Introduction – Hot dip galvanizing (HDG) of iron and steel results in a durable layer of corrosion protection that often exceeds the performance of liquid applied coatings. But despite the metallurgical reaction that results in an alloying of the molten zinc with the iron of the underlying substrate, the galvanizing layer can be susceptible to delamination, cracking, and peeling, not unlike the problems encountered with liquid-applied coatings. Challenges to the integrity of the galvanizing layer are often related to the chemistry of the steel being galvanized. This article addresses how the chemistry of the steel can affect the quality of the galvanizing and ways to mitigate the difficulties associated with HDG of reactive steel.
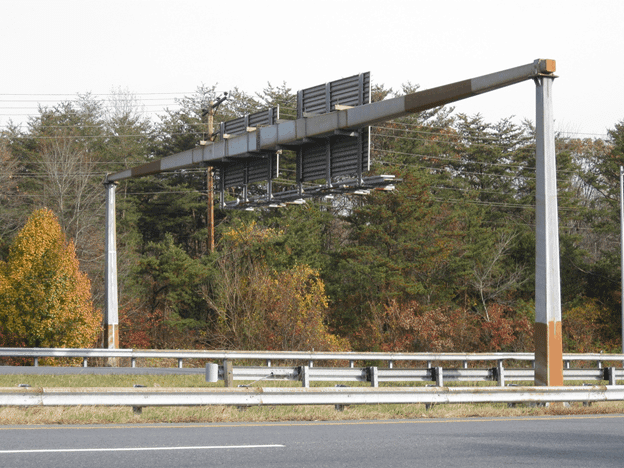
Chemistry Counts – HDG consists of 4 layers as shown in Figure 1: Eta, Zeta, Delta, and Gamma. The layers are distinguished by their relative percentages of zinc and iron, ranging from 100% zinc in the outermost layer (Eta) to 75% zinc/25% iron closest to the steel substrate (Gamma).
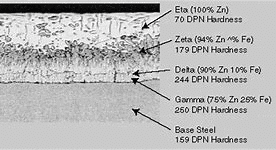
The outermost Eta layer of an HDG coating often has a shiny, metallic “spangle” appearance. An HDG coating that appears dull grey likely lacks the pure zinc topmost layer, and instead, the top layer is an alloy of zinc and iron (the zeta layer). The latter is typically the result of galvanizing steel that is classified as reactive, meaning that the steel chemistry lies outside the following boundaries for galvanizing as recommended by ASTM A385, Standard Practice for Providing High-Quality Zinc Coatings (Hot-Dip):
- Levels of carbon less than 0.25%
- Phosphorus less than 0.04%
- Manganese less than 1.3%
- Silicon levels less than 0.04% or between 0.14% and 0.24%
The structure of the galvanizing layer is a direct result of the chemistry of the underlying steel. The zinc-iron alloy portion of the HDG often represents 50-70% of the total HDG thickness for most hot-rolled steels1, however when galvanizing reactive steel, the alloyed layer can represent an even greater portion, even up to 100%. Of the four elements listed above, silicon has the most significant effect on the formation and composition of the galvanizing layer, so if it is excessive, the quality of the galvanizing can be compromised due to the rapid growth and increased thickness of the zeta layer. Even if the steel chemistry is held within the recommendations of ASTM A385, a high-quality HDG coating is not guaranteed. Material Test Reports should be reviewed to understand the specific chemistry of the pieces. It can also be helpful to galvanize test pieces to evaluate the galvanizing process being used. Even then, it must be recognized that galvanizing a test piece is not a guarantee that the same process will be successful for every production run as the chemistry of the production pieces may vary.
Corrosion of Galvanizing – Whether the steel is reactive or non-reactive, corrosion products (white zinc salts) start to form on a zinc surface as soon as it is exposed to the environment as the zinc reacts with atmospheric oxygen, carbon dioxide and water. Generally, the initial zinc compounds that are formed are water soluble, porous, and loosely adhered to the surface. Over time, these compounds are typically converted to a tightly adherent, water insoluble film that serves to protect the zinc surface from further corrosion. However, when the environment exposes the zinc to moisture/water very frequently, the conversion to a tightly adherent film does not occur, and the zinc continues to corrode, eventually consuming the zinc and allowing corrosion of the steel to propagate (red corrosion). These traditional concerns for all galvanizing are compounded when an HDG layer is excessively thick as can be the case with reactive steel, as the galvanizing is also subject to accumulating internal and external stresses, leading to disbonding. In this case, corrosion of the steel occurs more rapidly because the thickness of the zinc is greatly reduced.
Reactive Steel and Potential for HDG Delamination – Both shiny and dull galvanizing coatings provide the same level of corrosion protection initially, because performance is based on the thickness of the coating layer. But rapid growth of the zeta layer is often difficult to control when galvanizing reactive steel, and the result can be an excessively thick coating that is brittle with poor cohesive strength.
Delamination (Flaking) – While delamination or flaking of an HDG coating may seem highly unlikely since the alloyed layers (zeta, delta, and gamma) undergo a chemical reaction resulting in a metallurgical bond and a highly abrasion-resistant film, delamination does occur, especially with reactive steel. Flaking occurs when 3 of the 4 galvanizing layers detach from the steel, often when the zinc thickness exceeds 10 mils, which renders it more brittle. The flaking form of delamination can occur as a result of thermal gradients and other external stresses that reduce adhesion, which are also intensified when the HDG is excessively thick. When delamination occurs, the thickness of the remaining galvanizing (the gamma layer) is inadequate to provide adequate protection of the steel. If the galvanized members are already in place, the only option to improve protection when delamination occurs is to coat the galvanizing with a liquid coating system.
