KTA’s Certified Coating Inspector Forum Issue No. 3 – July 2022
KTA’s Certified Coating Inspector Forum is designed to provide continuing education on standards, inspection practices, new instruments, and other topics to help keep certified AMPP and FROSIO coating inspectors current. It is occasionally written blog style, and represents the views of the author and KTA-Tator, Inc. It may or may not represent the views of AMPP: The Association for Materials Protection & Performance, even though SSPC, NACE, and AMPP standards are frequently referenced in the content.
Coating specifications frequently reference industry standards developed by organizations such as SSPC (now AMPP), ASTM, ISO, and NACE (now AMPP). While specifications may reference a specific version or year of the standard, many simply state that “the latest version of the standard applies.” Many standards writing organizations require a review of the content of their documents every 5-years (or more frequently), and as a result, updates/revisions to standards can and oftentimes do occur. And new standards are developed and published to fill voids when a need for a standard is identified. Keeping current with revisions and updates to existing standards, as well as newly published standards that impact coating work can be very challenging. However, as trained and certified coating inspectors we have an obligation to recognize that new standards and revisions are always being published and remain current with changes to the industry standards that impact our work.
Over the years, SSPC (sometimes jointly with NACE International) developed and published no less than 30 surface preparation standards; three have been discontinued and others have been subdivided into multiple standards. The table below lists all the surface preparation standards that have been published (through 2022) and their status as active or discontinued.
Code | Title | Status |
---|---|---|
SSPC-SP 1 | Solvent Cleaning | Active |
SSPC-SP 2 | Hand Tool Cleaning | Active |
SSPC-SP 3 | Power Tool Cleaning | Active |
SSPC-SP 4 | Flame Cleaning of New Steel | Discontinued, not replaced |
SSPC-SP 5/ NACE 1 | White Metal Blast Cleaning | Active |
SSPC-5 (WAB)/ NACE WAB-1 | White Metal Wet Blast Cleaning | Active |
SSPC-SP 6/ NACE 3 | Commercial Blast Cleaning | Active |
SSPC-6 (WAB)/ NACE WAB-3 | Commercial Wet Blast Cleaning | |
SSPC-SP 7/ NACE 4 | Brush-off Blast Cleaning | Active |
SSPC-7 (WAB)/ NACE WAB-4 | Brush-off Wet Blast Cleaning | Active |
SSPC-SP 8 | Pickling | Active |
SSPC-SP 9 | Weathering, Followed by Blast Cleaning | Discontinued, not replaced |
SSPC-SP 10/ NACE 2 | Near-white Blast Cleaning | Active |
SSPC-10 (WAB)/ NACE WAB-2 | Near-white Wet Blast Cleaning | Active |
SSPC-SP 11 | Power Tool Cleaning to Bare Metal | Active |
SSPC-SP 12/ NACE 5 | Surface Preparation and Cleaning of Steel and Other Hard Materials by High and Ultrahigh Pressure Water Jetting Prior to Recoating | Discontinued, replaced by WJ1-WJ4 |
SSPC-SP WJ 1/ NACE WJ-1 | Waterjet Cleaning of Metals – Clean to Bare Substrate | Active |
SSPC-SP WJ 2/ NACE WJ-2 | Waterjet Cleaning of Metals – Very Thorough Cleaning | Active |
SSPC-SP WJ 3/ NACE WJ-3 | Waterjet Cleaning of Metals – Thorough Cleaning | Active |
SSPC-SP WJ 4/ NACE WJ-4 | Waterjet Cleaning of Metals – Light Cleaning | Active |
SSPC-SP 13 | Surface Preparation of Concrete | Active |
SSPC-SP CAB-1 | Abrasive Blast Cleaning of Concrete and Cementitious Materials – Thorough Blast Cleaning | Active |
SSPC-SP CAB-2 | Abrasive Blast Cleaning of Concrete and Cementitious Materials – Intermediate Blast Cleaning | Active |
SSPC-SP CAB-3 | Abrasive Blast Cleaning of Concrete and Cementitious Materials – Brush Blast Cleaning | Active |
SSPC-SP 14/ NACE 8 | Industrial Blast Cleaning | Active |
SSPC-14 (WAB)/ NACE WAB-8 | Industrial Wet Blast Cleaning | Active |
SSPC-SP 15 | Commercial Grade Power Tool Cleaning | Active |
SSPC-SP 16 | Brush-off Blast Cleaning of Coated and Uncoated Galvanized Steel, Stainless Steels, and Non-Ferrous Metals | Active |
SSPC-SP 17 | Thorough Abrasive Blast Cleaning of Non-Ferrous Metals | Active |
SSPC-SP 18 | Thorough Spot and Sweep Blast Cleaning for Industrial Coating Maintenance | Active |
In December 2020, SSPC-SP 11, Power Tool Cleaning to Bare Metal was updated. In September 2019, SSPC-SP 17 was published and in December 2020, SP 18 was added. Let’s look at the updates to SSPC-SP 11 and the basic content of the two newest standards.
