Introduction – If Fiber Reinforced Plastic (FRP), also known as glass reinforced plastic (GRP), is specified to be coated, the appropriate coatings must be selected and the surface properly prepared, to assure long-term performance.
Why Coat Fiberglass?
FRP is frequently used in highly corrosive environments as it is inherently corrosion resistant and does not rust like steel. So why cover it with a protective coating? One of the primary reasons is to provide protection from ultraviolet (UV) light. Exposure to UV degrades resin at the molecular level by breaking the carbon chains of the polymer. An analogy for the degradation is the chalking of epoxy coatings when exposed to sunlight. In the case of FRP, as the breakdown of the outer surface continues over time, glass fibers are exposed and the mechanical properties of the laminate are reduced. If the surface is already degraded from UV, coatings can be applied to stop further deterioration.
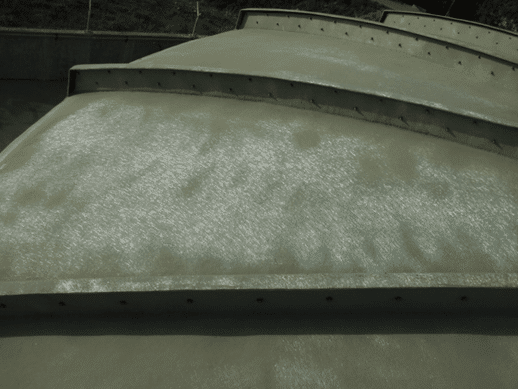
FRP is also coated to match the color coding at a facility. Many large industrial facilities have specific color codes for equipment and piping, such as red for fire protection systems, blue for cooling water, and yellow for natural gas. FRP can be easily coated to meet the facility’s color scheme.
FRP is also coated for aesthetics. Over time the FRP will fade and the gloss will be reduced. Coatings will provide a fresh appearance to the item, including high gloss, if desired.
Preparing the FRP for Coatings
Similar to the application of paints to other substrates such as steel, non-ferrous metals, concrete, and wood, the surface must be clean, dry, and etched or roughed for the protective coating to properly adhere.
Grease, Oil, and Dirt – Surfaces must be dry and free of dust, dirt, debris, grease, oil, and other surface contamination. Cleaning can be accomplished by pressure washing supplemented with detergent cleaning as necessary. Low pressure, defined by the Society of Protective Coatings (SSPC) as pressures up to 5,000 psi, is all that is needed. A rotating or spinner tip will also help to improve the cleaning. If pressure washing is not practical, cleaning can be achieved by scrubbing with detergent and rinsing with clean water.
Surface Roughening – FRP typically has a very smooth, glossy finish which is not conducive for achieving good coating adhesion. At a minimum, the surface needs to be hand or power sanded to remove the gloss and roughen the surface. Dual action sanders (DA sanders) and grinders are frequently used, but because FRP is much softer than steel, care must be taken during sanding to only roughen, rather than remove, the FRP. Grinders are also used for roughening, again with extreme care. For large projects, abrasive blast cleaning is used, but a less aggressive blast media than is used for steel is recommended. Abrasives include plastic, walnut shells, and corn cob. Stand-off distance and dwell times must also be adjusted to minimize the removal of FRP. Specialized sponge material impregnated with abrasives is a novel alternative that works well and helps to minimize dust generation, but specialized blast cleaning equipment is required.
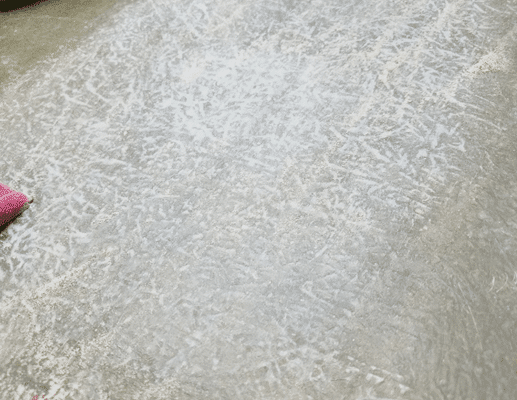
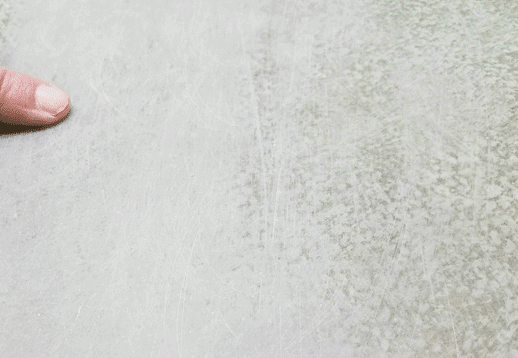
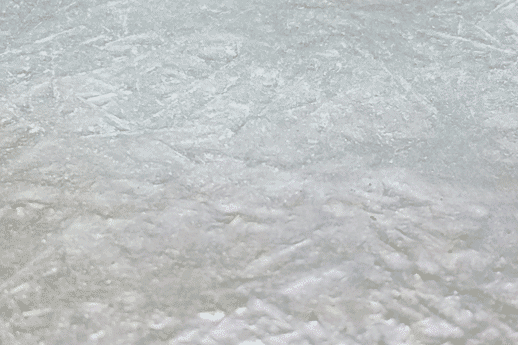
Because mechanically abrading of FRP generates a significant amount of dust, upon completion of the preparation, any free-standing dust must be removed. Vacuuming, clean air blow down, or wiping the surface with a damp cloth are effective in removing the dust.
