KTA’s Certified Coating Inspector Forum Issue No. 4
KTA’s Certified Coating Inspector Forum is designed to provide professional development/continuing education on standards, inspection practices, new instruments, and other topics to help keep certified AMPP and FROSIO coating inspectors current. It represents the views of the author and KTA-Tator, Inc. It may or may not represent the views of AMPP: The Association for Materials Protection & Performance, even though SSPC, NACE, and AMPP standards are frequently referenced in the content.
When striping or stripe coating is specified, a coatings inspector is responsible for verifying it is performed properly. This article describes the general content of an SSPC guide for stripe coating, defines stripe coat, discusses the value of stripe coating, where it may fall in the coating application sequence, application methods, dry versus wet striping, and the inspector’s role.
SSPC Guide 11, Protecting Corners, Edges, Crevices, and Irregular Steel Geometries by Stripe Coating, published by AMPP: The Association for Materials Protection & Performance is a valuable resource for specifiers in understanding the importance of stripe coating irregular surfaces. It describes the challenges associated with protecting sharp edges, outside corners, crevices, welds, and fasteners where coating failures and corrosion often begin prematurely due to reduced coating coverage or thickness. The document provides guidance on preparing outside corners and sharp edges, the use of coatings with edge-retention properties, what coats to stripe, areas to stripe, how to stripe (application method) and the advantages and limitations of each method, when to stripe (before or after full coat application, and the associated advantages and limitations), and controlling stripe coat thickness. The Guide contains sample language to assist specifiers with invoking stripe coating on their projects and contains nine color images of configurations/geometries that may benefit from stripe coats.
According to SSPC Guide 11, a “stripe coat” is a layer of coating applied to specific areas such as edges, welds, outside corners, bolt heads and threads, nuts, and crevices, to provide additional barrier protection. The stripe coat may be applied either before or after a layer of coating (often called a “full coat”) is applied over the entire surface being coated. The practice of applying a stripe coat is frequently referred to as “striping.”
Stripe coating or striping is frequently invoked by specification on tank, vessel, and rail tank car interiors, but is also specified on structures/surfaces exposed to atmospheric conditions such as bridges and tank exteriors to prevent rust staining from welds, crevices and fasteners that are difficult to protect long term. As a trained/certified inspector, never assume stripe coating is or is not required by specification. There is no industry standard requiring it, so if it is invoked, it is done so by the specifier, perhaps with guidance from the coating manufacturer. Also, the specific coating layer(s) to stripe (e.g., primer, mid-coat, finish coat, or multiple coats) should be specified. If it isn’t, ask for clarification at the pre-job meeting.
The Value of Stripe Coating
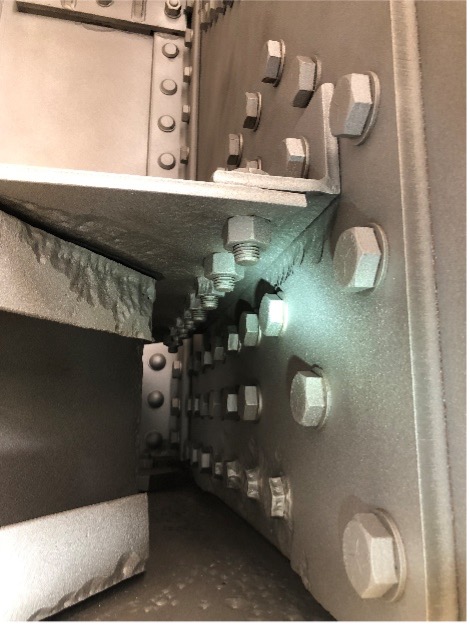
Generally speaking, high-performance industrial coating systems are capable of long-term protection of flat surfaces, provided the surfaces are properly prepared and the coating system is properly applied. However, irregular geometries such as those cited earlier (and depicted, left) can be challenging to protect, as the coating may temporarily bridge crevices and appear to cover edges while being applied, but frequently draws thin on these surfaces as the coating shrinks during curing. The best way to protect these irregular surfaces is to assure that the thickness of the coating (the barrier) between the substrate and the environment is the same as the thickness on the flat surfaces. But applying a coating thicker on edges, for example, to overcome the shrinking the occurs has its own inherent problems, including potential solvent entrapment, cracking, and delamination. Stripe coating or striping helps to overcome these concerns while providing additional barrier protection to the configured surfaces. The stripe coats are applied as separate layers (separate from the full coat application), reducing the potential for solvent entrapment and/or performance issues.
