KTA’s Certified Coating Inspector Forum
Volume 4, Issue No. 2 – April 2025
William Corbett, Technical Consultant
AMPP Senior Certified Coating Inspector & Certified Protective Coating Specialist
KTA’s Certified Coating Inspector Forum is designed to provide professional development/continuing education on standards, inspection practices, new instruments, and other topics to help keep certified AMPP and FROSIO coating inspectors current. It represents the views of the author and KTA-Tator, Inc. It may or may not represent the views of AMPP: The Association for Materials Protection & Performance, even though SSPC, NACE, and AMPP standards are frequently referenced in the content.
Introduction
The use of duplex coating systems for long term protection of structural steel is becoming more mainstream in many industries; yet many aspects of specifying, installing, and inspecting duplex coating systems are not widely understood. This edition of the Certified Coating Inspector Forum explains duplex coating systems, lists several industry standards addressing surface preparation and application, and provides an overview of hot dip galvanizing and thermal spray coating processes, including the quality concerns and inspection checkpoints.
What is a Duplex Coating System?
A duplex coating system is generally considered to be the application of a metallic coating such as galvanizing or thermal spray coatings (TSC, also known as metallizing) followed by one or more coats of a powder or liquid-applied paint/coating (see Figure 1). The metallic coating is generally relied upon for galvanic protection of the underlying steel, while the organic coatings (liquid or powder) provide barrier protection (both to the steel and the metallic coating) and aesthetics.
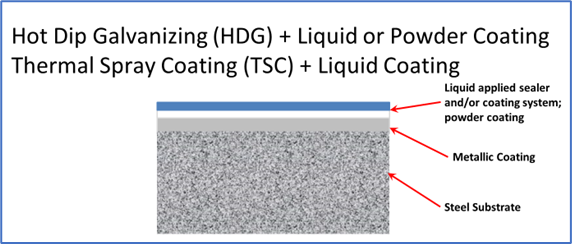
Some would consider a duplex coating system to be, in effect, a “belt & suspenders” approach to corrosion protection since hot dip galvanizing or thermal spray coatings (the “belt” in the corrosion prevention system) can protect steel without liquid or powder-applied coatings (the “suspenders” in the corrosion prevention system). Depending on the prevailing service conditions and desired service life, the application of a liquid or powder coating system may not be necessary. The benefits of liquid or powder coats include imparting color, providing safety indicators (e.g., yellow handrail), improving aesthetics due to elimination of oxidation, protecting the metallic coating in high or low pH environments, and providing additional barrier protection to the substrate.
Industry Standards for Duplex Coating System Applications
There are several industry standards that may be referenced in project specifications pertaining to surface preparation, coating application, and the associated quality control procedures when applying duplex coating systems. Five standards that are specific to hot dip galvanizing and thermal spray coatings are listed below.
- ASTM D6386, Preparation of Zinc (Hot-Dip Galvanized) Coated Iron and Steel Product and Hardware Surfaces for Painting.
- ASTM D7803, Practice for Preparation of Zinc (Hot-Dip Galvanized) Coated Iron and Steel Product and Hardware Surfaces for Powder Coating.
- AASHTO S8.2/SSPC-PA 18, Specification for Application of Thermal Spray Coating Systems to Steel Bridges
- SSPC-CS 23.00, Specification for the Application of Thermal Spray Coatings (Metallizing) of Aluminum, Zinc, and Their Alloys and Composites for the Corrosion Protection of Steel
- SSPC-SP 16, Brush-Off Blast Cleaning of Coated and Uncoated Galvanized Steel, Stainless Steels, and Non-Ferrous Metals
Thermal Spray Coatings: process Overview, quality concerns, and key inspection checkpoints
Process Overview
Thermal spray coatings (TSC) are not surface tolerant. Improper surface preparation (cleanliness and/or surface profile) can result in reduced coating system life or premature failure. Surface preparation is by abrasive blast cleaning using an angular abrasive to generate a 3-5 mil surface profile depth. SSPC-SP 5/NACE No. 1, White Metal Blast is typically specified for surface cleanliness; however, SSPC-SP 10/NACE No. 2, Near-White Metal Blast may be specified for atmospheric (non-immersion) service. Thermal spray quality is also affected by application technique, including equipment amperage and voltage settings, spray distances, and speed/angle of the spray gun.
