A commercial building’s structural support steel may not have exterior exposure, or even be visible inside the building, but in some cases — such as The New York Times building in Manhattan — it is part of the exterior facade. Visible or not, building codes generally require that structural steel be protected by a fire-resistive material, and the two major coating types used for this purpose are cementitious-based coatings and intumescent coatings. While the thick, rough appearance of cementitious coatings may be fine for many applications, intumescent coatings offer a more aesthetically pleasing way to protect exposed structural steel.
*** As seen in November 2016 Edition of Durability & Design ***
Intumescent coatings protect steel from getting too hot by swelling and charring in the event of a fire, becoming an insulating layer for the metal substrate. These coatings are rated by how long they provide such protection — typically from half an hour to four hours. Although intumescents may appear similar to other liquid-applied coatings, they have unique properties that should be understood before they are selected and specified for a project.
APPROVALS AND TESTING
In the United States, Underwriters Laboratories (UL) is a recognized authority that evaluates and approves intumescent coatings for a certain fire rating. The approval for a coating includes important details, including the type and size of steel member (e.g., beam, column, angle, etc.) and the required coating thickness. A primer and exterior finish coat may also be required as part of the system.
Failure to comply with these design requirements would likely void the UL approval for the coating, and more importantly, could jeopardize the coating’s fire protection properties. Note that the use of any primer(s) should be approved by the intumescent coating manufacturer.
Approvals and testing of intumescent coatings are divided into two categories: those offering protection from cellulosic fires and those designed for hydrocarbon-fueled fires, which burn at much higher temperatures.
Cellulosic Fires: Most house or building fires are cellulosic, and fueled by typical building materials such as timber and paper. Compared to a hydrocarbon fire, this type of fire grows more slowly and is generally of a lower intensity and temperature. Fire resistance for cellulosic fires is tested per ANSI/UL 263, “Standard for Fire Tests of Building Construction and Materials.” The temperature for testing increases gradually over time and reaches 2,000 degrees Fahrenheit at four hours.
Hydrocarbon Fires: A hydrocarbon fire is fueled by a liquid hydrocarbon (i.e., petroleum fuel) or pressurized flammable gas. This type of fire is most likely to occur at petroleum processing facilities which might include refineries and offshore drilling platforms. Testing for resistance to hydrocarbon fires follows ANSI/UL 1709, “Fire Tests of Structural Steel Protected for Resistance to Rapid Temperature Rise Fires.” In this testing, a temperature of 2,000 degrees Fahrenheit is reached within five minutes, making the test conditions much more severe. The testing also includes environmental testing for weathering exposure. This qualification testing is commonly required when intumescent coatings are applied to offshore structures, refineries, chemical facilities and others.
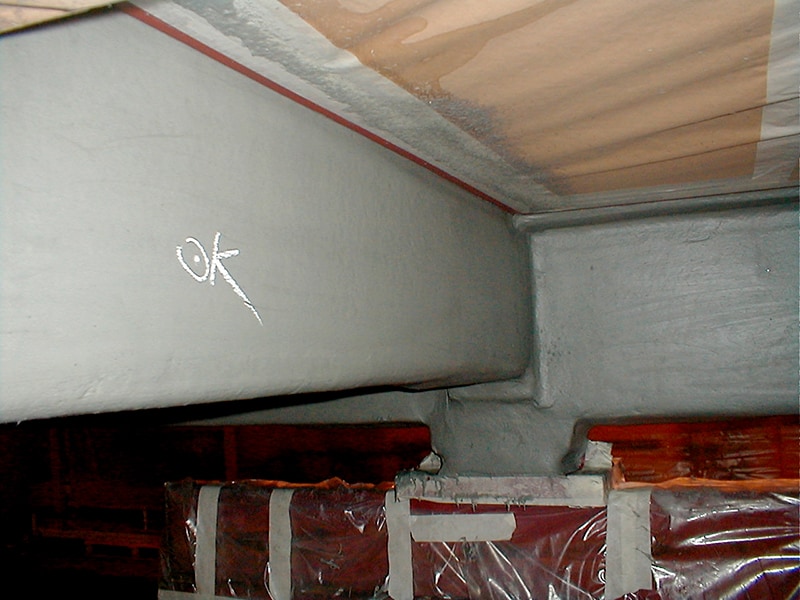
INTUMESCENT COATING TYPES
Intumescent coatings may be grouped into two basic coating types: single component acrylic/vinyl/polyvinyl acetate coatings and high-build plural component epoxy coatings.