Upon completion of cleaning, the surfaces should be examined for protruding glass fibers which must be removed. If glass fibers protrude through the coating film, pinholes can occur at that location. Any specific preparation requirements of the coating manufacturer should also be met.
Coating Materials
A wide variety of generic coating types can be applied to FRP. The specific system is selected based the expected environmental exposure, such as chemical or UV. Following are several coating types that are frequently applied to FRP:
- Gel coats – Gel coats are typically applied during the manufacturing process. It is a finish coat that uses the same base resin that was used in the fabrication of the product with additional UV stabilizers and pigments added. There is no reinforcement material in this layer, and it does not provide structural properties to the fabricated item. Gel coats can be applied to the surface of the mold prior to injecting the FRP material or applied by spray, brush, or roller to the surface of the completed item. Examples include exterior FRP panels and pleasure watercraft where a UV stable gel coat is used.
- Several water-based acrylic coating systems are suitable for application to FRP. Acrylic coatings are single component, easy to apply, and do not require the addition of solvents for application other than water. They contain little to no volatile organic compound (VOC’s) which makes them ideal for use in regions with stringent restrictions on VOC emissions. UV resistance, color retention, and resistance to chalking are typically good, but can vary between products. For exposure to more severe service environments (chemical/marine), a more robust coating system would be recommended. The use of a bonding primer may be needed depending on the individual coating. The coating manufacturer and product data sheets should be consulted for specific product requirements.
- Epoxy systems generally provide excellent chemical resistance and are often selected when chemical exposures are anticipated. Epoxies are two component systems that require mixing prior to application. Although water-based epoxy can be used, solvent-based is more common. Epoxies in general have poor UV resistance and will chalk and fade with exposure to sunlight. If sunlight exposure is anticipated, a finish coat such as urethane is applied to the epoxy.
- Urethane coatings consist of two components and typically have good chemical resistance. Unlike epoxies, urethanes have excellent resistance to UV light and are suitable for outdoor service. They can be applied as a finish coat to epoxy or applied directly to the FRP.
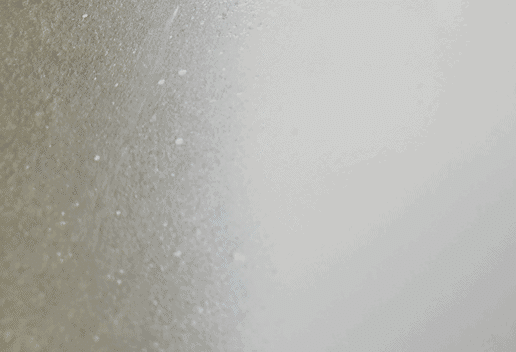
Conclusion – FRP is coated to improve UV and chemical resistance, for color coding of piping and vessels, or for aesthetics. Traditional industrial coatings such as acrylic, epoxy, and urethane can be applied to FRP. Prior to applying a coating, the surface must be clean, dry, and roughened to assure good adhesion.
Other topics in this FRP series:
Topic 1 – Inspection of the FRP fabrication process
Topic 2 – Surface Preparation and Coatings for FRP
Topic 3 – Inspection of FRP cleaning and painting
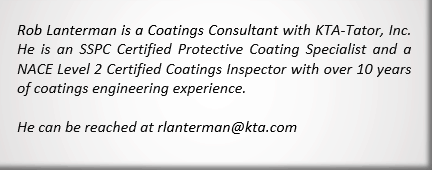
Need Frp coating contactor in concrete surface
Hi Akbar, please contact us directly by calling 1-800-245-6379 or emailing info@kta.com