Every fall, OSHA publishes a list of the Top 10 most frequently cited standards from the previous fiscal year (October 1 through September 30), as well as the Top 5 sections from each of the most frequently cited standards that resulted in the majority of the citations. For the past 10 years, the annual rankings may have shifted slightly, but the Top 10 most frequently cited OSHA standards have not changed at all over the past 10 years. The chart below provides a tabular summary of the Top 10 most frequently cited OSHA standards over the past 10 years.
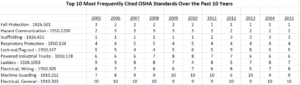
This table should tell us two things:
1) If OSHA visits your job site, you should expect that compliance with at least some of these standards will be investigated
2) these Top 10 standards likely make the list each year because they continue to result in non-compliance violations in the field.
So what does this ten year look-back at the Top 10 most frequently cited OSHA standards mean to the consultants and contractors who operate in the industrial coatings arena? In short, it means that corporate safety and health policies and procedures should be reviewed annually for compliance with these standards, and any safety and health emphasis for the coming year should revolve around, or at least in some way address the requirements of these standards. For those folks that perform the majority of their work in the field, emphasis should be placed on compliance with the fall protection, scaffolding, and ladders standards, particularly the implementation, training, and content of the written compliance programs related to these standards. Similarly, for those whose work is performed primarily in a shop environment, attention should be directed to compliance with the machine guarding, powered industrial trucks, and electrical standards. And independent of whether your operations are conducted in the shop or field, compliance with the OSHA lock-out/tag-out, respiratory protection and hazard communication standards should be continuously evaluated, particularly use, training, and the content of written compliance programs related to these standards.
Regardless of whether work is performed in the shop or field, professionals responsible for implementing safety and health practices in the industrial coatings industry should focus on the written compliance programs, training, and most importantly implementation of policies and procedures related to the above listed Top 10 standards.
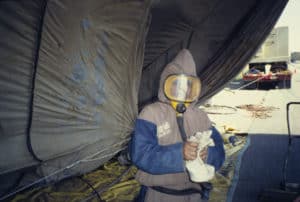
Written Compliance Programs on OSHA
As described above, OSHA provides a list of the top 5 sections that were responsible for the majority of the violations within each of the Top 10 most frequently cited standards. A review of these top 5 sections for the standards that made up the top 10 most frequently cited OSHA standards over the past 10 years indicates that the establishment and implementation of written safety and health programs, or more importantly the lack thereof, is consistently a major cause for citation, particularly related to the OSHA hazard communication, respiratory protection, and lock-out/tag-out standards.
Written safety and health programs obviously need to be current, but just as important, comprehensive. Someone within the organization should have responsibility for staying current with the OSHA regulatory environment, including changes to existing standards as well as the enactment of new standards for which compliance may be required. To verify that programs are current, annual reviews by the Corporate Health and Safety Officer or executive management should be performed and documented. It might be advisable (and actually required by the SSPC QP1 certification program) to have a Certified Safety Professional perform a comprehensive review of the written program every 3 years to ensure it is both current and technically accurate. Reviews should focus on ensuring that the program is in compliance with not only existing OSHA standards and the Top 10 most frequently cited standards, but any comprehensive health standards for which employees may have exposure. The review should also consider whether the business has expanded to include new service offerings or new market sectors since the last review of the program. Entering into new service offerings or market sectors may require compliance with an entirely different set of OSHA standards that aren’t addressed in the current program.
Training
A review of the top 5 sections for the standards that made up the top 10 most frequently cited OSHA standards over the past 10 years indicates that the lack of effective training is consistently a major cause for citations, particularly related to the OSHA hazard communication and lock-out/tag-out standards.
So what exactly does effective training look like? Effective training should include:
- Materials that are presented in a way that support adult learning styles – short, concise units
- SMART learning outcomes – specific, measurable, achievable, relevant, time-stated
- Assessments to verify that the learning outcomes were achieved – oral, written, practical exams
- Interactive opportunity for participant engagement – hands on workshops and demonstrations
- Self-directed learning exercises (i.e., identify deficiencies in example respirators)
Once the development of effective training programs has been verified or completed, administrative issues related to training delivery should be addressed or evaluated. First, someone within the organization should verify that existing employees are receiving training at the required frequency, that new employees attend mandatory training, and that participation is documented. Second, someone within the organization should verify that all current employees have received training in the appropriate subject matter – for all of the Top 10 standards listed above as well as for any other hazards to which employees may be exposed.
Implementation of Compliance Programs/Training
The bulk of the violations in the OSHA Top 10 most cited standards were related to issues of non-compliance in the field. The question that should then be asked is – why are these field violations occurring? Is it because concepts presented in the training courses are not being retained? Or is it because written safety and health programs are just a document collecting dust on a shelf? The primary responsibility of evaluating field implementation lies with the Site Supervisor or Foreman. These individuals have their boots on the ground and should be the daily eyes and ears related to safety and health compliance. A second, and equally important evaluation method of assessing implementation is for frequent site visits (both scheduled and unannounced) by a Corporate Safety and Health Officer or by an independent 3rd party safety and health consultant. Regardless of who evaluates field implementation, the assessments should include evaluations of work practices for compliance with corporate safety and health policies as well as any applicable OSHA regulations and contractual or specification requirements. As with training, the results of any site visits should be well documented and reported to management. Inadequate implementation of company safety and health policies and procedures may indicate that training was ineffective in changing behaviors, and the use of a more effective instructional method may be required. Regardless, for training and written compliance programs to be effective, corporate management needs to be actively engaged in the process, and promote a “safety first” culture. Frequent visibility of the Corporate Safety and Health Officer at job sites is a great start, but annual training offerings (that are truly effective in changing behaviors) or semi-annual reviews of written compliance programs are giant steps towards developing a safety culture and minimizing the opportunity for OSHA violations.