KTA’s Certified Coating Inspector Forum Volume 3, Issue No. 3 – March 2024
William Corbett, COO
AMPP Senior Certified Coating Inspector & Certified Protective Coating Specialist
KTA’s Certified Coating Inspector Forum is designed to provide professional development/continuing education on standards, inspection practices, new instruments, and other topics to help keep certified AMPP and FROSIO coating inspectors current. It represents the views of the author and KTA-Tator, Inc. It may or may not represent the views of AMPP: The Association for Materials Protection & Performance, even though SSPC, NACE, and AMPP standards are frequently referenced in the content.
Introduction
The February 2024 edition of the Certified Coating Inspector Forum included information on the difference between rust-back and flash rust. Rust-back was described as rusting that occurs when steel is prepared using dry methods (without a surface passivator) and remains uncoated for a given period such that moisture and oxygen in the air react with the uncoated steel, causing it to rust (i.e., rust back). Flash rust was described as rusting that occurs when steel is prepared using wet methods, such as wet abrasive blast, vapor blast, or water jetting, and there is no passivator added to the water. This article describes products that may be used to remove flash rust (or rust back) without having to re-blast the surfaces, and how to verify the products are being applied and rinsed properly.
What do the Industry Surface Cleanliness Standards Say About Flash Rust?
The SSPC/NACE Surface Preparation Standards (now managed by AMPP) for wet methods of surface preparation state that an inhibitor/passivator (e.g., Hold Blast® or Hold Tight®) can be used to retard flash rust, when permitted by the coating manufacturer. If disallowed, the tolerance level for flash rusting should be specified (e.g., light, moderate, heavy) as depicted in SSPC-VIS 4[1] for water jetting and SSPC-VIS 5[2] for wet abrasive blast cleaning.
What if the Flash Rust Occurs, but is not Allowed
In many cases, coating over flash rust is not desirable unless a surface tolerant coating is used, and the service environment is somewhat benign. So, what do you do when flash rusting can’t be coated over (i.e., when surface tolerant coatings aren’t specified, the service environment is demanding, etc.) and re-blasting with dry abrasive isn’t feasible or desirable? Flash rust removers, if approved by the specifier and manufacturer, could be the answer. These products effectively remove flash rust from steel surfaces without re-blasting. Further, if “light” flash rusting is permitted by the project specification but becomes moderate or heavy, flash rust removers can be used to effectively remove all the flash rust, even the “light” level. Like any materials, it is important that they be used properly.
Following is the procedure for using one of the flash rust removal systems, Chlor*Rid SP8 Gel/Rinse.
Chlor*Rid SP8 Gel is a field-applied, water-soluble pickling agent containing citric acid (pH < 2) that can be brushed, rolled (pictured), or sprayed (airless spray is recommended) onto a flash-rusted surface at 12-16 mils wet film thickness. Given the acidity of the gel, it must be subsequently removed from the surface (after the recommended dwell time, typically 30 minutes) using Chlor-Rid SP8 Rinse, which contains 2-dimethylaminoethanol (pH 11.2 after dilution). These products, when used correctly are “coating neutral,” which means they do not form a film on the surface and do not leave a residue. Further, in lieu of re-blasting, the Chlor*Rid SP8 Gel/Rinse may be used to remove rust-back when the cleanliness of dry abrasive blast cleaned steel deteriorates before it is coated.
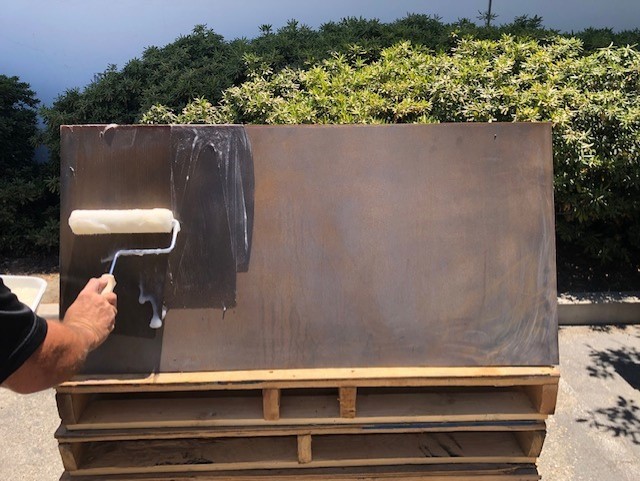
Verifying Proper Use
As certified coating inspectors, one of our roles is to verify specified or selected products are used properly. Flash rust removers are no exception. Here are sixteen key inspection checkpoints/steps to consider when Chlor*Rid SP8 Gel/Rinse is specified or used.
