KTA’s Certified Coating Inspector Forum: Volume 2, Issue No. 8 – August 2023
William Corbett, COO
AMPP Senior Certified Coating Inspector & Certified Protective Coating Specialist
KTA’s Certified Coating Inspector Forum is designed to provide professional development/continuing education on standards, inspection practices, new instruments, and other topics to help keep certified AMPP and FROSIO coating inspectors current. It represents the views of the author and KTA-Tator, Inc. It may or may not represent the views of AMPP: The Association for Materials Protection & Performance, even though SSPC, NACE, and AMPP standards are frequently referenced in the content.
Introduction
Arguably one of the most difficult in-process inspections is determining whether the specified degree of surface cleanliness has been achieved before the coating is applied. Inspection of surface cleanliness is done visually with unaided eyesight or corrected vision, and preferably under adequate lighting. But even under the best conditions, it can be a very subjective inspection. This edition of the Certified Coating Inspector Forum describes how the SSPC Visual Guides and be used to establish a project-specific cleanliness standard, and how creating this standard can help minimize subjectivity and ensuing disagreements on a project. The guide for abrasive blast cleaning is used as the example.
History of Pictorial Guides for Abrasive Blast Cleaning
The industry has long recognized the value of a visual guide to assist with surface cleanliness inspection. A pictorial guide was first developed and published by the Swedish Standards Institute (SSI) in 1959. It contained four initial conditions of steel prepared to two levels of hand and power tool cleaning (St2/St3), and three levels of dry abrasive blast cleaning (Sa1, Sa2, and Sa3). It was written in multiple languages and was adopted by SSPC in 1963 as SSPC-VIS 1-63T to depict the appearance of Brush-off Blast Cleaning, Commercial Blast Cleaning, and White Metal Blast Cleaning. In 1963, the definition of Near-White Metal Blast Cleaning was written, but photos were not included in the Swedish Standards until 1967 (Sa 2 ½). The revised Swedish Standards was subsequently adopted by SSPC as SSPC-VIS 1-67T.
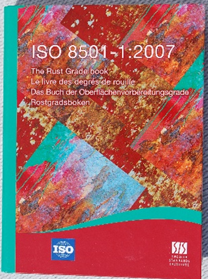
In the early 1980’s, users expressed concern that some of the photographs didn’t agree with SSPC’s written definitions, primarily those of Sa2, which was said to be equivalent to Commercial Blast. In particular, photograph BSa2, showed islands of mill scale on the surface, contrary to the written SSPC definition that allowed only staining to remain, rather than actual remnants of mill scale. SSPC was unsuccessful in convincing the SSI that the photo should be changed, and in 1985, began developing its own photographs, which were published in 1989 as SSPC-Vis 1-89, Guide and Reference Photographs for Steel Surfaces Prepared by Dry Abrasive Blast Cleaning. Around the same time, the Swedish Standards became an ISO standard – ISO 8501-1/SIS05 59 00 (1988) and is still in use (primarily outside of the United States) today.
Use of SSPC Visual Guides
The current version of SSPC-VIS 1 (2002) depicts seven initial conditions of steel before any abrasive blast cleaning is performed. They include four conditions of uncoated steel:
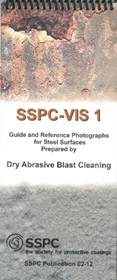
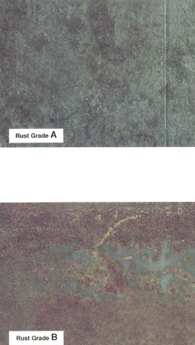
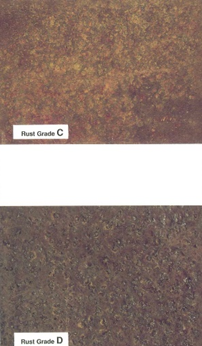
- Condition A – Intact Mill scale;
- Condition B – Rust and mill scale;
- Condition C – Totally rusted; and
- Condition D – Totally rusted and pitted
and three conditions of previously painted steel:
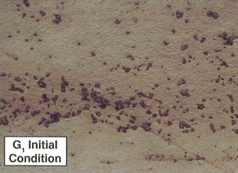
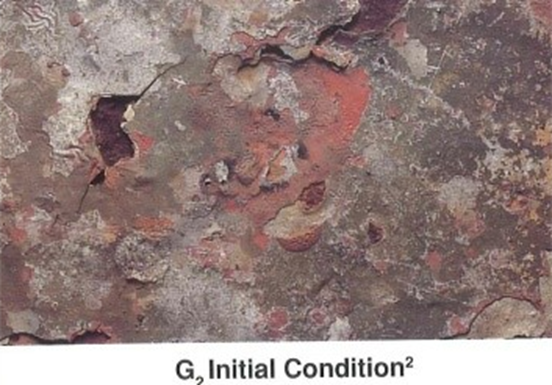
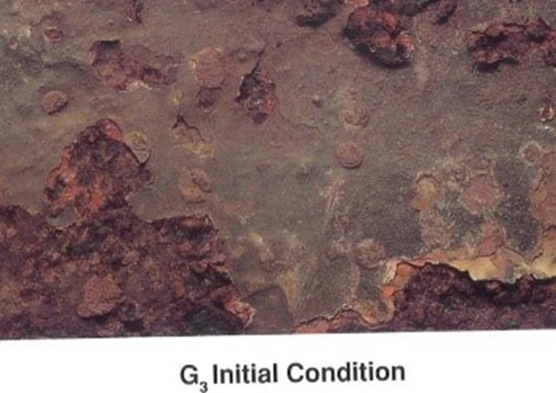
- Condition G1 – Aged coating with extensive pinpoint rusting;
- Condition G2 – Aged coating with moderating pitting; and
- Condition G3 – Aged coating with severe pitting.