Updates to SSPC-SP 11
There are two significant changes to the December 2020 revision of SSPC-SP 11, Power Tool Cleaning to Bare Metal. The first and most significant is the addition of two cleaning levels to the original one. A summary of the levels is shown in the table below. Note that if a level is not specified, Level 2 is invoked by default.
Level | Percent Overall Staining | Amount of Residue Permitted in Pit Bottoms | Minimum Profile |
---|---|---|---|
1 | 0% | None | 1.0 mil; deeper if specified |
2 | 0% | Traces in bottoms | 1.0 mil; deeper if specified |
3 | 5% | Traces in bottoms | 1.0 mil; deeper if specified |
The second significant change is related to surface profile measurement. The previous version of this standard only allowed the use of a depth micrometer (Method B in ASTM D44171) to verify the minimum 1-mil profile. The current version allows the use of depth micrometer, replica tape, or drag stylus instrument (Methods B, C, and D in ASTM D4417, respectively) to measure the resulting surface profile depth.
It should be noted that the current version of SSPC VIS 3, Guide and Reference Photographs for Steel Surfaces prepared by Power and Hand Tool Cleaning were not updates to reflect the changes and only depict Level 3. Sample images of SSPC-SP 11 from SSPC-VIS Guide 3 are shown below, for Rust Grades B, C, D and G.