Chlor*Rid SP8 Gel
1. While a project specification may not invoke the use of flash rust removers, the contractor may elect to use them to reduce the amount of rework and minimize project delays. When this happens, verify that the contractor has received the necessary approvals (in writing) from the owner/specifier and the coating manufacturer prior to use.
2. Obtain a copy of the product application and safety data sheet (SDS) and read them carefully. Verify the contractor has done the same.
3. Prior to application, verify all visible grease, oil, and other contaminants have been removed from the surfaces per SSPC-SP 1, Solvent Cleaning.
4. Flash rust removers are designed for use on wet abrasive blast cleaned surfaces that have developed flash rust. Verify the surfaces complied with the specified level of surface cleanliness prior to the formation of flash rust. The minimum surface cleanliness level (prior to formation of flash rust) is SSPC-SP 6/NACE No. 3, Commercial Blast Cleaning for the Chlor*Rid SP8 Gel/Rinse products. Note that the Chlor*Rid SP8 Gel/Rinse process is not selective in the origin of the rust it will remove. That is, when used post-blast it will remove all rust staining, even that which is permitted by the SSPC-SP 6 (and SSPC-SP 10) surface cleanliness standards, potentially leaving a higher degree of surface cleanliness than originally specified.
4. Verify the product is mixed using a mechanical mixing blade and verify the cleanliness of the mixing blade prior to each use.
5. The effectiveness of the product is based, in part, on application of the correct thickness to the flash rusted surfaces. Verify the applicator is using a wet film thickness gage that conforms to ASTM D4414[3] (see image below) and that the product is applied 12-16 mils thick. Insufficient thickness will limit the effectiveness of the product, while excessive thickness will result in sagging on vertical surfaces.
6. Eye, skin, and respiratory protection are listed in the SDS. Verify you are properly protected if near the area where the product is being applied.
7. Verify the correct application procedure. The Gel should be applied starting at the top of vertical surfaces and proceed downward.
8. Verify adequate dwell time, which is approximately 30 minutes at 70°F. The Gel should not be allowed to completely dry on the surfaces. The amount of surface treated should not exceed that which can be revisited and rinsed 30 minutes later (shorter times may be required during warmer temperatures).
9. While the Chlor*Rid SP8 Gel is biodegradable and non-hazardous, it is a good idea to confirm that the contractor is aware of any local environmental regulations that may be triggered by its use.
Chlor*Rid SP8 Rinse
1. Obtain a copy of the product application and safety data sheet (SDS) and read them carefully. Verify the contractor has done the same.
2. Verify the concentrated product is diluted with deionzed water. Potable water may be used provided it contains < 15 ppm chlorides.
3. Verify the correct ratio of product-to-water is used. For example, Chlor*Rid SP8 Rinse is recommended to be used at a 1:100 dilution (e.g., 1 gallon of SP8 Rinse to 100 gallons of water).
4. Verify the application equipment and any minimum pressures required. The Chlor*Rid SP8 Gel should be removed with Chlor*Rid SP8 Rinse using a pressure washer capable of producing a minimum 2,500 psi water pressure (3,500-5,000 psi is recommended).
5. Eye, skin, and respiratory protection are listed in the SDS. Verify you are properly protected if near the area where the SP8 Rinse is being used.
6. Verify the correct rinsing procedure. On vertical surfaces, the SP8 Rinse should start at the top and proceed downward.