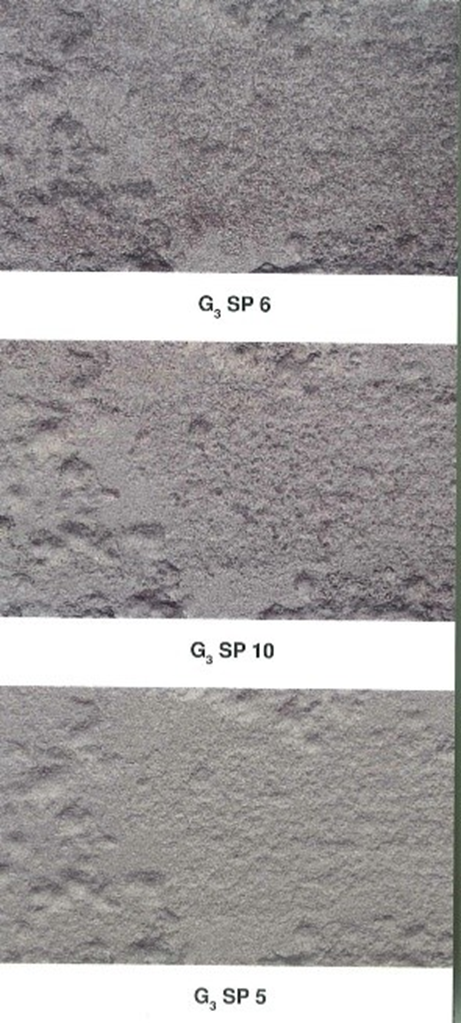
Post-blast conditions include:
- SSPC-SP 7/NACE 4 (Brush-off Blast Cleaning),
- SSPC-SP 6/NACE 3 (Commercial Blast Cleaning),
- SSPC-SP 10/NACE 2 (Near-white Metal Blast Cleaning), and
- SSPC-SP 5/NACE 1 (White Metal Blast Cleaning) for Conditions B, C, D, G1, G2, G3, as well as SSPC-SP 14/NACE 8 (Industrial Blast Cleaning) for conditions G1, G2, G3.
The images shown left represent Condition D (Rusted/pitted) and Condition G3 (Aged coating with severe pitting) prepared to a Commercial Blast (SP 6), a Near-white Blast (SP 10) and a White Metal Blast (SP 5).
Note that Condition A (mill scale) only contains post-blast images for SSPC-SP 10/NACE 2 and SSPC-SP 5/NACE 1. Silica sand was used to prepare all surfaces, so the abrasive did not impart any color.
SSPC-VIS 1 also contains images depicting the appearance of SSPC-SP5 produced with different metallic and non-metallic abrasives as well as the effect of surface profile depth, angle of view, and lighting on the appearance of SSPC-SP5.
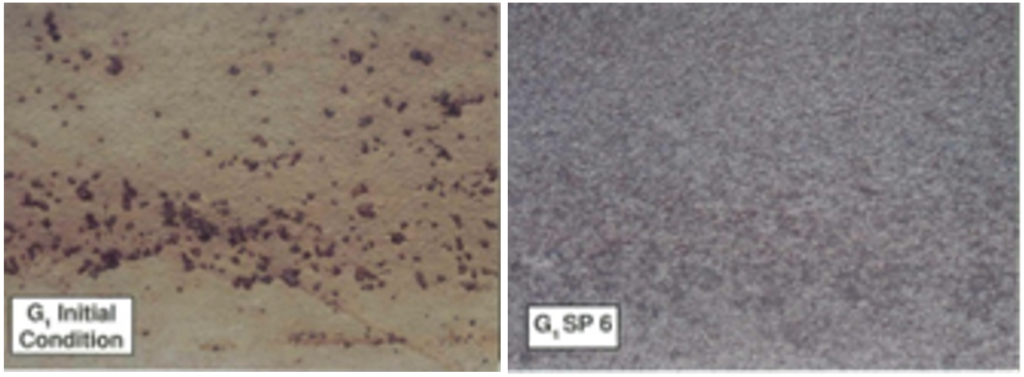
To use the guide, the condition of the existing steel surface is examined and the image closest to the actual surface is selected from the seven options listed above. For example, let’s assume the existing steel contains an aged coating with some evidence of pinpoint rusting – Condition G1 should be selected. Based on the specified surface cleanliness requirement, the post-blast photo is selected (e.g., specification requires a Commercial Blast [SSPC-SP 6], so photo G1 SP 6 is selected and compared to the post-blast condition). The photos in the visual guide are approximately 9 square inches, so they match the written definition for sizes of the areas to be examined. The size of the images shown are reduced to fit in the article.