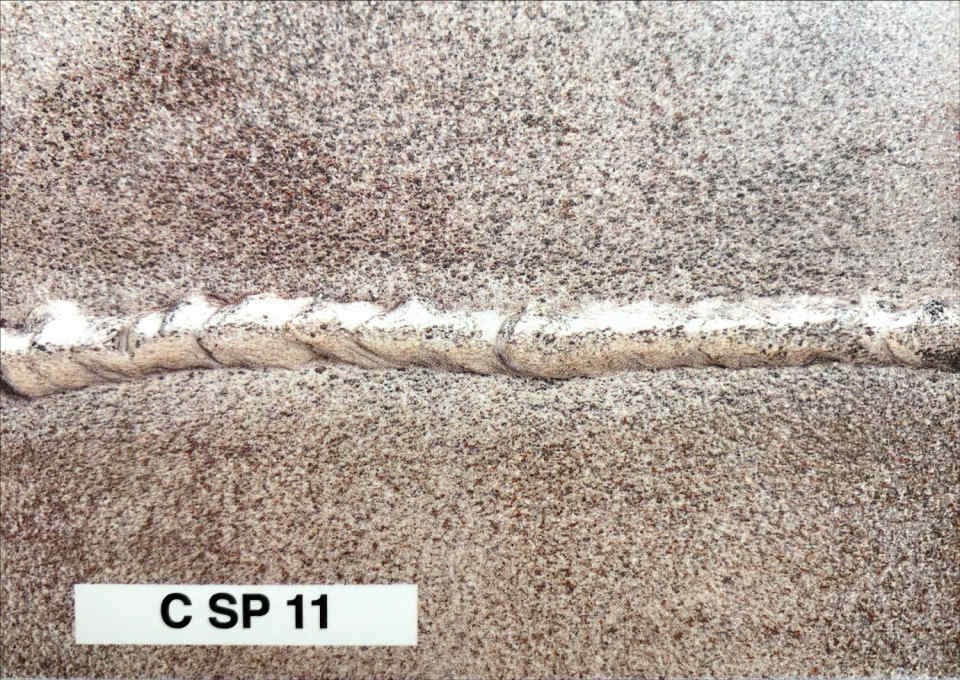
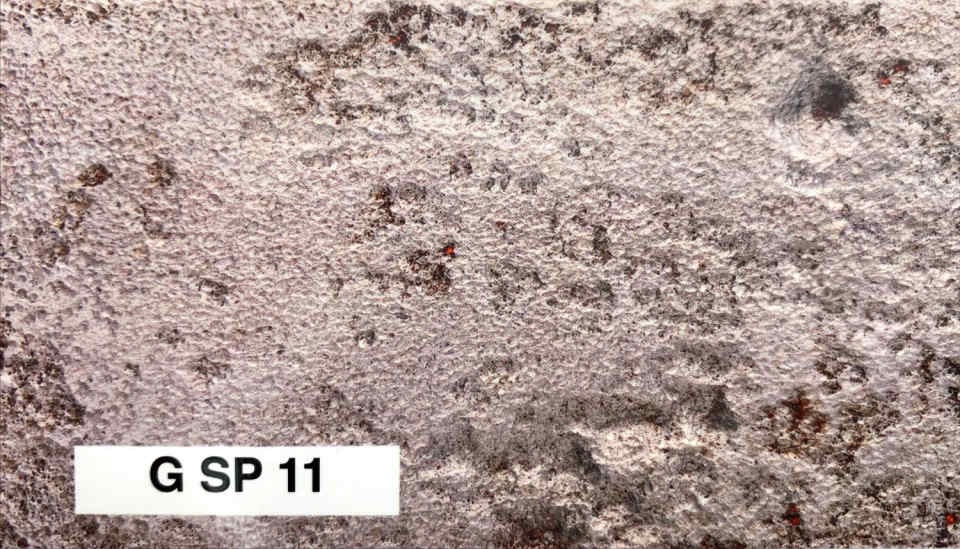
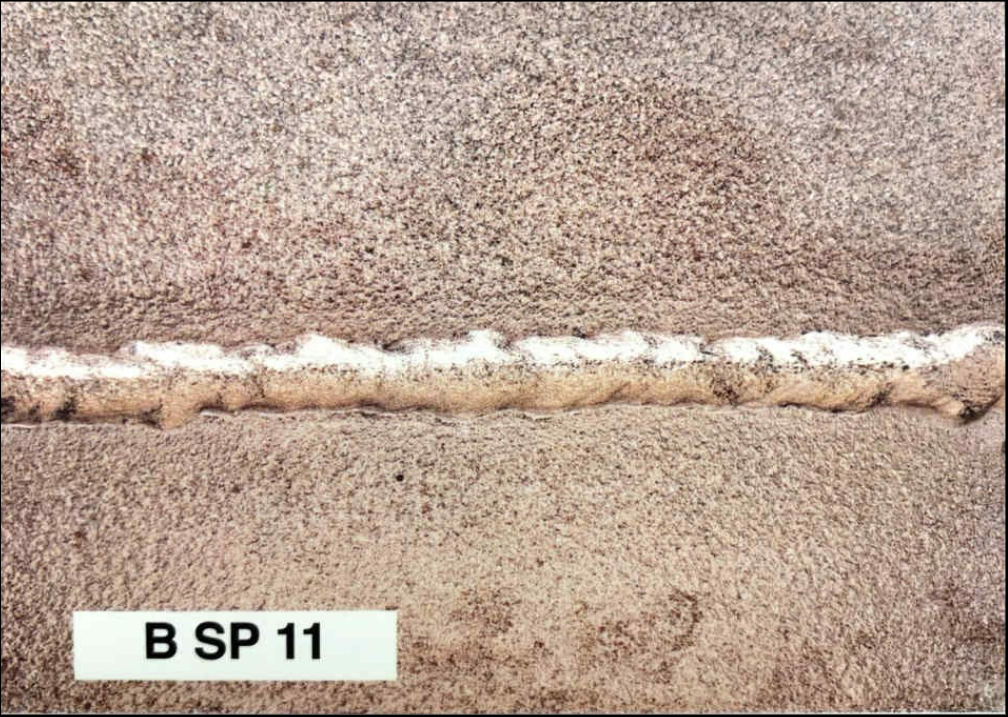
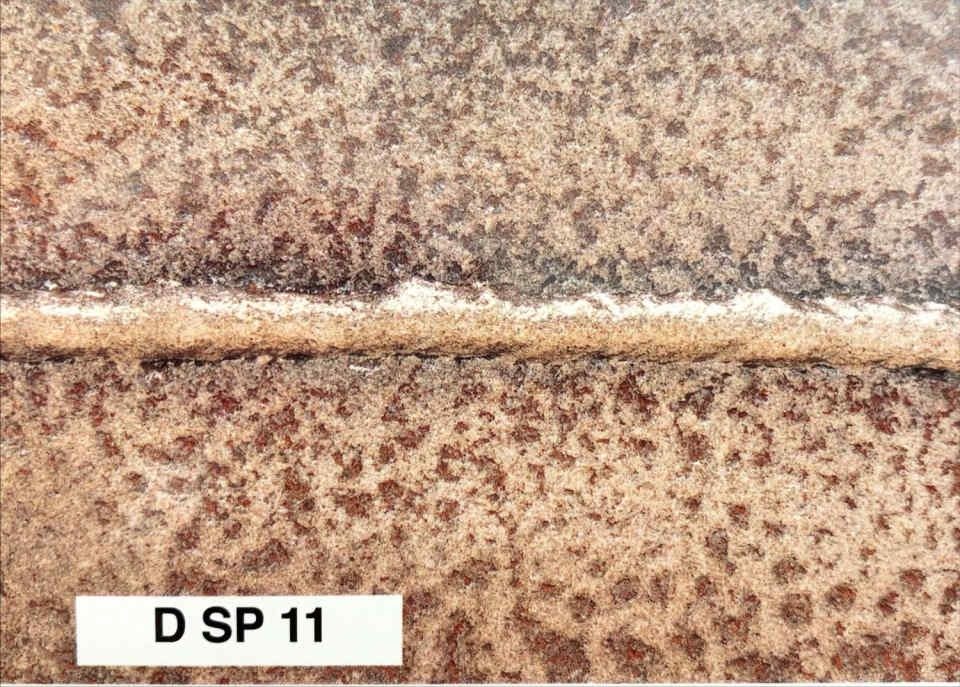

SSPC-SP 17, Thorough Abrasive Blast Cleaning of Non-Ferrous Metals
SSPC-SP 17 addresses the level of surface cleanliness achieved by abrasive blast cleaning uncoated or coated non-ferrous metal or stainless-steel surfaces and includes requirements for materials and procedures used to achieve and verify the cleanliness level. Substrates addressed by this method include but are not limited to copper and copper alloys, aluminum and aluminum alloys, and stainless steel.
Surfaces prepared according to this standard, when viewed without magnification, shall be free of all visible oil, grease, dust, dirt, oxides (corrosion products), coating, and other foreign matter. Random color variations shall be limited to no more than 5% of each unit area (9 sq.-in), and may consist of light shadows, slight streaks, or minor discolorations.
Visible deposits of grease, oil or other contaminants must be removed prior to blast cleaning (per SSPC-SP 1, Solvent Cleaning, or other pre-approved methods), and surface imperfections (sharp edges, weld spatter, etc.) may be required to be addressed per the project specification.
This standard requires the contractor to prepare a Job Reference Standard (JRS), so it’s likely that the inspector will be intimately involved in determining the acceptability of the JRS. The JRS helps to establish the procedures required to properly prepare the substrate without damaging it, as well as establish the degree of cleanliness and profile expected on the project.
Dry or wet abrasive blast cleaning may be employed to prepare the substrates, and clean mineral and slag abrasives, aluminum oxide, stainless steel, or encapsulated media may be used. The size of the abrasive is determined based on the specified surface profile depth.
Post-blast/pre-coating procedures include:
- Removal of any visible grease/oil that was deposited on blast-cleaned surfaces
- Removal of dust/residual abrasive (if blow down is used, compressed air must be tested for cleanliness per ASTM D42852)
- Removal of visible oxides that have formed on blast-cleaned surfaces
- Measurement of surface profile
Currently, there are no published visual guides illustrating SSPC-SP 17 which makes preparation of the JRS that much more critical.