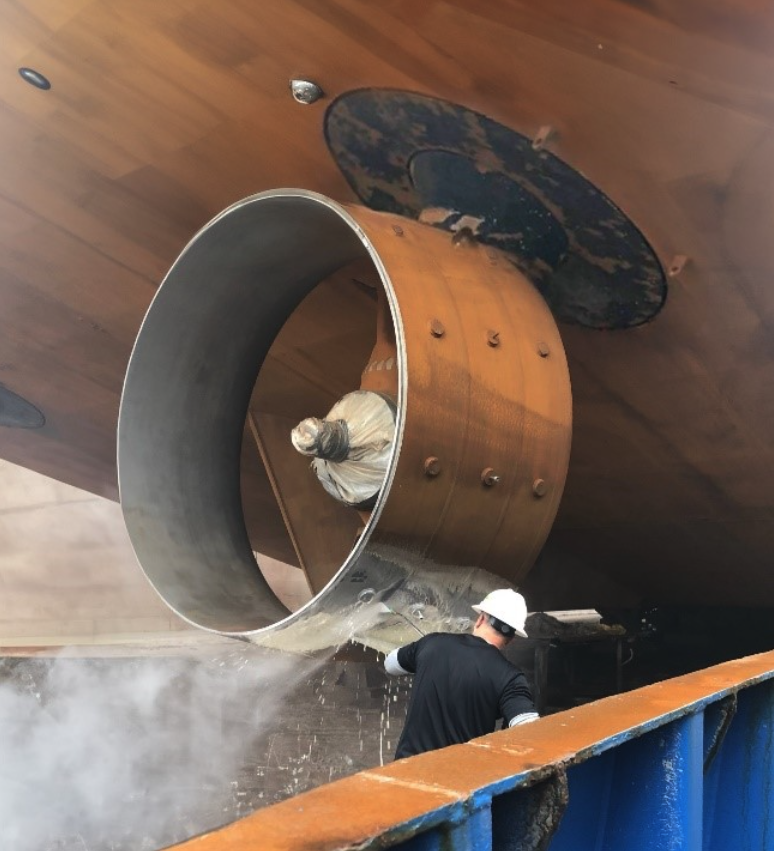
Application of SP8 Rinse to remove SP8 Rinse to remove SP8 Gel from the surface. Photo courtesy of Corrosion Innovations
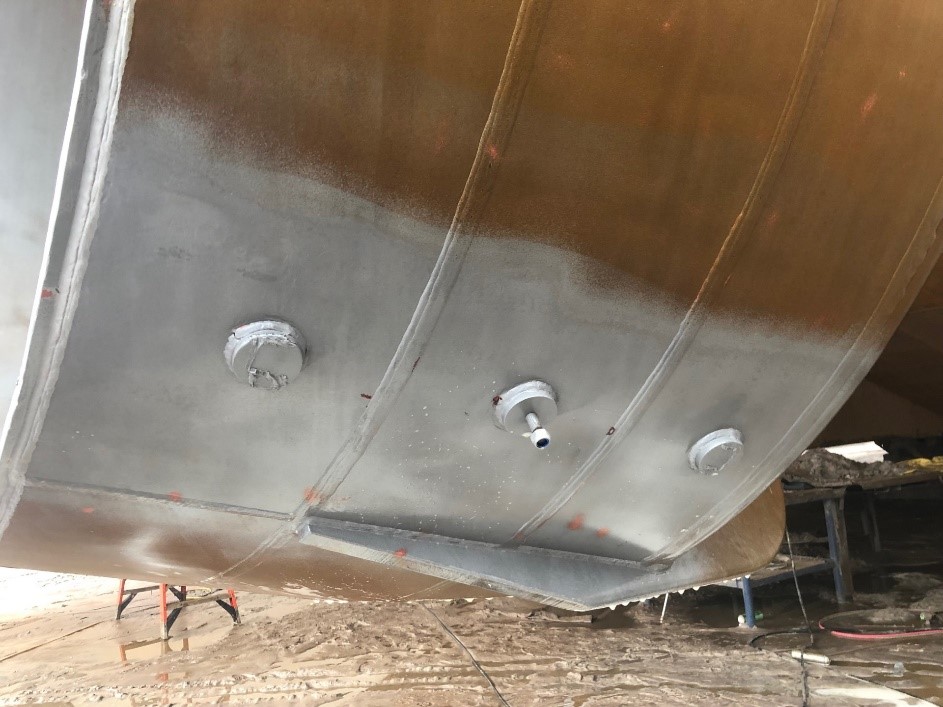
Surfaces free of flash rust after treatment. Photo courtesy of Corrosion Innovations.
7. Even though Chlor*Rid SP8 Rinse is biodegradable and non-hazardous, it is a good idea to confirm that the contractor is aware of any local environmental regulations that may be triggered by its use.

Summary
This brief article described how flash rust can be removed from abrasive blast cleaned steel surfaces without having to incur material and labor costs associated with a re-blast. The article also listed several key checkpoints/steps that an inspector needs to consider when inspecting a project that specifies the use of flash rust removers, or when a contractor employs them.
[1] SSPC VIS 4/NACE VIS 7, “Guide and Reference Photographs for Steel Surfaces Prepared by Waterjetting”
[2] SSPC VIS 5/NACE VIS 9, “Guide and Reference Photographs for Steel Surfaces Prepared by Wet Abrasive Blast Cleaning”
[3] ASTM D4414, Standard Practice for Measurement of Wet Film Thickness by Notch Gages
Great article from the KTA University .
Very thorough description how flash rust can be removed together with the
checkpoints/steps that an inspector needs to consider when inspecting a project that specifies the use of flash rust removers
Systematic inspection is required to check all the field-applied, water-soluble pickling agent is effectively removed
Thanks for the comment!