As seen in the Fall Edition of PaintSquare Press News
The Surface Preparation Hand Tool Cleaning Standard (SSPC-SP 2) was first published as a temporary specification in August 1952 (SSPC-SP 2-52T), only two years after the Steel Structures Painting Council was founded (1950). The standard was developed primarily for maintenance of existing coating systems when loose paint, rust and/or mill scale was present and needed to be removed prior to the application of the maintenance system.
Non-powered hand tools such as chippers (hammers), scrapers and wire brushes were commonplace. Conditions St 1 and St 2 in the Swedish Pictorial Standards (SSPC VIS 1-63T), replaced by SSPC-VIS 3, Guide and Reference Photographs for Steel Surfaces Prepared by Power and Hand Tool Cleaning in 1993 were used to aid inspection personnel in visually assessing the quality of hand-tool cleaned surfaces. The standard has been revised and updated a few times in its history; the latest version was published by SSPC: The Society for Protective Coatings on Jan. 3, 2018. This version replaced the Nov. 1, 1982, version and the definition of a dull putty knife (the inspection tool to help determine conformance to the standard) refined by the SSPC Education Committee was added to the body of the Standard (Section 2, Definitions), as well as some reorganization to parallel its organization with newer power-tool cleaning standards (SSPC-SP 11 and SSPC-SP 15).
Unlike other surface preparation standards that are frequently impacted by advances in technology of the equipment used to prepare steel surfaces, there has been little advancement in the tools and equipment used for hand-tool cleaning over the past half century or so. A recent informal survey of six SSPC-certified coating contractors across the U.S. revealed the following information
There has been little, if any, significant advancement in hand tools in almost 30 years, except that the scraper went from a 3-in-1 to a 5-in-1 to a 7-in-1.
Scrapers, chisels, files and wire brushes are used for removal; sandpaper, Scotch-Brite pads and/or abrasive mesh/sheets that are available in various shapes, sizes and abrasives are used for feathering (transitioning) edges of intact coating.Most of the improvements in the tools are related to ergonomics. Handle materials, such as rubberized coating, are used to limit vibration and worker fatigue and wooden handles are replaced with plastic or other polymers on some scrapers, hammers and wire brushes. Tool selection for hand-tool cleaning should be based on what and how much needs to be removed, as well as the configuration of the surface such as:
- Flaking or loosely adhering paint – scrapers;
- Generalized rusting (painted or unpainted) – wire brushes; and
- Rusted/pitted surfaces or hard/brittle coating – hammers.
- A hammer can be extremely helpful in areas that have heavy corrosion or thick coating. A few well-placed hits can assist with removal of pack rust or help fracture an existing thick coating. The key is to look at the existing condition(s) and select what is going to work best.
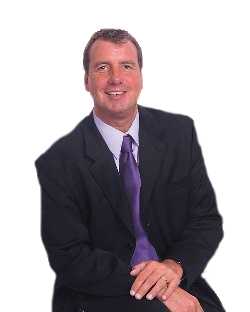
In summary, the equipment used for hand tool cleaning hasn’t evolved much in the last few decades, likely because the “tried-and-true” tools can produce surface conditions that conform to the requirements of SSPC-SP 2. If productivity is a concern, power tools can be considered since the SSPC definitions for both hand-tool cleaning and power-tool cleaning (SSPC-SP 3) are nearly identical.