Follow along with the audio article by clicking the video, or read the article as normal below.
While we are wiping and spraying surfaces in public spaces both at work and home, we are probably not considering the possibility of negative interactions with the surface materials. This article defines cleaning, disinfecting, and sanitizing, explores the potential interactions with materials, and describes methods for testing material compatibility.
Cleaning, Disinfecting and Sanitizing
Emerging pathogens or organisms that cause diseases, are an increasing public health concern. One of the greatest concerns, especially considering the current Covid-19 pandemic is pathogenic viruses (1). These viruses, such as the common cold or the norovirus, can infect and replicate within human cells and cause diseases. Pathogenic bacteria, such as MRSA and strep throat can also cause diseases, although it is estimated less than 1% of all bacteria is responsible for diseases (2). Most bacteria are harmless and beneficial. The ability of germs (e.g., viruses and bacteria) to persist on environmental surfaces can play a role in human transmission. The length of time these germs can remain viable, or “alive” on surfaces varies. For germs that remain viable on surfaces, cleaning, disinfecting, and sanitizing help prevent transmission.
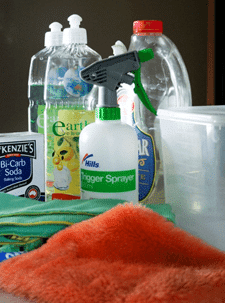
When selecting a product to minimize the number of germs on a surface or object, it is important to understand the meaning of cleaning, disinfecting, and sanitizing. The Centers for Disease Control (CDC) defines the differences between cleaning, disinfecting, and sanitizing as follows (3). Cleaning “removes germs, dirt and impurities from surfaces or objects.” Cleaning does not necessarily kill germs. Instead, it decreases the numbers of germs and, in turn, lowers the risk of spreading infection. Cleaning uses soap (or detergent) and water to physically remove germs from surfaces. Disinfecting “kills germs on surfaces or objects” using chemicals. Disinfecting surfaces after cleaning further prevents the spread of germs. Sanitizing “lowers the number of germs on surfaces or objects” to a safe level, as determined by public health standards or requirements, by either cleaning or disinfecting.
Ultimately, a disinfectant should be selected to kill germs on surfaces and prevent the spread of diseases. The market size of disinfectant manufacturing in the US is 3 billion dollars; there are many disinfectants available. Various factors must be considered before selecting a product. The product’s spectrum of activity, or germs against which it has been proven to be effective, should be researched. The product label may claim the disinfectant kills 99.99% of germs; however, the disinfectant will likely kill only a small number of strains or types of germs. The product most likely will not kill all germs on the surface being disinfected. The conditions of use should be considered as well, i.e. how quickly must the surface or object be disinfected. For the disinfectant to work properly, the recommended contact time, or length of time the surface or object must remain wet after the application of the disinfectant must be followed. Other considerations when selecting a disinfectant include ease of use, method of delivery (e.g., spray, pre-saturated wipes), requirement of a separate cleaning step (i.e., is the product both a cleaner and a disinfectant) and product stability. Mixing requirements, which may involve increased exposure times for the product user, may also be considered. Additional factors to consider include selection and proper use of other products (e.g., mops, cloths), safety (e.g., toxicity, flammability), surface compatibility, odor, and cost of the product (4).
Disinfectants are antimicrobial pesticides and must be registered with the US Environmental Protection Agency (EPA). Approval is based on the manufacturer’s submitted data on safety and effectiveness of the product. The registration does not evaluate all possible health risks of users of the products (5). Several broad categories of disinfectants are used in commercial and industrial facilities including alcohols, chlorine compounds, aldehydes, hydrogen peroxide, iodophors, phenolic compounds and quaternary ammonium compounds (6). Each of these categories comes with its own pros and cons; not all disinfectants are created equal. The active ingredient in the product that kills the targeted germs will vary between products. Other differences between disinfectants include the efficacy of the product, concentrations of its ingredients, required contact time and personal protective equipment required during use. Label language between products may also differ (e.g., green, environmentally friendly). Incorrectly using a disinfectant may kill the weaker germs but the more resistant germs can survive. However, not only should we consider the effect of the disinfectant on germs, but also the impacts of disinfectants, sanitizers, and cleaners (DSC) on the surface materials.
