Coating Condition Assessment Services
Are you looking for an Assessment of Coating/Lining Conditions?
Managing and planning repairs, renovations and other maintenance needs of coating systems on industrial structures can be a daunting task. A thorough assessment of current coating conditions provides the necessary information for determining the most cost-effective maintenance strategy. Subsequent selection of coating materials and corresponding levels of surface preparation for the chosen maintenance strategy are equally important in protecting fixed assets. And none of the results of the first two steps are of value unless communicated effectively through a performance-based technical specification to prospective contractors so that desired outcomes are achieved.
Our Project Engineers provide assessments of critical factors that are known to impact coating system longevity and performance. While KTA’s coating condition assessments are based on applicable industry standards (e.g., ASTM, NACE, SSPC), our approach to integrating coating condition assessments, opinions of probable cost and specification development has been developed from decades of experience on a vast array of industrial structures and facilities. In fact, we have assessed the condition of over 150 facilities in 10 industries in the past 3 years alone. KTA does not manufacture or sell coatings and we do not apply coatings. So our corrosion surveys/coating condition assessments and the resulting recommendations are engineering-based and without bias.
KTA’s Coating Condition Assessment Services Help Answer the Following:
Why Use KTA to Assess the Condition of your Installed Coatings/Linings?
The cornerstone of KTA’s approach entails an evaluation of the existing condition of coating (e.g., visible coating deterioration/corrosion, coating thickness, coating adhesion, surface preparation, toxic metal content) applied to representative major components/elements of a structure. The structure is analyzed in order to identify deterioration patterns so that alternative remediation strategies like spot repair and zone painting can be considered along with total removal and replacement. But we don’t make recommendations without considering our client’s objectives and concerns, like equipment or staging limitations, facility operations, and other factors that may impact maintenance decisions.
Once the desired maintenance options are identified, KTA’s professional staff begins the process of preparing independent opinions of probable cost (an opinion of likely bid ranges for the recommended repair options), based upon guidance from the Association for the Advancement of Cost Engineering (AACE). After the maintenance strategy is selected, KTA can develop a performance-based, project-specific technical specification outlining required aspects of surface preparation and coatings application necessary to achieve the desired end product. And we can assist with management of the bidding process, contractor selection and provide third party quality assurance inspection to verify that the contractor is controlling the quality of the work. In fact, KTA employs the most NACE-certified coatings inspectors in the US (over 150), and is an SSPC-QP 5 certified coatings inspection agency.
KTA provides a turnkey coatings engineering service that covers both the design and construction phases of a project:
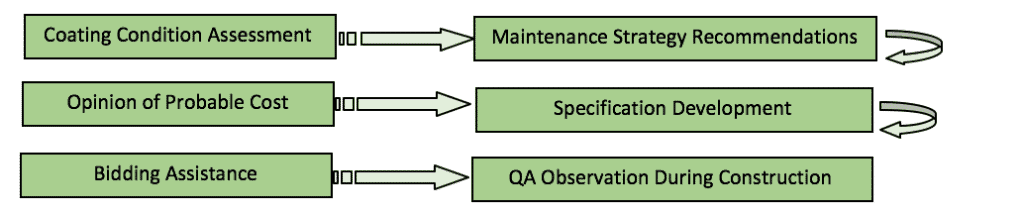
Contact our Condition Assessment Group:
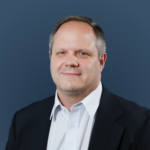