO (Registered Roof Observer) certification. Brown has a bachelor’s degree and a master’s degree in business administration from Gardner-Webb University. He also has attended several seminars at World of Concrete, SSPC, and PACE on floor restoration and coating systems. He has more than 15 years of experience in the field of retail facility management, overseeing building maintenance and preventative maintenance programs for more than 1,700 stores including store repaints, floor coating replacement and long-range budget planning.
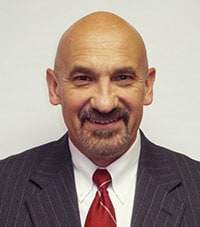
Terry S. Carroll, P.E., is the Commercial Services Group manager for KTA-Tator Inc., where he manages the efforts of the group in performing building envelope diagnostics and providing recommendations and specifications for resolution of moisture intrusion problems. His career covers 40 years of engineering design, construction, and facilities management of commercial and industrial facilities in manufacturing, power, and retail industries. Carroll is a registered Professional Engineer and a licensed general contractor. He holds a bachelor’s degree in Civil Engineering from NC State University and a master’s degree in business administration from Winthrop University. He is an active member of the National Society of Professional Engineers, serving as North Carolina state president and in many other roles at the state level. Carroll has served as a lecturer at various engineering and trade association conferences.
It’s so enlightening when you said that concrete polishing is not very like coverings and coatings in that the finish is produced on-site. We didn’t know until now that polished concrete doesn’t come in a box, roll, or can like other products that are made in plants with rigorous quality control products. I can’t believe that I just learned it! Thanks for your amazing blog.
We’re glad that our article was helpful!