Application processes include flame spray, arc spray, and plasma spray; the most common application method to industrial structures is arc spray. Flame spray had been used in the past, but it is much less common today.
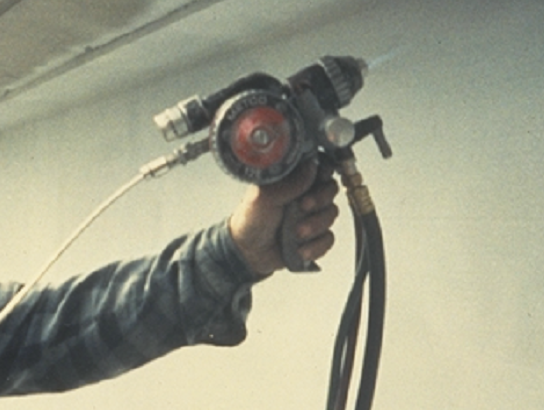
For flame spray, a single wire is fed into an oxygen-acetylene flame, melted, and atomized using clean, dry compressed air, which also propels the metallic particles to the surface (see Photo 1). This process is relatively slow (compared to arc spray) and gun distance to surface should not exceed 4-inches; otherwise, the metal particles will cool prior to reaching the surface, affecting film integrity.
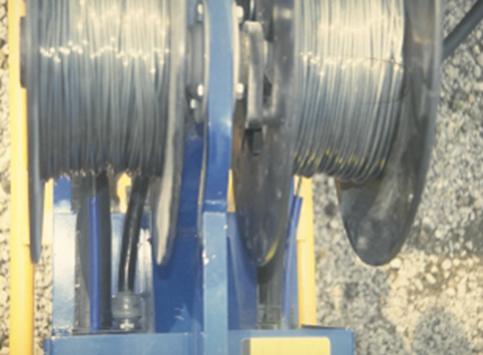
For arc spray, the material is supplied as two wires fed from spools (Photo 2) or large drums.
The arc spray gun is connected to a supply of compressed air and a constant voltage power supply (400-450 amps). The wires are fed through the gun ports, electrically charged, and contact each other. They short out upon contact, causing the wires to melt into metal droplets that are atomized by compressed air and propelled to the surface (Photo 3).

The application rate is dictated by the arc current and gun design; the higher the current, the faster the application rate (provided the voltage is kept reasonably low).
Common wires are Zinc (99.9% purity), Aluminum (99.5% purity), and an 85% Zinc/15% Aluminum alloy. Similar to liquid-applied coatings the wire type selected is based on the service environment.
For plasma spray, the material to be deposited (typically a metal powder) is introduced into a plasma jet created using a plasma torch, where the temperature is nearly 9800°C. The powder is melted and propelled to the substrate. The molten droplets flatten and rapidly solidify upon cooling.
One or more coats of liquid paint are applied to create a duplex system. The first coat is thin and designed to penetrate and seal the porous metallized surface. It should be applied to the TSC before significant oxidation occurs; many specifications require coating within 8-hours of TSC application. Application and curing of liquid-applied coatings is performed according to the coating manufacturer’s product data sheets (PDS) unless the specification contains specific requirements.
Quality Concerns
Quality concerns include porosity, adhesion, flexibility, use on faying surfaces of bolted connections, and properly protecting fasteners.
Porosity: Thermal spray coatings are porous since the metal droplets do not flow together the same as liquid applied coatings. The pores contain air that becomes trapped when the liquid coating is applied to the TSC. A low viscosity sealer or mist coat is frequently required (prior to full coat application) to prevent outgassing and pinholes in subsequent coats. A similar precaution is necessary with inorganic zinc-rich primers due to their inherent porosity.
