SSPC-PA 2, Procedure for Determining Conformance to Dry Coating Thickness Requirements provides a frequency for obtaining coating thickness readings based on areas of 100 square feet. This frequency can be applied to I-beams painted in the shop or field; however, the total square footage of all beams coated during the shift must be calculated, and surfaces like the undersides of the top flange and bottom flange must also be measured even though they may be more difficult to access.
SSPC-PA 2 contains several appendices that are nonmandatory but may be invoked by contract. Two of the appendices apply to measuring coating thickness on steel beams and girders (Appendix 2) and laydowns of beams, structural steel, and miscellaneous parts after shop coating (Appendix 3). This article provides clarification on these two appendices, along with examples of each.
SSPC-PA 2, Appendix 2 – Steel Beams and Girders
Appendix 2 of SSPC-PA 2 provides a frequency for measuring coating thickness on steel beams or girders. Two approaches for taking the readings on each beam are described – a full determination and a sample determination, but the standard does not specifically indicate how many beams should be measured.
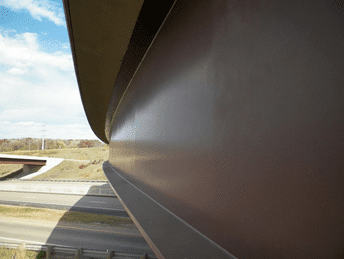
Full Determination: For a full determination, the total length of the beam is divided into five equal sections. For example, a beam that is 75 feet long is divided into five 15-foot sections, while a beam that is 100 feet long is divided into five 20-foot sections.
For steel beams fabricated with a web that is greater than or equal to 36” in height, one spot measurement is acquired in each of 14 locations per section (see Figure 2), for a total of 70 spot measurements for the entire beam. Each spot measurement is the average of at least three gage readings. The measurement locations on stiffeners are arbitrarily selected since the number of stiffeners will vary. The readings on stiffeners are in addition to the 70 readings per section, but a specific number of readings on stiffeners is not stipulated.
For steel beams fabricated with a web that is less than 36” in height, one spot measurement is acquired in each of 12 locations per section (see Figure 2), for a total of 60 spot measurements. Again, each spot measurement is the average of at least three gage readings, and the measurement locations on stiffeners are arbitrarily selected.
Figure 2 illustrates the locations of the spot measurements for a full determination based on the two web sizes. If the flange is too thin to be able to accurately measure the edge or toe, the edge/toe measurements can be dropped (Spots 2, 6, 8 and 12 in Figure 2).the top of the top flange (Spot 1 in Figure 2) may not be accessible in the field if it’s embedded in concrete, or may not be required to be fully coated in the shop (e.g., it may be painted with the a zinc primer only, so readings of the remaining coats are not applicable). For webs greater than or equal to 36” in height two readings are taken on the web (high and low, designated as 4a, 4b, and 10a, 10b in the right example in Figure 2. For smaller webs, only one reading (4 and 10) is required on the web per the left example.
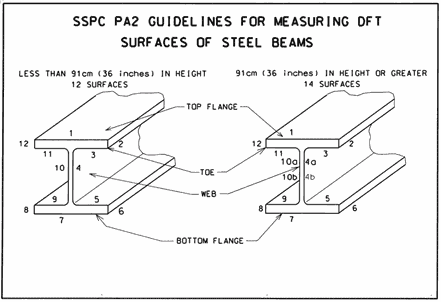
For the Full Determination, individual gage readings averaged to determine the Spot Measurement are unrestricted meaning the readings can be any value; but the tolerance of each of the Spot Measurements is per Coating Thickness Restriction Level 3 (unless otherwise specified), which is 80% of the minimum specified thickness and 120% of the maximum specified thickness. The average of all the Spot Measurements must conform to the specified thickness range. For example, if the specification is 8 to 12 mils, the individual gage readings can be any number, the spot readings (average of 3 gage readings) must be no less than 6.4 mils (80% of 8 mils), nor greater than 14.4 mils (120% of 12 mils), provided the average thickness of the entire beam is 8 to 12 mils.