Peeling – Peeling occurs when the outer free zinc layer separates from the intermetallic layers. The remaining thickness is in the range of 2 to 6 mils. Peeling can occur when newly galvanized steel cools extremely slowly or if the steel is exposed to high temperatures (>400°F) for prolonged periods2. In the case of peeling, the remaining galvanizing may be thick enough to provide protection of the steel. It should be compared with the values in ASTM A123, but the addition of a liquid coating should also be considered.
Examples of locations particularly susceptible to corrosion or deterioration of the galvanizing after installation include the below-deck structural steel of a bridge which is an aggressive environment due to frequent water and moisture intrusion at weep holes, expansions, and seams of adjoining deck panels.
Controlling the thickness of the galvanizing layer is critical to maintaining corrosion protection through the life expectancy of the coating. It is this lack of good thickness control when reactive steel is galvanized that is the heart of the problem.
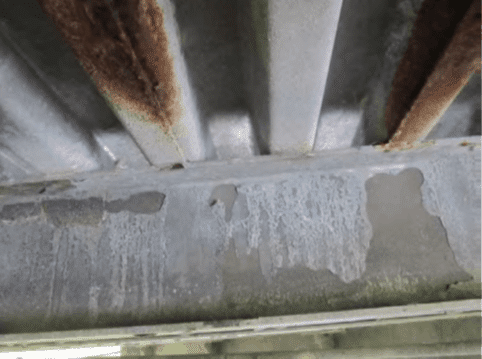
Controlling the Thickness of the Alloyed Zeta Layer – The thickness of the alloyed layer (zeta) is influenced by steel chemistry, reaction time, and the temperature and chemistry of the molten zinc bath. If it is known in advance that the steel is reactive, steps can be taken to mitigate that potential for excessive thickness by limiting the amount of time the member is immersed in the kettle, decreasing the kettle temperature, and blast cleaning the steel before pickling and dipping.
Blast Cleaning – Since the growth of the alloyed layers occurs perpendicular to the steel surface, it is possible to control the thickness of this layer when galvanizing reactive steel by blast cleaning. Creation of a jagged profile will cause these zeta crystals to grow into each other and thus will limit their height. Ironically, abrasive blasting of non-reactive steel can have the opposite effect and increase coating film build because the profile creates more surface area for the molten zinc to react with, and the alloyed layer crystals push up and against each other.
Over-pickling – As an alternative to blast cleaning, a rough profile can also be produced by over-pickling in sulfuric acid.
A complication with using the above methods of mitigation is when fabricated members contain elements that are both reactive and non-reactive.
Thickness of the Pure Zinc Eta Layer – The thickness of the pure zinc layer, unlike the alloys, is limited and is not as affected by immersion time. The pure zinc layer is affected by the cooling rate of the steel and galvanizing. but can also be influenced by drainage or wiping of the HDG layer. Geometry of the member can complicate the rate of drainage and may result in areas of thicker coating, but sufficient temperature to allow good drainage upon withdrawal from the kettle can alleviate some drainage issues. However, increased temperature can also have an adverse effect because alloying of the lower layers can continue beyond removal from the kettle if the steel surface is hot enough, consuming the outer eta layer. “Browning” can occur when the iron in the intermetallic layer reacts with the environment. Although the aesthetics may be compromised, corrosion protection of the steel is still provided.
Conclusion – The quality of an HDG coating is essential to maintaining proper corrosion protection. Although ASTM A123 does not reference upper limits on galvanizing thickness, a heavy HDG film is subject to delamination, particularly when it exceeds 10 mils. Controlling the composition and thickness of an HDG film starts with understanding the chemistry of the member being galvanized. If the chemistry qualifies as reactive, a quality HDG film can still be achieved through controlling the immersion time, temperature, and surface profile. But if the components being galvanized have been fabricated from both reactive and non-reactive steel, tests of blast cleaning and dipping should be required to establish the best process for galvanizing, recognizing that the composition of the steel may still vary between the test section and the production pieces.
ABOUT THE AUTHOR
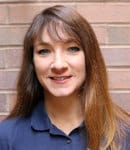
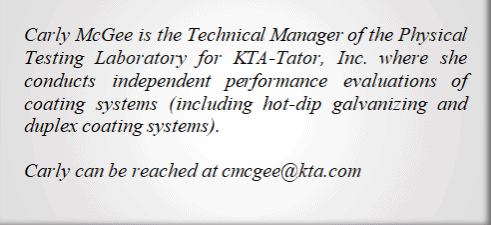
Other topics in this galvanizing series:
Topic 1 – Inspection of the galvanizing process
Topic 2 – Problems with galvanizing reactive steel
Topic 3 – Measurement of galvanizing thickness
Topic 4 – Preparation of galvanizing for painting
Topic 5 – Coatings for galvanizing
Topic 6 – Inspection of surface preparation and coating application
1American Galvanizers Association, https://galvanizeit.org/design-and-fabrication/design-considerations/steel-selection
2American Galvanizers Association, https://www.galvanizeit.org/education-and-resources/resources/technical-faq-dr-galv/peeling-vsflaking