SSPC-SP 18, Thorough Spot and Sweep Blast Cleaning for Industrial Coating Maintenance
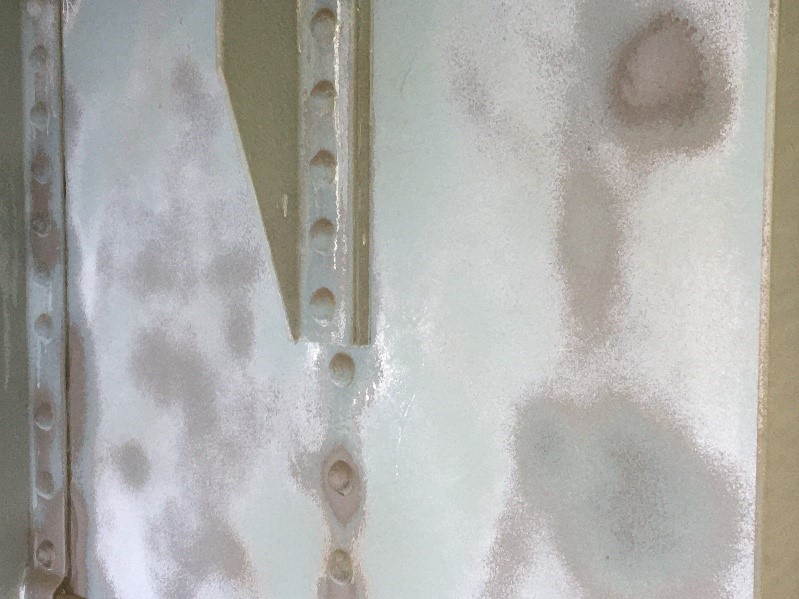
SSPC-SP 18 addresses the level of surface cleanliness achieved by abrasive blast cleaning previously coated steel surfaces. Thorough spot and sweep blast cleaning subjects the entire surface to abrasive impact. Existing coating that cannot withstand the abrasive impact is removed, while the remaining existing coating is suitably prepared and roughened for application of an additional layer of compatible coating. Areas of exposed steel are prepared to SSPC-SP 10/NACE No. 2, Near-white Metal Blast Cleaning.
Any retained existing coating shall have sufficient adhesion such that it cannot be removed from the substrate by lifting with a dull putty knife. The borders of the retained coating shall have no clear shoulder or edge at the coating/ substrate interface. If the coating can be dislodged, the area shall be rejected and cleaned again until the requirements of this standard are met. Coating that has been tapered by the blasting process in a manner that challenges adhesion and removes all sharp edges is considered well adhered. Any retained coating shall not exhibit chalking, residual corrosion staining, visible cracks, blisters, delamination, or other defects after the blast cleaning process. The retained coating shall be uniformly roughened and shall not have any area larger than 40 mm2 (~1/16 in2) that exhibits the appearance of undisturbed (unroughened) coating.
Visible deposits of grease, oil or other contaminants must be removed prior to blast cleaning (per SSPC-SP 1, Solvent Cleaning, or other pre-approved methods), and surface imperfections (sharp edges, weld spatter, etc.) may be required to be addressed per the project specification.
Similar to SSPC-SP 17, this standard requires the contractor to prepare a Job Reference Standard (JRS), so again, the inspector will likely be intimately involved in determining the acceptability of the JRS. The JRS helps to establish the degree of cleanliness and profile expected on the project.
Dry abrasive blast cleaning may be employed to prepare the substrates. Wet abrasive blast cleaning or pressurized water cleaning may be substituted if allowed by the project specification. If wet abrasive blast is employed, areas of exposed steel are prepared to SSPC-SP 10 (WAB)/NACE WAB-2; if pressurized water cleaning is used, the bare steel must conform to SSPC-SP WJ-2/NACE WJ-2.
The abrasive is selected based on the type, grade, and surface condition of the steel to be cleaned, the type of blast cleaning system used, the finished surface to be produced (cleanliness and surface profile [roughness]), and whether the abrasive will be recycled. The abrasive is required to conform to the cleanliness requirements of the SSPC Abrasive (AB) standards.
Post-blast/pre-coating procedures include:
- Removal of any visible grease/oil that was deposited on prepared surfaces
- Removal of dust/residual abrasive (if blow down is used, compressed air must be tested for cleanliness per ASTM D42853)
- Removal of visible rust-back that has formed on areas of exposed metal
- Measurement of surface profile
Currently, there are no published visual guides illustrating SSPC-SP 18, which makes preparation of the JRS that much more critical.
Summary
Surface preparation is frequently considered a key factor in determining the long-term performance of a protective coating system. The two-fold purpose of surface preparation is to clean and roughen the surface. Surface preparation standards developed by SSPC/NACE (now AMPP) and others such as ASTM and ISO are a critical component to project specifications, and verification of compliance with the standards is considered a key role of a coating inspector. Trained and certified coating inspectors must strive to remain current with changes to existing standards and be familiar with newly published standards to perform their job. This column provided insights on changes to SSPC-SP 11 and the general content of two relatively new standards (SSPC-SP 17 and SSPC-SP 18).