Sample Determination: The sample determination is based on two lengths of steel beams – those that are less than 20 feet and those that range from 20 feet up to 60 feet. For beams up to 20 feet in length, two randomly distributed spot measurements are obtained on each of the 12 surfaces shown in Figure 2 (8 surfaces if the flange edges are not measured). A total of 24 spot measurements are acquired (16 if the toe is not measured). Each spot measurement is the average of at least 3 gage readings taken within a 1.5-inch diameter circle. Individual gage readings are unrestricted; however, each spot measurement and the overall average of the entire beam must conform to the specified coating thickness range (i.e., Coating Thickness Restriction Level 1). This is an important distinction between a full and sample determination. There is no additional allowable tolerance for the spot measurements beyond the specified thickness range.
For beams from 20 feet up to 60 feet in length, three randomly distributed spot measurements are obtained on each of the 12 surfaces shown earlier (8 surfaces if the toe [flange edges] is not measured). A total of 36 spot measurements are acquired (24 if the toe is not measured). Each spot measurement is the average of at least 3 gage readings taken within a 1.5-inch diameter circle. Individual gage readings are unrestricted; each spot measurement and the overall average of the entire beam must conform to the specified coating thickness range (i.e., Coating Thickness Restriction Level 1). That is, there is no additional allowable tolerance for the spot measurements beyond the specified thickness range when a sample determination is specified.
SSPC-PA 2, Appendix 3 – Steel Members in a Laydown Area
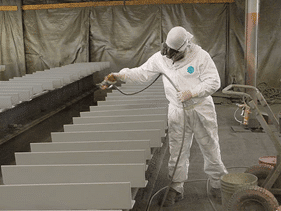
Appendix 3 of SSPC-PA 2 describes a process for measuring coating thickness on laydowns in a shop. A laydown is considered a group of steel members laid down to be coated in one shift by a single applicator. A Full Determination or Sample Determination can be performed on the coated beams. Each of these procedures was described earlier. Again, the standard does not specifically indicate how many members should be measured.
For inspection of a laydown, the Quality Control inspector should first make a visual survey to detect areas with obvious defects, such as poor coverage, and ask the applicator to correct as necessary. Subsequently a Full or Sample Determination can be conducted as specified or desired.
Frequently, miscellaneous parts are coated concurrently with the beams. Full and Sample Determinations can also be performed on the miscellaneous parts, as described below.
For a Full Determination of Miscellaneous Parts, one spot measurement should be obtained on each surface of the part (each spot measurement is the average of a minimum of three gage readings). If the part has fewer than five surfaces, such as an angle, multiple spot measurements should be obtained on the larger surfaces to bring the total to five. If the total area of the part is over 100 square feet, 5 spot measurements randomly distributed over the part should be obtained for each 100 square feet, or portion thereof.
For a Sample Determination of Miscellaneous Parts, three spot measurements should be obtained, randomly distributed on the part (each spot measurement is the average of a minimum of three gage readings). Each spot measurement must conform to the specified DFT.
If any spot measurement falls outside the specified range, then additional measurements may be made to define the magnitude of non-conforming area.
While SSPC-PA 2 does not address the number of beams or parts to receive a full DFT determination versus the number to receive a sample DFT determination in a laydown, it may be specified by the contract documents. For example, to help ensure the consistency of the applicator, a specification may require a full DFT determination on a piece painted near the beginning of the shift, near the middle of the shift, and near the end of the shift, and require a sample DFT determination on every third piece. Alternatively, a contractor can invoke this same approach as part of their standard QC process.
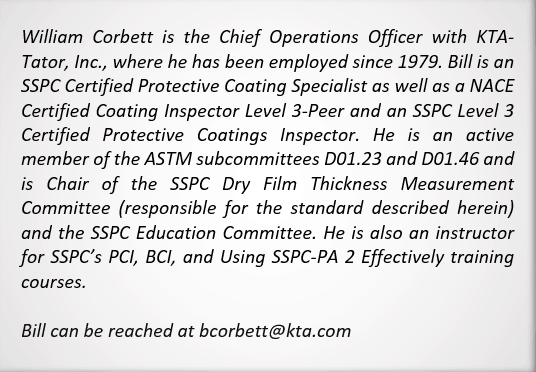
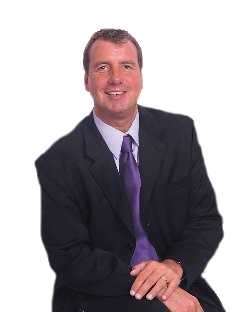