The Construction Specifications Institute (CSI) provides a format for preparing specifications that is often adopted for use in the coatings industry. It contains three primary sections, including General, Products and Execution. The Products section typically contains the specified coating system. There are several ways that a coating system can be specified, one of which is “Trade name, or equal.” But what exactly does “or equal” mean? It’s not quite as simple as choosing another coating of the same generic resin type, for example substituting the specified urethane topcoat for a less expensive urethane topcoat, and considering it “equal” since both products contain a polyurethane resin.
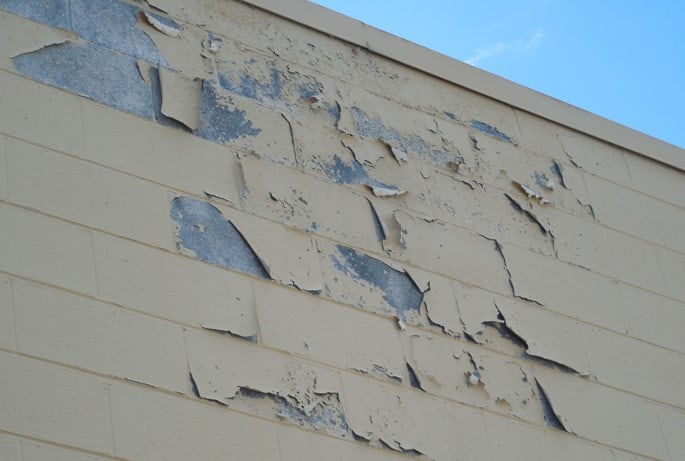
Unlike the world of “designer” and “generic” prescriptions, opting for a less expensive coating may not provide the same long term performance. Less expensive formulations may not have the same protective properties as the higher priced materials since the raw materials used to manufacture the coating may be of lesser quality. Selecting a less expensive product that on the surface appears to be an “equal” may result in application difficulties and poor hiding (requiring multiple coats), or premature deterioration such as color shift, gloss reduction, chalking, erosion, delamination, or corrosion of the substrate due to a lack of film integrity. That is why selecting a coating that can withstand the demands of the service environment is of utmost importance to a successful project.
Comparing manufacturer’s product data sheets (PDS) and safety data sheets (SDS) can reveal some information about the formulation of the coating, including the type and concentration of raw materials used (listed on the SDS), the volume solids content, weight per gallon (density) and performance characteristics (may or may not all be listed on the PDS); however, these documents rarely reveal enough information to make an accurate assessment of “equality.” In fact, a raw material used at less than 1% in the formulation of a coating does not have to be listed on the SDS unless it is carcinogenic. Yet this relatively small percentage of a given material may contribute to performance properties of the applied coating, depending on what it is. So, while these documents can supplement an “or equal” assessment, they typically should not be the sole source of information.
Selecting a Generic Coating System
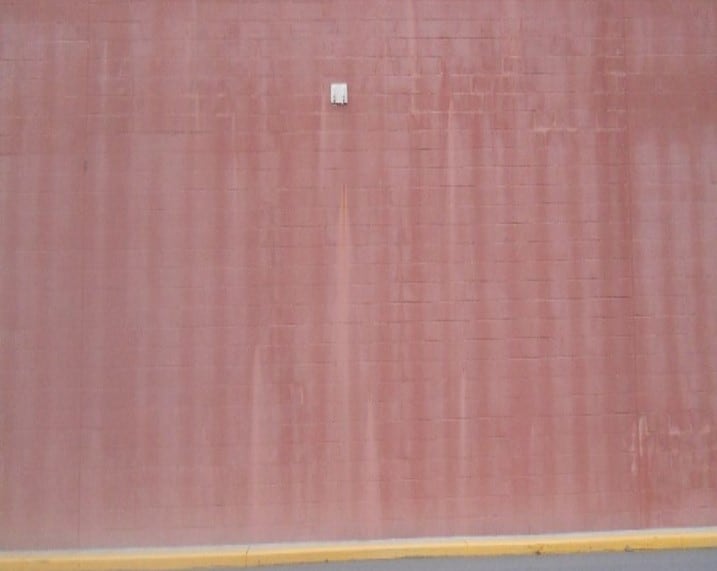
The selection of the appropriate generic coating system is a prerequisite to performing an “or equal” assessment. One of the first and most important steps when trying to select an appropriate coating system is to identify the specific service environment and its unique characteristics. For example, exterior exposure will dictate the selection of a finish coat that is resistant to solar radiation (sunlight in the ultraviolet region of the spectrum); otherwise the resin will be quickly degraded and chalking will occur. The simplest way is to select a generic coating system that has a track record of successful performance in similar environments. For example, the common coating system with a proven track record of successful performance for a new steel bridge, or an existing steel bridge that is scheduled for removal and replacement of the existing coating system includes a zinc rich primer (inorganic for new steel and organic for existing steel, since it is easier to apply in the field), an epoxy midcoat and a polyurethane topcoat. The zinc rich primer provides both barrier and galvanic protection to the steel, the epoxy midcoat adds additional thickness and barrier protection and the urethane topcoat provides the protection from solar radiation (sunlight). Selecting a system that would be “equal” to this system lies more in the performance of the system than in the three coats generically described. That is, the selection of a two-coat system consisting of 3 – 5 mils of a zinc rich primer and 6 – 9 mils of a polyaspartic finish coat may perform just as well, but may or may not be considered equivalent.
