KTA’s Certified Coating Inspector Forum Volume 3, Issue No. 2 – February 2024
William Corbett, COO
AMPP Senior Certified Coating Inspector & Certified Protective Coating Specialist
KTA’s Certified Coating Inspector Forum is designed to provide professional development/continuing education on standards, inspection practices, new instruments, and other topics to help keep certified AMPP and FROSIO coating inspectors current. It represents the views of the author and KTA-Tator, Inc. It may or may not represent the views of AMPP: The Association for Materials Protection & Performance, even though SSPC, NACE, and AMPP standards are frequently referenced in the content.
Introduction
Several years ago, Douglas Reardon (KTA) posted an article to KTA University titled, “Window of Time – Surface Preparation to Painting.”1 In his article he discusses the purpose of invoking a “prep-to-prime” requirement, lists industry references, questions the variability in time periods specified, and explores a performance-based alternative. When conformance to specified time intervals isn’t feasible or practical, there are ways to minimize or eliminate the risk of rust-back that include dehumidification and surface passivation. While certainly feasible, dehumidification can be expensive, and is subject to having the ability to contain the area needing to be dehumidified. So while the interior of a tank or vessel may be easy to control, a bridge, pipeline, or a tank exterior is reliant on the quality of the containment to use dehumidification efficiently. Surface passivation, on the other hand, has been used for decades to retard rust back until the surfaces can be primed, and is not subject to the costs and concerns associated with controlling the environment. This article describes what these passivators are, and how to verify they are being applied correctly.
Distinguishing Rust-Back from Flash Rust
The terms Rust-Back and Flash Rust are frequently used interchangeably. But in the surface preparation world they hold two different meanings. Flash rust is a term that is used to describe what happens to steel when it is prepared using wet methods, such as wet abrasive blast, vapor blast, or water jetting, and there is no passivator added to the water. Since water is an electrolyte, in the presence of oxygen it represents the fourth and final element of a corrosion cell, and in effect causes the steel to rust. Because it happens quickly, it is called flash rust.
Rust-back is a term that is used to describe steel that is prepared using dry methods (without a surface passivator) but remains uncoated for a given period such that moisture and oxygen in the air reacts with the uncoated steel, causing it to rust-back. Depending on prevailing conditions (e.g., low or high humidity, presence of chemical contamination, etc.) rust-back can happen slowly or quickly.
The SSPC/NACE Surface Preparation Standards (now managed by AMPP) for wet methods of surface preparation state that an inhibitor/passivator can be used to retard flash rust, when permitted by the coating manufacturer. If not allowed, then the tolerance level for flash rusting should be specified (e.g., light, moderate, heavy) as depicted in SSPC-VIS 42 for water jetting and SSPC-VIS 53 for wet abrasive blast cleaning. In many cases, coating over flash rusting is not desirable unless a surface tolerant coating is used, and the service environment is somewhat benign.
The SSPC/NACE Surface Preparation Standards (now managed by AMPP) for most of the dry abrasive blast cleaning levels (SSPC-SP 6 Commercial Blast, SP 10 Near-White Blast, SP 5 White Metal Blast, SP 14 Industrial Blast, and SP 18 Thorough Spot and Sweep Blast) and two power tool cleaning standards (SP 15 Commercial Grade Power Tool Cleaning, and SP 11 Power Tool Cleaning to Bare Metal) do not permit rust-back to occur; otherwise, the surfaces must be re-prepared to the specified degree of cleanliness prior to coating. These specifications do not address the use of an inhibitor/passivator to preserve the cleanliness, nor do they prohibit it.
What are Surface Passivators?
Surface passivators are chemical solutions that can be applied during or immediately after wet methods of preparation to prevent flash rust or after dry methods of preparation (dry abrasive blast, power tool cleaning) to prevent the surfaces from rusting until they can be protected with coatings.

Photo courtesy of Corrosion Innovations.
In effect, surface passivators chemically change the active surface of prepared steel to a much lower reactive state. There are a variety of products on the market that can be used to slow the onset of rust for up to 72 hours, depending on the prevailing environment; Hold*Blast™ is used as an example. Most passivators are concentrates that are diluted with potable water. For example, Hold*Blast™ uses a chemical called Triethanolamine, a water-soluble amine-based inhibitor that has a pH of 10.8 (+/-0.2) once diluted. The inherent alkalinity retards the formation of rust.

Verifying Proper Use
As certified coating inspectors, one of our roles is to verify specified or selected products are used correctly. Surface passivators are no exception. Here are eleven key inspection checkpoints/steps to consider when surface passivators are proposed or used.
1. Verify that the specifier has approved the specific passivator for the project. Passivators are not removed prior to coating application, so the specifier will verify with the coating manufacturer that the coating system is compatible with the passivated surfaces.
2. While a project specification may not invoke the use of surface passivators, the contractor may elect to use them to reduce the amount of rework and project delays. When this happens, verify that the contractor has received the necessary approvals (in writing) from the owner/specifier and the coating manufacturer.
3. Obtain a copy of the product application and safety data sheet (SDS) and read them carefully. Like coatings, not all surface passivators are the same.
4. While passivators are typically biodegradable and non-hazardous, it is a good idea to confirm that the contractor is aware of any local environmental regulations that may be impacted by their use.