Adhesion: Thermal spray coatings adhere to prepared steel by mechanical adhesion. As stated previously they are not surface tolerant and require a clean surface and deep, angular surface profile. Shot abrasives do not provide adequate angularity for proper adhesion. In-process pull-off adhesion testing (self-aligning adhesion tester per ASTM D4541) of unsealed metallizing is frequently performed on the actual structure or on companion coupons (when permissible) to verify the minimum adhesion as established by the project specification. SSPC-CS 23.00 establishes minimum adhesion values based on the wire that has been used (see Key Inspection Checkpoints below).
Flexibility: Even though thermal spray coatings are in effect metal, they must exhibit flexibility. The project specification may invoke in-process bend testing using a specific diameter mandrel based on the metallizing thickness (performed on thinner gauge companion coupons prepared concurrently) to verify the inherent flexibility at the specified thickness. Note that SSPC-CS 23.00 lists flexibility testing as non-mandatory, however testing may be invoked by the project specification.
Use on Faying Surfaces (slip-critical bolted connections): Many buildings, bridges and other industrial steel structures contain connection plates/gusset plates to join structural members. In some cases, these bolted connections are deemed slip-critical by the Engineer of Record, meaning the joining surfaces (known as faying surfaces) must exhibit a certain amount of friction between them. The faying surfaces are often coated to prevent corrosion and rust staining. If coated, the coating used on the faying surface must be certified as Class A or Class B slip coefficient, with Class A representing mill scale bearing steel or a coating with a minimum slip coefficient of 0.30, and Class B representing abrasive blast cleaned steel or a coating with a minimum slip coefficient of 0.50. The specific Class required for the project will be included in the design documents. The slip coefficient of each brand of coating proposed for use on faying surfaces must be tested and certified according to Appendix A of the Research Council on Structural Connections (RCSC) Specification for Structural Joints Using High-Strength Bolts.
The Federal Highway Administration (FHWA) conducted a study in 20141 that included slip coefficient and tension creep testing of zinc and 85/15 zinc/aluminum thermal spray coatings, both sealed and unsealed. Both types of wire achieved a Class B slip coefficient when unsealed; however, the sealed TSC did not achieve Class A or B; therefore, when metallizing is applied to the faying surfaces of slip-critical connections, it is important that the metallizing remain uncoated.
Protecting Fasteners: Thermal spray coatings are not used to protect fasteners (i.e., bolts, nuts, washers). The fasteners used in the bolted connections are galvanized, painted, or zinc/aluminum-treated (per ASTM F1136). If hot dip galvanized fasteners are used and are required to be painted, the lubricant on the fasteners (visually evident blue dye) needs to be removed prior to coating. Black bolts are prepared by blast cleaning or SSPC-SP11 Power Tool Cleaning to Bare Metal, and zinc/aluminum treated fasteners should be solvent cleaned prior to painting.
Key Inspection Checkpoints
Like any project involving surface preparation and coating application, there are many inspection check points and hold points that may be invoked by the specification. However, there are five key inspection check points associated with duplex coating systems employing a thermal spray coating (listed below) that are critical.
- Generating the Correct Surface Profile: The surface profile anchors the TSC to the steel and must be angular and 3-5 mils (per specification). If edges were subjected to torch cutting, then grinding to remove surface hardening is critical prior to blast cleaning to achieving the required surface profile.
- Achieving the Required Degree of Surface Cleanliness: Preparing all surfaces to SSPC-SP 5 or SSPC-SP 10 (including indirect requirements for grease/oil removal per SSPC-SP 1, compressed air cleanliness per ASTM D4285, and abrasive cleanliness per ASTM D4940 and D7393) is critical. As stated earlier, TSCs are not surface tolerant.
- Developing a Job Reference Standard (JRS): If SSPC-CS 23.00 is invoked by the project specification, the contractor is required to prepare a JRS, which is an 18” x 18” x ¼” steel plate illustrating (via step-back) the surface preparation, TSC, sealer and coatings (if applicable). The JRS must be inspected prior to production work and is used as a comparative standard during production thermal spray processes.