Single component coatings may be solvent- or water-based, and are applied in several coats. The time-frame for a complete application may span several days, depending on the recoat time required between coats. After applying multiple intumescent coats, additional time may be needed to allow for full cure of the coating layers before applying any required exterior finish coat. This time period may span from days to weeks depending on the curing requirements of the coating.
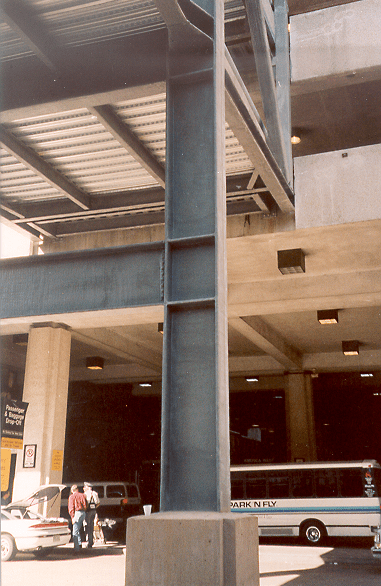
A common method (as specified by the coating manufacturer) for assessing cure is to measure the hardness of the coating with a Durometer test. “Shore D” hardness is the typical test for coatings, and measures the resistance of the coating film to indentation by the Durometer instrument on a scale of 0-100. If the indenter completely penetrates the sample, a reading of 0 is obtained; if no penetration occurs, a reading of 100 results. A hardness value in the range of 40 to 50 is commonly required before applying an exterior topcoat. The hardness value for a fully cured an adequately intumescent coating is typical 70 or higher.
Plural component epoxy fireproofing coatings are high-solids materials, typically applied in one or two applications. Plural spray is a technique that requires specialized equipment used by licensed applicators. These coatings cure very quickly and are typically ready for exterior finish coat application within two days, but they may also require mesh reinforcement, applied between applications of the coating.
The overall time-frame for application of the epoxy intumescents is just a day or two, depending on whether two applications (and mesh) are required. That means the overall application cycle for plural component epoxy coatings is much shorter than that required for the single component coatings.
APPLICATION AND THICKNESS REQUIREMENTS
Another aspect of intumescent coatings that should be considered is the finished appearance. Rather than a completely smooth finish, most intumescent applications result in rougher surface texture or orange peel appearance. The application method(s) can influence the appearance of some coatings — e.g., back rolling after spray application may make the surface smoother. Finish coats can also be applied to affect the final coating system appearance. (As previously noted, any primers or topcoats must be included in the UL approval.)
The thickness required for either single-component or epoxy intumescents may vary widely. The thickness is a function of the physical properties and based on the fire resistance test results. As an example, consider the following generic intumescent coatings for application to structural steel framing for a building structure. (This information is based on manufacturers’ actual published product data for the various coating types.)
As the table shows, the requirements for coating thickness, number of coats and curing time vary widely between the coatings. The curing times required for both recoat time between coats, and until finish coat application (if required for a system), will obviously impact the project duration. In this case, from at least a month for the solvent-based acrylic coating to only a day or two for an epoxy coating.
The comparisons above illustrate how critical it is to fully understand the requirements for a particular intumescent coating. Paying attention to these details will lead to better planning for a project and increase the chances of a successful outcome.
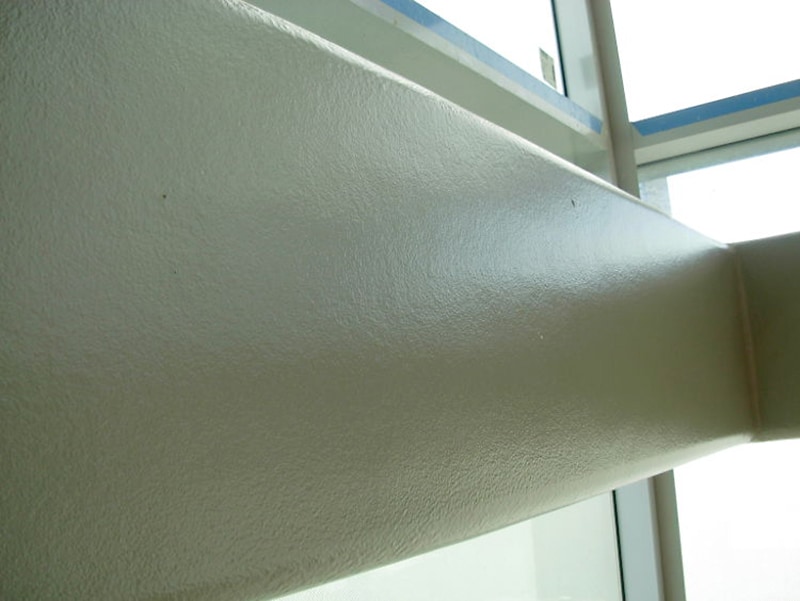
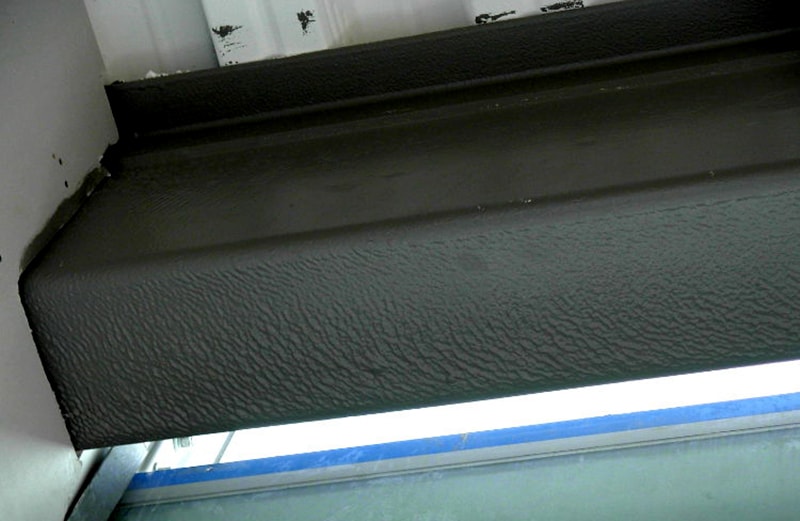
NEW DEVELOPMENTS IN INTUMESCENT COATINGS TECHNOLOGY