5. Determine whether surface soluble salt testing is invoked by specification. The use of surface passivators can mask the presence of surface soluble salt contamination such as chlorides, sulfates, and nitrates. Testing for these and other soluble salts should be performed after surface preparation, but before application of the passivator.
6. Verify conformance to storage temperature and application temperature ranges, which may be product specific. These ranges are typically noted on the product data sheet or application instructions.
7. Verify the concentrated product is diluted with potable water and that the correct ratio of passivator-to-water is used. For example, Hold*Blast™ is recommended to be used at a 1:50 dilution (e.g., 1 gallon of passivator to 50 gallons of potable water).
8. If the surface passivator will be incorporated into the water during wet abrasive blast cleaning, slurry blasting, vapor blasting, or water jetting, verify that the contractor follows the methods for dilution, etc. as directed by the manufacturer of the passivator.
9. Verify the application equipment and any minimum pressures that are required. Most surface passivator solutions can be applied to prepared surfaces using a pressure washer, where the diluted concentrate is drawn from a reservoir tank. After application no additional washing or removal steps are required other than in areas of pooling (see #11).
10. Verify treated areas are protected from rain, immersion, splash, and excessive condensation; otherwise, the effectiveness of the passivator will be significantly lessened.
11. Watch for pooling/puddling of the applied passivator and make sure it is removed using compressed air or other means. The Triethanolamine passivator used in Hold*Blast™ is an oilier amine and has the potential to cause coating issues if it is allowed to pool or puddle on surfaces. “Birdbaths” on floating roof structures are of particular concern due to the warping of the roof plate.
Summary
This brief article differentiated between flash rust and rust back, how surface passivators can be used to help preserve prepared steel surfaces, and several key checkpoints/steps that an inspector needs to consider when inspecting a project that specifies the use of passivators, or when a contractor considers employing them.
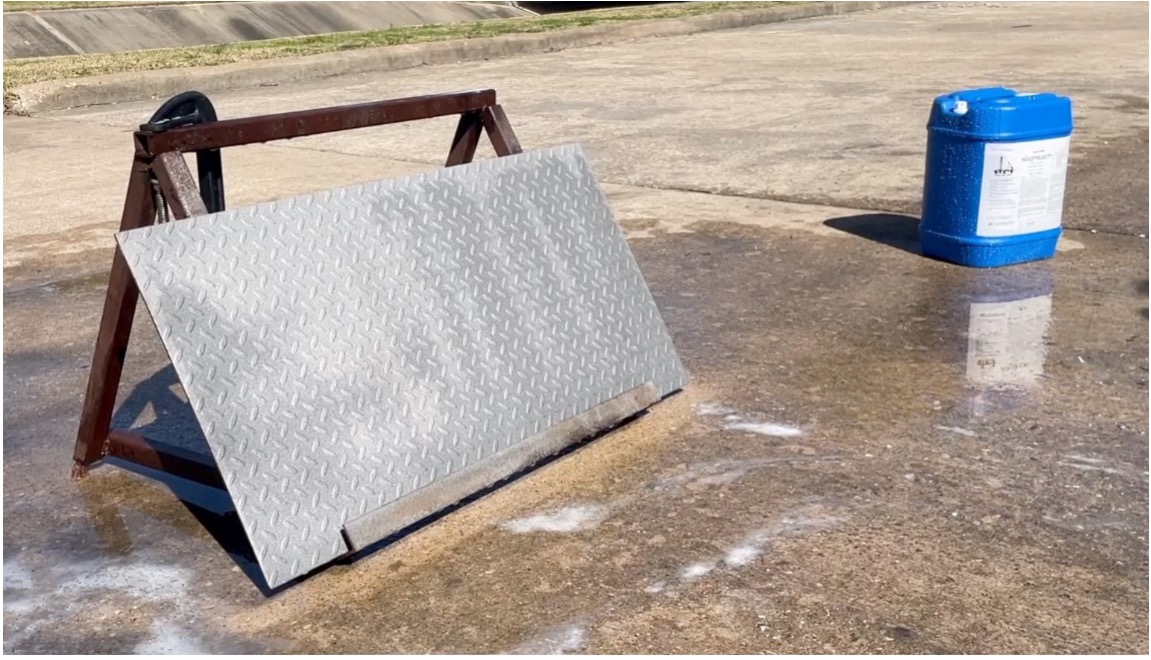
Photo courtesy of Corrosion Innovations.
[1] https://kta.com/kta-university/surface-preparation-prep-to-prime/
[2] SSPC VIS 4/NACE VIS 7, “Guide and Reference Photographs for Steel Surfaces Prepared by Waterjetting” [1] SSPC VIS 5/NACE VIS 9, “Guide and Reference Photographs for Steel Surfaces Prepared by Wet Abrasive Blast Cleaning”
[3] SSPC VIS 4/NACE VIS 7, “Guide and Reference Photographs for Steel Surfaces Prepared by Waterjetting” [1] SSPC VIS 5/NACE VIS 9, “Guide and Reference Photographs for Steel Surfaces Prepared by Wet Abrasive Blast Cleaning”
Good, concise information about this class of passivating compounds, Bill.
Gordon
Thank you for the comment!
Very useful article
Great article providing facts and imparting knowledge in the wide field of flash rust , rust back and surface passivators
Very interesting, non hazardous , like to try this Passivators and see the results and thanks for the knowledge