Introduction
There are a wide range of immersion environments where protective coatings (liquid or powder), sheet materials, or rubber linings may be expected to protect an asset. Some of the environments range from basic water immersion to chemical immersion with perhaps high pressure and elevated temperatures. The most widely protected assets are constructed of concrete and metallic substrates that can range from basic steel structures such as rail cars and storage tanks to nuclear power plants. There are several test methods used to simulate actual service environments. This article focuses on a few ASTM and NACE standard test methods for immersion and one-sided cell testing.
Starting Simple – Distilled Water
One of the more basic environments but arguably one of the most aggressive is distilled water. ASTM D870 “Standard Practice for Testing Water Resistance of Coatings Using Water Immersion” primarily tests coated substrates fully or partially immersed in distilled water. The method subjects the coated substrates to circulating or aerated water at room temperature (23°C), or at slightly elevated temperatures: 32°C, 38°C or 40°C. Depending on the duration of exposure (typically chosen by the material manufacturer), the test panels may be rotated, and the water can be periodically changed. When the exposure time is completed, the coatings are immediately evaluated visually for any physical changes when compared to a non-exposed coated panel. If significant changes are observed, the coatings are allowed a recovery period of 12 to 24 hours, after which the coatings are re-evaluated for physical properties and visual defects.
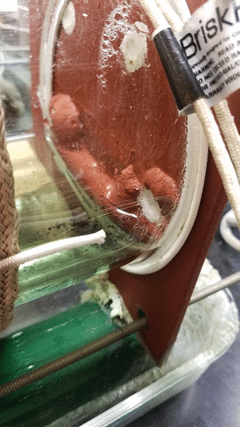
Another method for assessing water resistance is ASTM D7230 “Standard Guide for Evaluating Polymeric Lining Systems for Water Immersion in Coating Service Level III Safety-Related Applications on Metal Substrates.” This method can be used to evaluate a coating product or a lining system for maintenance or new construction. Products include liquid- and paste-grade polymeric materials and are tested on metallic panels. The method covers two different phases of testing: Phase 1 is used to evaluate the permeability of the coating and resistance to water via one-sided cell (Atlas Cell) testing followed by destructive testing. Permeability testing is used to determine how well the coating will behave when exposed to water, while Atlas Cell testing is performed with a temperature gradient to simulate the intended service environment. Phase 2 includes more destructive tests that can be used to help refine the selection process of a coating product.
Getting More Aggressive – Temperature and Pressure Gradients
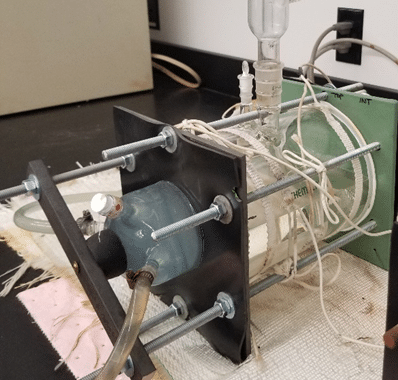
In addition to water immersion, other test methods employ various chemical solutions representative of the conditions seen in pipe or storage vessels (steel or concrete) using the Atlas Cell method. ASTM D6943 “Standard Practice for Immersion Testing of Industrial Protective Coatings and Linings” can be used to evaluate candidate coatings that will be continuously or intermittently exposed to chemical solutions. The chemicals used for the exposure are typically selected based on the anticipated service environment. The standard provides for three different methods of varying temperatures and pressures. Method A (Immersion with No Temperature Gradient) is used to evaluate coatings at a constant temperature under atmospheric pressure using a glass vessel (Atlas Cell) with ports to allow venting and release any pressurization during exposure. The test panels are immersed ⅔ to ¾ into the chemical solution at room temperature for a minimum of 30 days or as agreed upon by the contracting parties. Method B (Immersion with Temperature Gradient) exposes coatings to different temperatures on the panel faces to create a cold wall effect, which is when the interior side is heated, and the exterior is cooled.
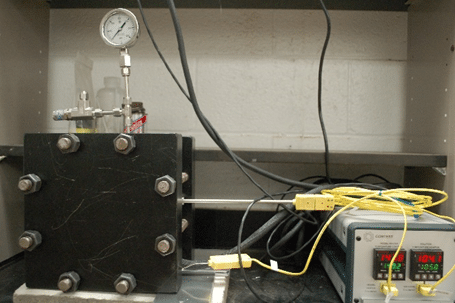
Method C (Immersion Testing at Static Temperature and Elevated Pressure) employs an insulated pressure vessel that has an external heat source capable of exposing the coating to higher temperatures and pressures. Method C also allows for temperature cycling. Typical cyclic exposure times are a minimum of 30 days or continued until failure of the coating. Once the testing is completed for all three methods, the exposed areas of the liquid and vapor phases are examined and evaluated for physical properties including pencil hardness, durometer hardness, tensile adhesion, gloss, and color variations (visually or with a spectrophotometer) as well as any visual defects such as blistering, rusting, lifting, cracking, peeling, or erosion.
