By Jay Helsel, PE, KTA-Tator, Inc.
Introduction – Cast iron and ductile iron are two different materials but are prepared and painted similarly. Ductile iron consists of iron, carbon, silicon, manganese, magnesium, phosphorous and sulfur, whereas ductile iron consists primarily of carbon and silicon together with nodular graphite to provide ductility. Ductile iron is commonly used in water and sewer lines. Cast iron is not as flexible or strong as ductile iron and will break if bent. It also corrodes more quickly.
Extreme care is needed when preparing cast iron and ductile iron for painting as the surface can become deteriorated by aggressive blast cleaning. Further, annealing oxide on the surface of ductile iron that remains intact after cleaning serves as a corrosion resistant protective layer.
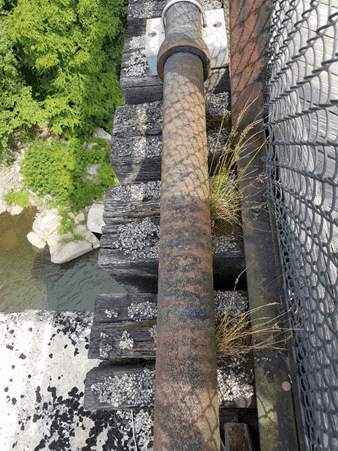
Preparation of Cast Iron/Ductile Iron
As with any substrate, successfully coating cast iron begins with proper surface preparation. The degree of cleaning required depends on the service environment (the environment in which the coating system must provide sufficient performance), the composition and properties of the coating system, and the intended service life of the installed coating. The specified preparation must also be consistent with the recommendations of the coating manufacturer. Surface preparation methods can range from simple solvent cleaning to hand and power-tool cleaning; from dry and wet abrasive blast cleaning to chemical stripping; and from water jetting to other, more nontraditional methods, such as sponge jetting and cryogenic blast cleaning with dry ice pellets. A general discussion of surface preparation by hand/power tool cleaning and abrasive blast cleaning is discussed below, followed by a more specific discussion on the preparation of ductile cast iron.
It should be noted that a separate set of surface preparation standards from those published by the Society of Protective Coatings (SSPC) have been developed by the National Association of Pipe Fabricators (NAPF) for ductile cast iron. These standards are discussed under the next section, “Cleaning Ductile Cast Iron.”
Regardless which mechanical method of preparation is used, initial cleaning should consist of removing any grease, oil or other contaminants. The guidance of NAPF 500-03-01, Surface Preparations Standard for Solvent Cleaning” can be followed to accomplish this initial cleaning.
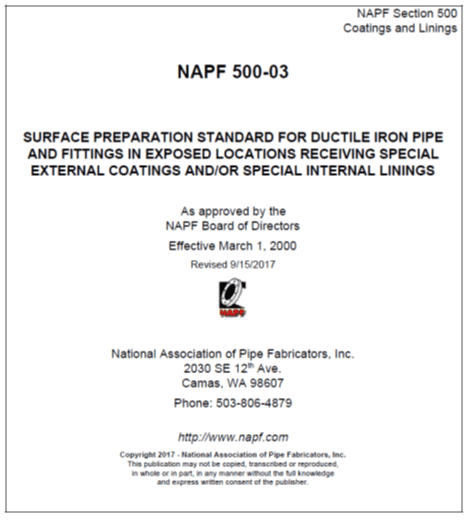
Hand and Power Tool Cleaning – General
Hand-tool cleaning, typically employed for relatively minor touch-up repairs for maintenance painting activities, is done with wire brushes, scrapers, and other tools that do not depend on electric or pneumatic power to operate.
Hand tools are only intended to remove loosely adhering materials such as loose corrosion products and loose paint. Hand tools are not intended to roughen the substrate and produce a surface profile or “anchor” pattern to facilitate adhesion of newly applied coatings.
Power-tool cleaning is typically performed with grinders, pneumatic chisels, needle scalers, rotopeen tools, and other equipment that require an electric or pneumatic power source to operate. Most of these tools can remove both loosely and tightly adhering corrosion products and paint from surfaces. Some of these tools can also produce a small surface profile. Power-tool cleaning is typically employed for maintenance repairs of small areas but can also be used when methods such as abrasive blast cleaning are not an option, but like blast cleaning, care is needed to avoid damaging the substrate. The use of hand and power tools for the preparation of ductile cast iron is discussed below in the section “Cleaning Ductile Cast Iron.”