Dry Versus Wet Striping
The terminology “dry and wet striping” can be misleading. In this case, dry versus wet is related to the degree of dryness or curing of the stripe coat prior to full coat application, not the application method itself. Wet stripe coating is arguably more common. In this case, the stripe coat is applied and allowed to dry for 10-15 minutes prior to application of the full coat. So, a solvent flash-off time is allowed, but the coating will likely still be tacky. The same applicator may stripe an area, then come back with the full coat 15 minutes later. Alternatively, one applicator may apply the stripe coat, and a second applicator may follow with the full coat application. This “wet-on-wet” approach is often considered more cost-effective and less labor intensive than dry striping. It also saves time over dry striping.
Dry striping is where the stripe coat is applied and allowed the full dry time prior to application of the full coat. When striping the primer, unless dehumidification is employed, the stripe coat is often applied after the prepared surfaces have received a full coat of primer, so that the blast cleanliness is not lost. Striping of subsequent coats may be before or after the application of the full coat.
The inspector should gain clarification if the specification does not delineate between wet and dry striping.
Where Striping May Fall in the Coating Application Sequence
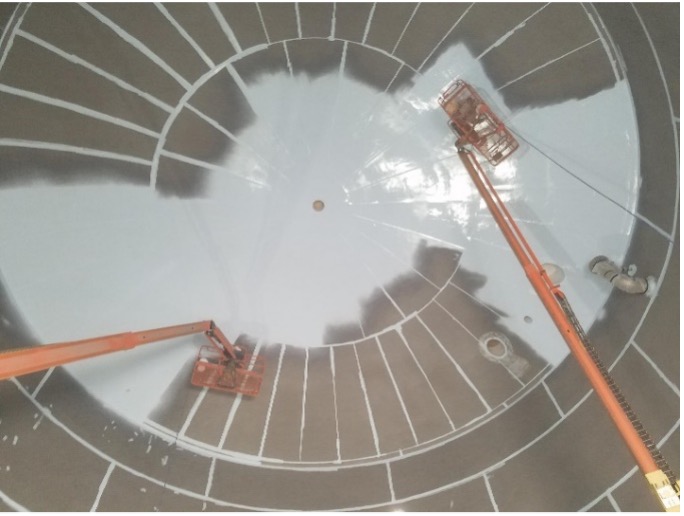
As indicated above, application of a stripe coat may be done before or after application of the full coat. If a stripe coat of the primer is specified, and dry striping is specified, it may be advantageous to apply it after the full coat, so the prepared, uncoated steel surfaces don’t rust back.
A typical sequence for a 3-coat system may be: 1) Apply a full coat of primer; 2) Apply a stripe coat of primer; 3) apply a stripe and full coat of mid-coat; 4) Apply the finish coat. While the finish coat may also include a stripe coat, it may not be aesthetically pleasing and may be eliminated by the specifier.
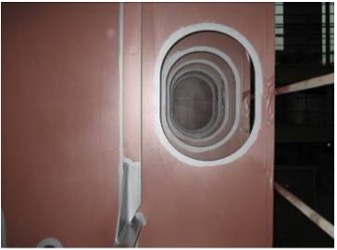
However, stripe coating of ballast tanks in ships frequently entails the application of three stripe coats and three full coats (effectively 6 coats on edges and welds) since seawater is often used as ballast and is highly corrosive.
The dry stripe coat should always contrast the color of the underlying surface or coating layer since inspection of the stripe coat is often done visually. For wet striping, the same color is typically used, but if done before the full coat is applied, the stripe coat will typically contrast with the underlying coat. Inspection of stripe coat application is described later in this article.