A method similar to ASTM D6943 is NACE Standard Test Method TM0174 “Laboratory Methods for the Evaluation of Protective Coatings and Lining Materials on Metallic Substrates in Immersion Services.” TM0174 is designed for liquid or powder protective coatings and linings on metallic substrates. The method does not specifically cover the testing of sheet linings or rubbers on metallic substrates, but the testing can be used as part of the selection process of a lining. Test Method TM0174 is typically performed as one-sided cell and immersion of the completely coated panel. As in ASTM test method D6943, NACE TM0174 has two types of tests, Procedure A and Procedure B, and uses immersion fluids that are similar to the anticipated service environment. Procedure A is similar to ASTM D6943, Methods A and B and encompasses the one-sided cell testing of coated metallic panels and uses similar temperature parameters and gradients. Procedure B uses a resin kettle, which is a chemical reaction vessel to help maintain the required temperatures of the testing, along with the use of a condenser to help retain evaporated solution control and the buildup of pressures. The coatings exposed to both procedures are checked for initial thickness, durometer hardness, and pencil hardness and then re-tested after one-, three- and six-month immersion exposures.
Summary
The variations in coating immersion test methods illustrates the need to customize testing to accurately simulate the chemicals, temperatures, and pressures found in actual service environments. Proper selection of the test method and post exposure evaluation of physical properties (relative to pre-exposure properties) can help ensure field performance and save time and money in testing.
About the Author
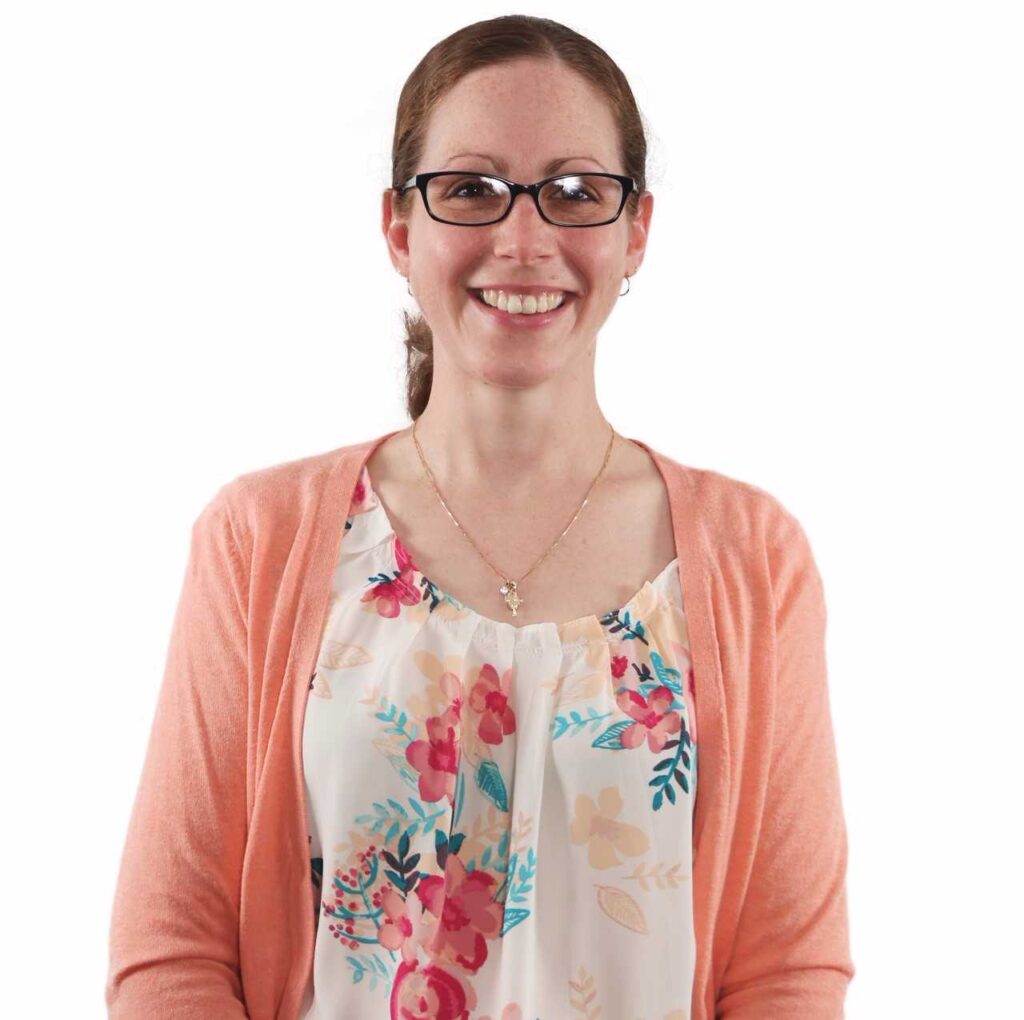
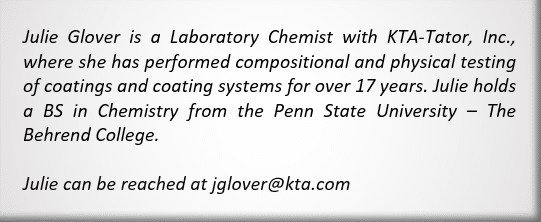
My firm is adopting immersion testing for our upcoming project. I appreciate how you emphasise the necessity for the chemical solution to be at room temperature for at least 30 days. I believe that maintaining the temperature is difficult without good laboratory planning. I’ll work with the layout laboratory specialists to ensure that our project is completed effectively.