- Isolating Coating Thickness Layers: Type 2 (electronic) non-destructive coating thickness gages will measure the cumulative thickness of the duplex coating system (TSC and liquid-applied layers). Therefore, baseline thickness readings on the TSC may be required and will vary considerably due to the inherent roughness of the TSC. Because of the variation, SSPC-CS 23.00 invokes SSPC-PA 2, Coating Thickness Restriction Level 4 (spot measurements 80% of the specified minimum and 150% of the maximum are allowed provided the average thickness of the entire area is within the specified range). A special probe/multi-display coating thickness gauge (DeFelsko PosiTector® 6000 with FNDS-1 probe; see Photo 6) may be used to differentiate the TSC thickness from the paint thickness.
- In-process Adhesion Testing: Tensile (pull-off) adhesion performed per ASTM D4541 may be invoked by specification. Triplicate pulls (per location) should be conducted, and the results averaged and compared to the acceptance criteria. The location of break (adhesive, cohesive, glue) and type of adhesion tester used (self-aligning Type III, IV, V, or VI) should be documented. The minimum acceptance criterion in SSPC-CS 23.00 is based on the feedstock (zinc wire: 500 psi [3.45 MPa]; aluminum wire: 1,000 psi [6.89 MPa]; Zinc-Aluminum Alloy: 700 psi [4.83 MPa]).
Hot Dip Galvanizing: Process Overview, Quality Concerns, and Key Inspection Checkpoints
Process Overview
Hot-dip galvanizing (HDG) is a coating that is used to prevent steel from corrosion by galvanic protection. HDG consists of 4 layers as shown in Figure 2:
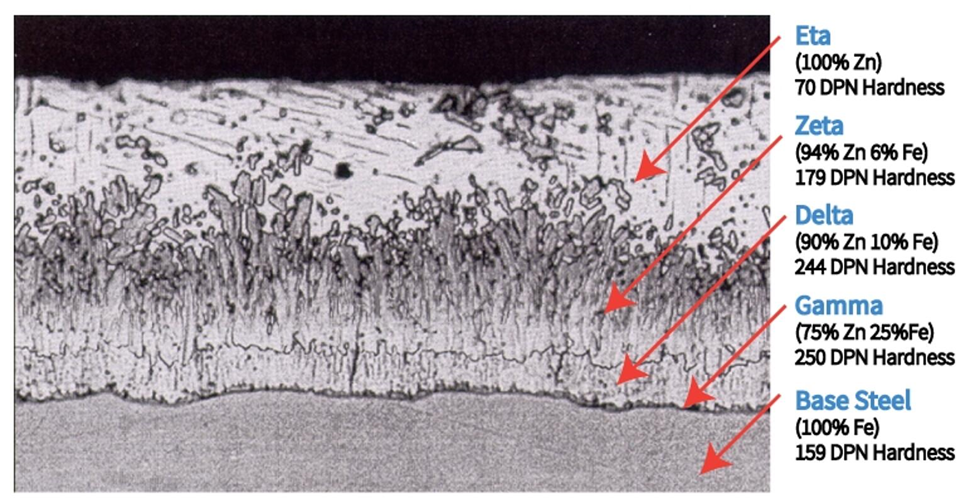
Figure 2 – Four layers of hot-dip galvanizing. Image from American Galvanizers Association, https://galvanizeit.org/hot-dip-galvanizing/what-is-galvanizing/the-hdg-coating
Like most coatings, surface preparation is key to long term performance. Frequently, fabricated steel contains oils and lubricants, rust, mill scale, and other contaminants that can interfere with the galvanizing reaction, so the steel members are chemically cleaned prior to galvanizing. Cleaning typically involves three steps: degreasing, pickling (dilute solution of hydrochloric or sulfuric acid) and fluxing (zinc ammonium chloride solution). In some cases, the steel is abrasive blast cleaned prior to chemical cleaning. This method is sometimes recommended when the steel chemistry is in the reactive range, meaning that the chemistry lies outside the recommended percentage ranges for carbon, phosphorus, manganese, or silicon established in ASTM A385, Standard Practice for Providing High-Quality Zinc Coatings (Hot-Dip). When excesses occur, especially silicon, the zeta layer of the galvanizing can become too thick, reducing, or even eliminating the pure zinc outer layer (Eta). Blast cleaning prior to pickling can sometimes help to reduce the excessive growth of the zeta layer.