But how do you know what performance characteristics to look for? Think about what the coating(s) will experience throughout the life of the system. Will there be prolonged exposure to water or moisture? Will the system be in contact with various chemicals? Will it encounter abrasion from foot traffic, forklifts, or other sources? Will it be exposed to high temperatures? Once the obstacles that the coating system will encounter throughout the service life are defined, it’s a little easier to identify which characteristics the system should possess. There is no shortage of testing that can be performed to assess various properties of coatings (in order to determine whether they are candidates for use), so it is important to have a focused approach and evaluate the performance properties that are most applicable. For example, subjecting a coating to salt fog exposure that is intended for use on a concrete floor in a warehouse will have little value, even though it is a common test to comparatively evaluate coating system performance for marine/coastal exposures, or on structures that will be exposed to deicing materials. Rather, abrasion resistance is a key consideration when considering systems for this environment.
Use of Industry Standards for Evaluating Coating Performance
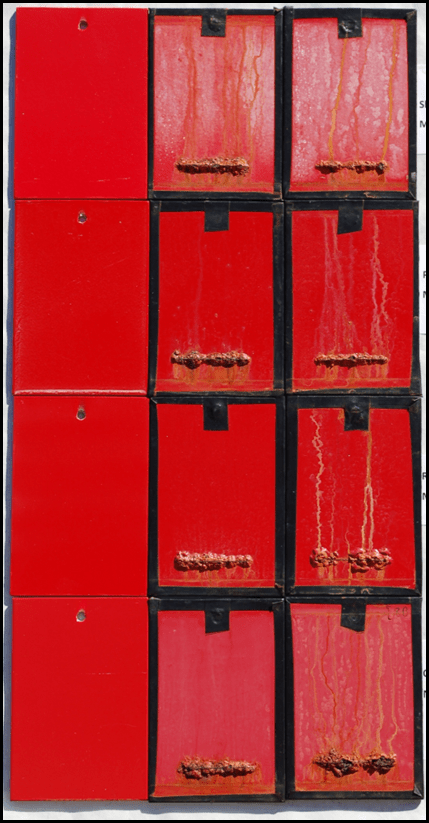
One way to determine the suitability of a coating system for a given environment is to evaluate candidate systems according to an industry standard test regime. For example, the American Water Works Association (AWWA) has published standard ANSI/AWWA C222, “Polyurethane Coatings for the Interior and Exterior of Steel Water Pipe and Fittings.” This standard outlines required performance data for a defined service environment. It contains tests appropriate to the service environment, including resistance to cathodic disbondment, flexibility, impact resistance, abrasion resistance, chemical resistance, dielectric strength, water absorption, hardness and tensile adhesion. These properties were determined to be of highest importance for a coating in this service environment by the committee that wrote the standard. It is important to note that ANSI/AWWA C222 represents a standard and not a specification. It does not indicate a particular coating or coating system that should be used, but rather parameters that need to be met.
Each of the tests listed above provides a minimum or maximum value (as appropriate) that must be met by any coating being considered for use. Once again, the acceptance criteria were established by the committee who wrote the standard. For example, if the coating does not have a minimum Shore D hardness of 65 units, it would not be considered an appropriate coating by the scope of this standard, since the hardness of the coating was determined to be critical performance property. Standards like this may be referenced in a project specification as, “Product X or equal has been found to be suitable as determined by ANSI/AWWA C222.” A statement such as this one in a specification defines the performance requirements of the coating system, thereby establishing what is considered “equal.” As long as the coating manufacturer can show evidence of testing according to the requirements established by the testing standard, and the results of the testing meet the minimum acceptance criteria that coating system is considered acceptable for use.
Determining “Or Equal” Based on Comparing Existing Data
Frequently owners and specifiers do not have the luxury of time and/or money to establish a test regime and/or perform long term testing to compare candidate systems and determine equivalency.
So, another way to determine the suitability of a coating system is to compare existing data. Here is a suggested approach:
- Ensure that the generic resin type(s) of the recommended coating system and the candidate coating system are the same;
- Compare recommended dry film thicknesses, number of coating layers and application methods;
- Review any data provided by a laboratory (preferably independent to remove any bias) that indicates physical performance characteristics. Often, the tests that are most applicable for the service environment can be found on the PDS. There are many physical tests that can be performed and reported, so concentrate on reviewing data that is most relevant to the anticipated exposure environment; and
- Consider field performance history data. This is more valuable than laboratory-generated performance data because it reveals how the coating performs in an actual service environment as opposed to a simulated one. Field performance history data can be requested from the coating manufacturer along with contact information for the facility owner to verify the data.
Independent of the information or data gathered, whether from testing programs, product data sheets, or field performance history, the pros and cons of the candidate systems should be carefully considered prior to selection, along with the level of expertise offered by the manufacturer’s technical support staff.
Thanks for an interesting article. The comparison of course can be quite time consuming and so a practical first step should always be to verify that the specification writer does actually wish for an equal / equivalent product to be put forward and is not just complying with company policy regarding listing singular trade names. A lot of time can be wasted providing supporting information for an equal recommendation that is unlikely to be accepted as the specification writer already has a strong preference, good experience etc.
Simon,
The following is a message from the Author, Chrissy Stewart:
Thank you for you thoughtful comment. You are correct, the specification writer should first confirm that an equivalent product is desired, otherwise it would be a less than constructive use of time.