Material Effects
There are several issues to consider when evaluating the impacts of a disinfectant, sanitizer or cleaner on a surface material. It is difficult to simply characterize the wide range of products offered. While the “active ingredients” needed to disinfect, sanitize, or clean may be divulged, there is little information on the “inactive” ingredients that might affect materials. There are tradename products wherein derivative products sold under the same tradename are widely different in formulations. For example, a “disinfectant” with a quaternary ammonia active ingredient is also sold under the same tradename as the “disinfectant” with bleach. These are very different products. (Liquid quaternary ammonia-based products should never be mixed with “bleach” for safety reasons.) Products might be used with different application frequencies and, in fact, different products may be used sequentially with potential synergistic effects. A review of sample Safety Data Sheets (SDS) of some products reveals:
- Product pH ranging from 2-3 (buffered hydrogen peroxide) to 12.8-13.2 (buffered “bleach” solutions).
- Products containing 1-5% sodium chloride (i.e., salt water).
- Products containing from 5% to 99% concentrations of different alcohols.
The widespread application of products will have the potential for noticeable impacts, especially when used to treat an area never designed to be exposed to any liquid in a fog or aerosol form. This may be the case with office spaces or living quarters. Obvious concerns include likely cosmetic corrosion of unprotected metallic surfaces or functional corrosion effects on electronics. Non-metallic materials and paints may also be impacted by surface discoloration, softening, or swelling depending on the product and exposure time.
More specifically regarding metallic corrosion, the longer term (or repeated) exposure can create corrosion problems on amphoteric materials such as aluminum alloys. Oxidizing products such as “bleach” or peroxides can supporting pitting or crevice corrosion on susceptible stainless steel and other active / passive materials. Products with noble metal cations (e.g., silver) can plate onto more active surfaces such as steel, zinc (galvanizing), or aluminum and support enhanced localized corrosion.
Certain products can affect non-metallic surfaces. Non-metallics encompass a large range of products. Computer screens, especially the more common touch screens, can be impacted by more concentrated alcohol and ammonia containing products. Some thermoplastic products (e.g., acrylics, PVC) can be impacted more than thermosetting materials (e.g., epoxy).
In all cases, for more than infrequent applications, critical metallic and non-metallic materials should be evaluated for continued treatment to ensure long-term reliability.
Testing the Material Compatibility
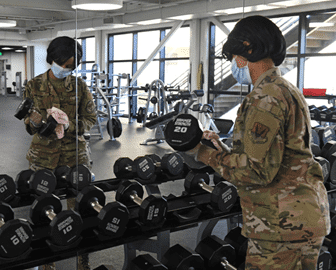
The number of possible disinfectant / material interactions is large. A study showed that there are 15 surfaces with different materials within three feet of a hospital patient’s bed (7). Similarly, there are several potential surfaces in any environment with a high population density such as a cruise ship or college dorm. While manufacturers may test compatibility of their product with generic chemicals such as alcohol or acids, they are unlikely to have tested all the disinfectants that they may encounter. There are several established methods for testing the compatibility of metals and non-metallic materials with specific disinfectants.
The simplest test for metals is to immerse the metal in the disinfectant of concern. NACE TM0169/ ASTM G31 “Standard Guide for Laboratory Immersion Corrosion Testing of Metals” provides guidance on the parameters such as oxygen concentration or alloying elements that effect laboratory corrosion especially for mass loss coupons. The method specifically does not include evaluation of localized attack or stress corrosion cracking (SCC) in which susceptible alloys prematurely crack in the presence of a tensile stress and a corrosive environment.
In SCC testing the samples are loaded in tension, exposed to a corrosive environment, and evaluated for the formation of cracks (8). There are two types of specimens, smooth and pre-cracked or notched. The latter allow for shorter tests times, while the smooth samples allow for the evaluation of crack initiation and propagation.
The samples can be loaded in tension by holding them in a fixture or using a mechanical testing machine. The fixtures can be a simple 2, 3 or 4-point bend, a C-bend or U-bend as described in ASTM G30 “Standard Practice for Making and Using U-Bend Stress-Corrosion Test Specimens.” The bend fixtures are simple to use and are good for evaluating susceptibility to SCC or generating a large sample population for statistical significance. However, there are many advantages to using a mechanical test machine. When the sample is loaded in one direction the stress state is uniform and more simply calculated. The machines allow for quantitative load that can be constant or increasing. This method of testing is described in ASTM G49 “Standard Practice for Preparation and Use of Direct Tension Stress-Corrosion Test Specimens.”
Similar concerns exist for non-metallic materials that can soften, discolor, swell or embrittle. Testing ranges from simple chemical exposures to exposures coupled with simulated wiping to extensive protocols incorporating mechanical testing post-exposure. The simplest test involves allowing a cotton ball soaked in liquid disinfectant to contact the test material. ASTM D1308 “Standard Test Method for Effect of Household Chemicals on Clear and Pigmented Organic Finishes” provides a method for conducting these so called “spot tests.” These tests can be conducted open or covered with a watch glass covering the soaked cotton ball during exposure.