The fluxed steel is subsequently dipped in molten zinc (approximately 820 – 850°F [438-454°C]), alloying with the iron and creating an intermetallic system. Parts are cooled after galvanizing by air cooling, quenching the galvanized steel in water to cool parts quickly after galvanizing, or quenching in a passivator such as chromate to slow the formation of zinc oxides on the surface. However, the passivators used in quenching and oil or dust from quench water can interfere with the bond of subsequently applied coatings, so if the galvanizing will be coated the quenching process should not be performed in favor of air cooling. If the steel does get quenched, then preparation per SSPC-SP 16, Brush-off Blast Cleaning of Coated and Uncoated Galvanized Steel, Stainless Steels, and Non-Ferrous Metals is typically required prior to coating. Additional information on surface preparation is provided in the next section.
Once surface preparation is completed, one or more coats of liquid paint are applied to create a duplex system. Application and curing of liquid-applied coatings is performed according to the coating manufacturer’s product data sheets (PDS) unless the specification contains specific requirements that would override the PDS.
Quality Concerns
Quality concerns related to coating HDG include outgassing and determining the degree of surface preparation of the galvanizing prior to coating.
Outgassing of Zinc during Powder Coat Baking: When powder coatings are used, they are commonly applied by electrostatic spray or fluidized bed. Once applied they require baking at relatively high temperatures (350-450°F) for a given duration. These temperatures cause water and air molecules that are trapped in the galvanized coating to out-gas, which produces tiny pinholes in the powder coating (Photo 4). This can be prevented by pre-heating the HDG (at the same temperature) prior to powder coating. This will not harm the galvanizing layer but will eliminate outgassing issues once the powder coating is applied and baked. ASTM D7803, Standard Practice for Preparation of Zinc (Hot-Dip Galvanized) Coated Iron and Steel Product and Hardware Surfaces for Powder Coating addresses this phenomenon.
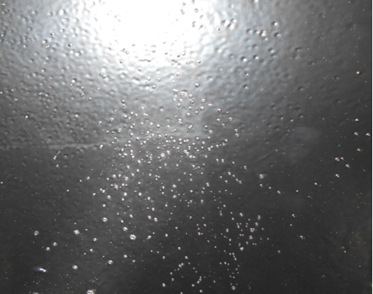
Surface Preparation of Galvanizing Prior to Coating: Almost certainly you have seen paint peeling from galvanized surfaces (Photo 5).
Successfully painting galvanizing means understanding of how galvanizing ages and the degree of surface preparation necessary based on the age of the galvanizing layer
There are generally three conditions of galvanizing: New, partially weathered, and weathered.
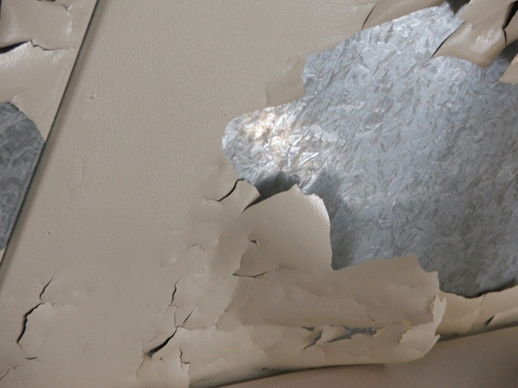
New: Galvanizing that has been exposed to the atmosphere for 48-hours or less.
Partially Weathered: Galvanizing that has been exposed to the atmosphere for two-days to one year.
Weathered: Galvanizing that has been exposed to the atmosphere from one year to total zinc consumption.
The degree of surface preparation required is dependent on the condition of the surface, which is based on the age of the HDG. HDG first forms zinc oxide as it is exposed to the atmosphere. When zinc oxide gets wet (i.e., from rain or condensation) it converts to zinc hydroxide. Both conditions will interfere with coating adhesion. When zinc hydroxide reacts with carbon dioxide in the atmosphere, zinc carbonate forms. Provided the zinc carbonate is intact it can be coated over. The following table provides stepwise guidance on the degree of surface preparation required based on the condition of the HDG.