New developments for intumescents generally involve coatings that can be applied thinner and that cure faster, while still providing the required level of fire protection. These developments are generally geared toward faster production rates for application of intumescents, whether shop or field applied. Equivalent protection with thinner coats or the ability to apply a heavier build per coat can reduce the number of coats ultimately needed. In the case of some coatings, multiple work days could be eliminated from the project time required. Other improvements involve simpler application, such as installation of coatings without the need for mesh reinforcement in the coating.
Other examples are epoxy intumescents with flexible characteristics, in contrast to the typical rigid nature of these materials. Flexibility can help eliminate the risk of cracking during construction, transportation and in service over a structure’s life. Some intumescents also combine fire protection with insulation properties. Insulation properties would be an important feature for an exterior coating on a tank containing a pressurized, liquefied gas, which must be kept at very low temperatures. When the gas is flammable, such as liquefied natural gas, an insulating coating that is also an intumescent coating would be desired.
Intumescents are coatings with unique properties, but an understanding of the approval types, different generic coating types and various issues involved with application will help make a project successful. D+D
ABOUT THE AUTHOR: Jayson Helsel is a senior consultant with KTA-Tator Inc. He holds a master’s degree in chemical engineering from the University of Michigan, is a licensed professional engineer in several states, an SSPC Protective Coatings Specialist, SSPC Certified Concrete Coatings Inspector and a NACE Certified Coatings Inspector. At KTA, Helsel manages coating projects, performs failure investigations and coating surveys, writes coating specifications and is a regular instructor for KTA coating inspection courses. He previously served as a Lieutenant Commander in the U.S. Coast Guard with experience in marine vessel inspection.
The Article on Intumescent Coatings for fire protection is exhaustive and nicely compiled. Still there are scope for comments:
1. Fire protection of Hydrocarbon Lines and structures, like in Offshore Platforms, with Epoxy Intumescent coatings are essential, more challenging and shall be designed and installed right in the construction stage. This is because Studs are to be fixed for hanging Chicken Mesh or FRP Mesh and blast cleaning is required for application of Epoxy Primer before installing the Intumescent Coating. Epoxy Finish coat, however, can be applied easily both for initial and maintenance coatings.
2. For post operation application of Intumescent Coatings studs are fixed by making small drill. and with adhesives. Priming is managed with SP 3 and Surface Tolerant Epoxy
3. Along with UL 1709 there are equivalent ASTM, ISO, BS test procedures for assessing fire rating.
These are thick coating; for 2 HR fire rating thickness requirements are 18 mm and more. As mentioned applications are plural component with packaged equipment having plural guns and heating arrangement..
4. Total length and area to be coated are most vital and shall be decided judiciously as in case of fire, the temperature at the end of the coated pipe/structures will be high. Escape and fire extinguishing operation will have to be designed in advance.
5. Because of economy Cementacious Fire Proofing Materials are still popular for bulk areas like walls and less essential pipe lines in remote areas. For vital HC lines and structures, walk ways; Epoxy Intumescents are the better answer.