More aggressive protocols have been developed to simulate the constant wiping associated with real world disinfection in part because bacteria have been observed on the grooves created by the abrasive action of surface wiping. One method involves 200 manual wipes with a laboratory tissue to simulate 6-months of cleaning and disinfecting. The tissues are soaked in disinfectants diluted according to the manufacturer’s specification and at off-label concentrations to simulate worse case scenarios (9).
Eastman Chemical Company has developed a comprehensive program that tests for embrittlement. The samples are held in a fixture loaded to a known strain level like the SCC tests previously described for metals. The samples are examined for cracking after exposure to the disinfectant. In addition, the exposed samples are tested for impact strength. By comparing the impact strength of the exposed sample to an unexposed control, the material can be tested for susceptibility to embrittlement even before cracking has initiated (10).
Based on testing of various cleaning and disinfecting products, the appropriate product can be matched with the materials in the environment or application to avoid material degradation.
About the Authors:
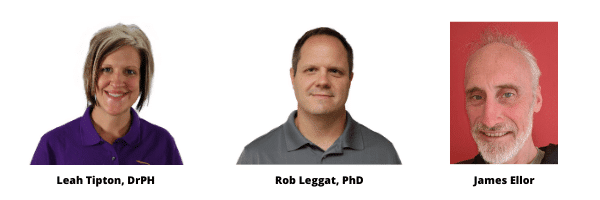
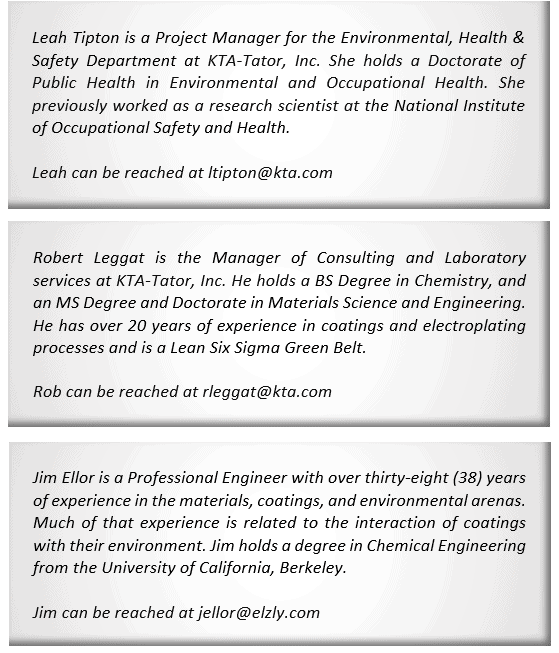
Sources:
(1) Environmental Protection Agency. (2016, August 19). Guidance to Registrants: GUIDANCE TO REGISTRANTS: PROCESS FOR MAKING CLAIMS AGAINST EMERGING VIRAL PATHOGENS NOT ON EPA-REGISTERED DISINFECTANT LABELS. https://www.epa.gov/sites/production/files/2016-09/documents/emerging_viral_pathogen_program_guidance_final_8_19_16_001_0.pdf
(2) NCBI. (2019, August 29). What are Microbes? https://www.ncbi.nlm.nih.gov/books/NBK279387/
(3) Center for Disease Control. (2018, July 31). How To Clean and Disinfect Schools To Help Slow the Spread of Flu. https://www.cdc.gov/flu/school/cleaning.htm
(4) Center for Disease Control. Environmental Cleaning and Disinfection: Principles of Infection Transmission and the Role of the Environment. https://www.cdc.gov/infectioncontrol/pdf/strive/EC102-508.pdf
(5) Center for Disease Control. Green Cleaning, Sanitizing, and Disinfecting: A Curriculum for Early Care and Education. https://www.epa.gov/sites/production/files/documents/ece_curriculumfinal.pdf
(6) Center for Disease Control. (2008). Chemical Disinfectants. Guideline for Disinfection and Sterilization in Healthcare Facilities. https://www.cdc.gov/infectioncontrol/guidelines/disinfection/disinfection-methods/chemical.html
(7) K.M. Pyrek “Disinfectants and Surface Compatibility”, Infection Control Today, April 2016.
(8) G. Koch “Tests for Stress-Corrosion” Advanced Materials and Processes, August 2001.
(9) Jo et al. Antimicrobial Resistance and Infection Control (2019) 8:24 https://doi.org/10.1186/s13756-019-0467-9
(10) N. Sparrow “Simple four-step test evaluates long-term resistance of plastics to hospital disinfectants” Plastics Today, February 17, 2017