Surface Preparation Procedures Prior to Painting HDG
Step No. | New Galvanizing | Partially Weathered Galvanizing | Weathered Galvanizing |
1 | Remove protrusions, runs, and drips | Remove chromate conversion coating if present (SSPC-SP 16 or SP 11) | Remove grease, oils per SP 1 |
2 | Remove organic contaminants and chromate (if included with quenching process) | Remove wet storage stain if present | Pressure wash with warm water |
3 | Rinse and dry | Sweep blast or use “clean and etch” product | Remove corrosion (if present (SSPC-SP 16 or SP 11) |
4 | Coat within 48 hours of HDG | Coat as soon as feasible | Coat as soon as feasible |
5 | If >48 hours, prepare per SSPC-SP 16, SSPC-SP 11, or apply zinc phosphate, wash primer, acrylic passivation |
Key Inspection Checkpoints
In addition to the requirements of surface preparation (previously described) there are three special inspection check points associated with duplex coating systems employing hot-dip galvanizing, including isolating coating thickness from HDG thickness, masking slip-critical bolted connections, and protecting fasteners.
Options for Isolating Liquid/Powder Coating Thickness from HDG Thickness: Since the HDG and liquid/powder coatings are both non-magnetic, most traditional Type 2 (electronic) coating thickness gages cannot distinguish one layer from the other. The thickness of the liquid or powder coating can be isolated from the thickness of the galvanizing later by obtaining baseline thickness measurements of the HDG and deducting the average from the total thickness measurements. However, this may not produce accurate data since HDG thickness can vary widely across a given structural element. A special probe/multi-display coating thickness gauge (DeFelsko PosiTector® 6000 with FNDS-1 probe; Photo 6) may be used to differentiate the HDG thickness from the paint thickness.
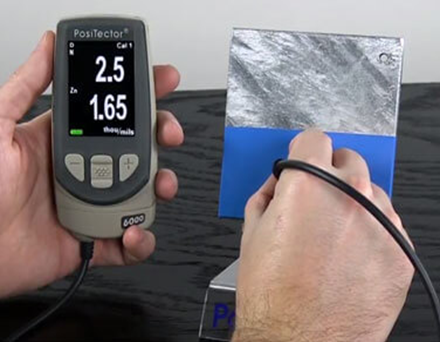
Note that calculating the average galvanizing thickness (prior to liquid/powder coating application) for a structure that is fabricated from different shapes and sizes of steel isn’t recommended, since the thickness of the HDG on the various members will be highly variable. In this case, it is recommended to map the HDG thickness across the entire structure, then measure the combined coating and HDG thickness and deduct the thickness of the HDG mapped to the appropriate steel member to get a fairly accurate paint thickness. Use of the DeFelsko PosiTector® 6000 equipped with the FNDS-1 probe eliminates the need to perform complex mapping.
Use on Faying Surfaces: As discussed earlier, the RCSC categorizes HDG steel as Class A slip coefficient. If Class A slip coefficient is required, it is important to verify that faying surfaces are masked after galvanizing and prior to application of any organic topcoats. If Class B slip coefficient is required, it may be necessary to totally remove the galvanizing and prime the faying surfaces with a coating that has a Class B certification.
Protecting Mechanically Galvanized or HDG Fasteners: While it is not necessary to coat galvanized fasteners, it may be desired for additional barrier protection and/or aesthetics. If fasteners are scheduled to be coated, verify removal of the lubricant (no evidence of color transfer of dye to dry cloth) prior to applying the coating.
Summary
The use of duplex coating systems for long term protection of structural steel is becoming more mainstream in many industries; yet many aspects of specifying, installing, and inspecting duplex coating systems are not widely understood. This edition of the Certified Coating Inspector Forum explained duplex coating systems and provided an overview of hot dip galvanizing and thermal spray coating processes, including the quality concerns and inspection checkpoints.