Note that it is not the intent that each 9 square inches of prepared steel be inspected with the visual guide, as this approach could cause significant project delays. Rather, the photo is used to “calibrate the eyes” to locate areas of non-conformance (i.e., excessive staining beyond that allowable, or actual mill scale, rust, or paint when only staining is allowed). In some cases, the visual guide is used in conjunction with a dull putty knife when intact materials are allowed to remain, as is the case for SSPC-SP 7/NACE 4 and SSPC-SP 14/NACE 8.
SSPC-VIS 3 (power and hand tool cleaning), SSPC-VIS 4 (water jetting), and SSPC-VIS 5 (wet abrasive blast cleaning) are used the same as SSPC-VIS 1, but they have different initial condition options and post-cleaning images.

Using SSPC Visual Guides to Create a Project-Specific Cleanliness Standard
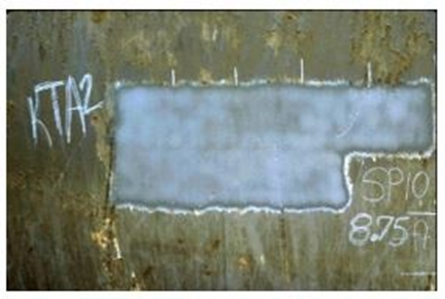
The images depicted in the SSPC visual guides (both initial condition and post-surface preparation) represent the differences in appearance of the degrees of cleaning on the specific steel that was used to create the guide. Since your existing steel will not be identical to that used to develop the guide, although the pictures in the guide will be similar, they will not precisely match the appearance of your structure before and after surface preparation. As a result, it is helpful to create a project-specific cleanliness standard (test section or mock-up, illustrated at left), before work begins, to establish the appearance of the specified degree of cleaning on a small, representative section of the structure that is to be prepared. In fact, some specifications require that this be done before any work begins. Note that if the existing condition of the structure varies, more than one test section may need to be generated.
The visual guides are used to help establish the specified degree of cleaning on the test section(s). Once established, the test section(s) becomes the visual guide for the project. The agreed-upon condition can be preserved by taking digital images using appropriate lighting. Even if the project specification does not require a test section, the inspector may suggest that the contractor prepare one (or more), so that all parties are on the same page regarding the level of cleanliness required. Another benefit to developing a test section is that the surface profile can be measured to verify conformance to the specified depth (and peak density, if required) prior to production blast cleaning and if the profile is not compliant, abrasive of the appropriate size can be obtained before the production work begins.
By creating this visual representation of the specified cleanliness on the actual structure (or multiple areas on a single structure), the effect of the initial condition on post-preparation appearance is accounted for. Workers, QC and QA inspectors, as well as job superintendents and coating suppliers can all view the jobsite standard and understand the expectations prior to and during production surface preparation work. Development of this jobsite standard may take a couple of hours but could save countless hours of disagreements that can have a significant impact on productivity and project schedule.
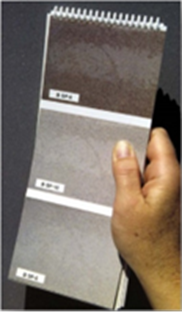
Summary
This edition of the Certified Coating Inspector Forum described the proper use of the SSPC visual guide for abrasive blast cleaning and how it may be used to assist in creating a project-specific surface cleanliness standard. Development of a jobsite visual standard can help reduce subjectivity and potential disagreements, while improving productivity and maintaining quality. It can also be valuable in verifying that the correct surface profile is being generated prior to production work.
Very good article
The performance level of coatings is ultimately determined by the degree of surface preparation achieved prior to application.
The higher the degree of surface preparation achieved, the greater the long-term performance.
Vessels and pipes experience aggressive service conditions and products specified only be applied to carbon steel surfaces which have been abrasive blast cleaned to a minimum standard of Sa2½ (ISO 8501-1:2007), or SSPC SP10
As it is pointed out to use the guide, the condition of the existing steel surface is examined and the image closest to the actual surface is selected from the seven options listed .
the photos are used to “calibrate the eyes” to locate areas of non-conformance (i.e., excessive staining beyond that allowable, or actual mill scale, rust, or paint when only staining is allowed).
the proper use of the SSPC visual guide for abrasive blast cleaning and how it may be used to assist in creating a project-specific surface cleanliness standard.
Development of a jobsite visual standard can help reduce subjectivity and potential disagreements
Thank you for reading!