Stripe Coat Application Methods
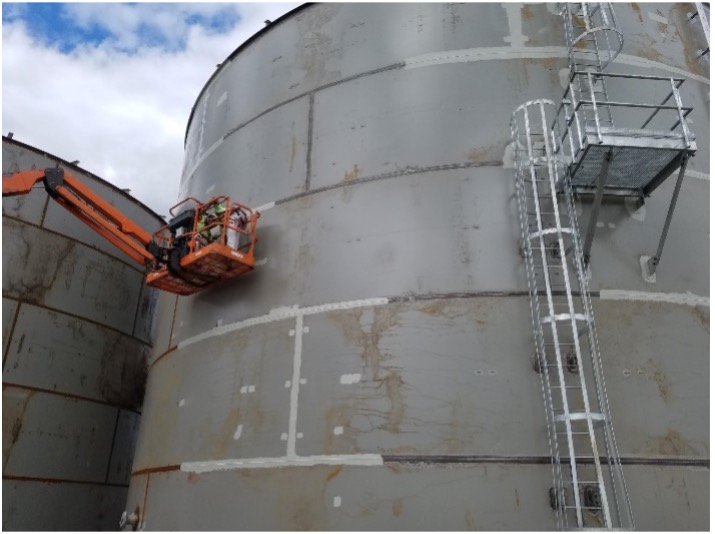
Stripe coats may be applied by brush or spray. In some cases, the contractor may elect to spray and back-brush to speed-up the process and to work the coating into crevices and around fasteners.
Brush striping corners and edges can be challenging, as the brush may pull the coating away from the edges during application, rather than build it up. While spray striping is faster, there is a tendency to skip/miss areas, particularly crevices and fasteners. This is where the use of back brushing is beneficial. There is also the potential for overspray on adjacent surfaces when applying a stripe coat by spray. Spray tip fan width selection is critical in this case. Narrower is better.
The Inspector’s Role
The inspection checkpoints associated the stripe coat application are similar to full coat applications, including measurement of ambient conditions and surface temperature, correct materials, batch/lot no. recording, mixing and thinning, and pot life monitoring. Most stripe coat application inspection is visual for coverage and continuity, which is why the underlying surface should be contrasting color. When wet striping, the inspector needs to be present during application to verify that the stripe coat has been applied. After the full coat is installed, it can be difficult to easily confirm that the stripe coat is present everywhere. Monitoring of dry time may be required if dry striping is specified. The thickness of the stripe coat is difficult to control (particularly when applied by brush); however, for practical purposes it should be the same thickness as a full coat and is often based on the skill of the applicator and their use of a wet film thickness (WFT) gage. However, notch gages cannot provide reliable WFT readings on irregular surfaces (welds, fasteners, etc.) and cannot be used on edges, so the readings must be taken immediately adjacent to these surfaces. The total (cumulative) dry film thickness (DFT) of the stripe coat and full should be measured. Even when dry striping is often unnecessary to measure the DFT of the stripe coat alone. Instead, the inspection is for visual coverage. Leeway on maximum thickness of the stripe coat plus full coat should be allowed within 2-inches of an edge or 1-inch of a weld. Project conflicts can be avoided if thickness requirements at or near the stripe coat and any allowed deviation from specified minimum and maximum DFT thickness requirements are clearly stated in the project specification and/or discussed during the pre-job conference because it is inevitable that, to achieve adequate coverage of the edge, the thickness of the coating immediately surrounding the edge will be heavier. |
Summary
Striping or stripe coating can help extend the life of a structure by providing corrosion protection of irregular surfaces like edges, welds, outside corners, bolt heads and threads, nuts, and crevices. When invoked by specification, the coatings inspector is responsible for verifying striping is sequenced correctly and completed. This article described the general content of SSPC Guide 11, defined stripe coat, discussed the value of stripe coating, where it may fall in the coating application sequence, application methods, dry versus wet striping, and the inspector’s role.