Dry Abrasive Blast Cleaning – General
Blast cleaning with dry abrasive media is one of the most common methods for preparing a surface for coating, particularly steel structures. Although cast iron is a ferrous metal like steel, it cannot be treated the same as steel in terms of blast cleaning. The appearance of cast iron after cleaning will be different than steel and the use of the typical surface preparation standards for steel, particularly the visual standards, are difficult to apply. These differences must be recognized when blast cleaning is selected for the surface preparation of cast iron
Abrasive blast cleaning can be used to prepare both bare and painted substrates. When the surface has been previously painted, abrasive blast cleaning can be used to remove loose coating and roughen the remaining intact coating for subsequent overcoating, or to completely remove everything from the substrate, including underlying corrosion products. Abrasive blast cleaning is the most productive of all surface-preparation methods. The hardness and mass of the abrasive media, combined with the velocity of the abrasive as it exits a nozzle at high speed, generates high levels of energy. As the abrasive media impacts a surface, it can remove existing coating layers and corrosion products, while simultaneously generating a surface profile or anchor pattern. The level of cleanliness that is achieved is ultimately determined by the distance that the nozzle is held from the surface and the “dwell time” that the operator employs. The depth and shape of the surface profile is determined by the type and size of the abrasive media employed, as well as the hardness of the surface being prepared. Therefore, selection of the correct type and size of abrasive media is important.
Typically, harder abrasives—those designed to achieve complete coating removal and an adequate profile—include steel grit, steel shot, and mineral abrasives such as coal slag and garnet. Softer abrasives, which are typically used to remove loose coatings and other loose material from a substrate, include aluminum/magnesium silicate, corncobs, walnut shells, limestone, or some mineral sands.
Another mineral abrasive—usually used in the form of beads—is glass. Although not frequently employed, glass-bead blasting can be used to clean and prepare certain glass, plastic, rubber, and metal surfaces. The manufacturers of glass-bead abrasives should be consulted for specific applications suitable for their materials.
An alternative to blasting with traditional dry abrasives is “sponge blasting,” which uses proprietary blast media and equipment manufactured by Sponge-Jet Inc. According to Sponge-Jet, the sponge media “is an open-celled, water-based polyurethane impregnated with abrasives.” A variety of sponge abrasive materials are available to achieve various levels of cleaning. The nature of the sponge material can allow for greatly reduced levels of dust and airborne contaminants during the blasting process.
Cleaning Ductile Cast Iron
As indicated above, the. NAPF publishes surface preparation standards specifically designed for ductile cast iron as detailed in NAPF 500-03, “Surface Preparation Standard for Ductile Iron Pipe and Fittings in Exposed Locations Receiving Special External Coatings and/or Special Internal Linings.” According to the NAPF, the inherent metallurgical and manufacturing differences for ductile cast iron preclude using the preparation standards developed for steel surfaces. One of the primary differences between cast iron and steel is that cast iron may have a layer of annealing oxide rather than mill scale. The annealing oxide adheres to cast iron better than mill scale adheres to steel, making it difficult to remove. But more importantly, an intact annealing oxide layer is a corrosion resistant and protective layer that is allowed to remain for most of the NAPF surface preparation standards. The appearance of ductile cast iron after preparation is also different than the appearance of carbon steel, so the visual guides available for steel surfaces are not representative of the appearance of ductile cast iron.
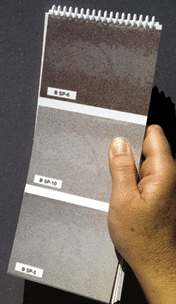
Because visual guides are not available, it is recommended that jobsite standards be prepared to agree on the appearance of the specified methods of cleaning before production work begins. The prepared surfaces can be photographed and used as a supplement to the written standards when inspecting the quality of the production work.
The NAPF standard is intended to apply to ductile cast iron used in the water and wastewater industry.. NAPF cautions that the standard is not intended for use as the basis for surface preparation for bonded coatings for buried pipeline applications. The NAPF standard, which is divided into five parts, is described in Table 1.

In addition to the specific coating types detailed by NAPF, the typical coating systems for steel can generally be applied successfully to cast iron when the surface is properly prepared. When a steel coating system is specified for cast iron, the NAPF surface preparation standard that best corresponds to the surface preparation standard required for the steel should be used.
Conclusion – Cast Iron and ductile iron can be successfully coated provided the surface is adequately cleaned and the roughness suitable to assure proper adhesion of the applied coating. Because there are no visual standards for cast iron and ductile iron to address the cleanliness, and because there is the potential for creating damage by overblasting the surface, the creation of a project mock-up is recommended.
Topics in this cast iron/ductile iron series:
Topic 1 – Preparation of cast iron/ductile iron for painting
Topic 2 – Coatings for cast iron/ductile iron
Topic 3 – Inspection of surface preparation and coating application